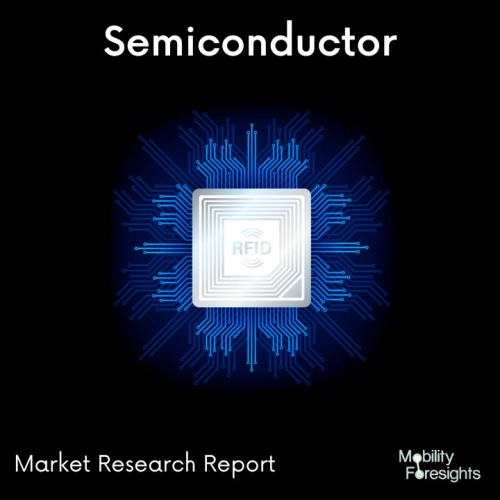
- Get in Touch with Us
Last Updated: Apr 25, 2025 | Study Period: 2023-2030
Dry etching is now employed in semiconductor fabrication procedures due to its superior ability to undertake anisotropic etching (material removal) to build high aspect ratio structures (e.g. deep holes or capacitor trenches) over wet etching.
The technique of eliminating a masking pattern of semiconductor material by hitting it with ions is known as dry etching, sometimes known as plasma etching. A plasma of reactive gases, such as oxygen, boron, fluorocarbons, chlorine, and trichloride, often makes up the ions.
After metallographic grinding and polishing procedures, etching is a chemical or electrolytic process used. Using etching to increase surface contrast will allow you to see the microstructure or macrostructure.
The Global Dry-etching exhaust gas treatment equipment market accounted for $XX Billion in 2022 and is anticipated to reach $XX Billion by 2030, registering a CAGR of XX% from 2023 to 2030.
Factor Design for the Oxide Etching Process to Reduce Edge Particle Contamination in Capacitively Coupled Plasma Etching Equipment. Particles stuck to the wafer edge by capacitively coupled plasma etching equipment during the oxide layer etching procedure result in flaws that lower the yield of semiconductor wafers.
Adjusting the voltage and temperature of the electrostatic chuck, the plasma discharge sequence, the gas flow, and the pressure parameters during the etching process to lessen edge particle contamination in plasma etching equipment. By examining particle maps after wafer etching, the proposed edge particle reduction method was created.
By lowering the voltage and temperature variations of the electrostatic chuck and producing a plasma sheath with a continuous discharge sequence of radio-frequency plasma, edge particle adhesion in plasma etching equipment may be decreased.
The quantity of wafer edge particles is also influenced by the gas pressure and flow rate. The equipment settings were improved using experimental data in order to decrease edge particle contamination and enhance edge wafer defects after dry etching.
Sl no | Topic |
1 | Market Segmentation |
2 | Scope of the report |
3 | Abbreviations |
4 | Research Methodology |
5 | Executive Summary |
6 | Introduction |
7 | Insights from Industry stakeholders |
8 | Cost breakdown of Product by sub-components and average profit margin |
9 | Disruptive innovation in the Industry |
10 | Technology trends in the Industry |
11 | Consumer trends in the industry |
12 | Recent Production Milestones |
13 | Component Manufacturing in US, EU and China |
14 | COVID-19 impact on overall market |
15 | COVID-19 impact on Production of components |
16 | COVID-19 impact on Point of sale |
17 | Market Segmentation, Dynamics and Forecast by Geography, 2022-2030 |
18 | Market Segmentation, Dynamics and Forecast by Product Type, 2022-2030 |
19 | Market Segmentation, Dynamics and Forecast by Application, 2022-2030 |
20 | Market Segmentation, Dynamics and Forecast by End use, 2022-2030 |
21 | Product installation rate by OEM, 2022 |
22 | Incline/Decline in Average B-2-B selling price in past 5 years |
23 | Competition from substitute products |
24 | Gross margin and average profitability of suppliers |
25 | New product development in past 12 months |
26 | M&A in past 12 months |
27 | Growth strategy of leading players |
28 | Market share of vendors, 2022 |
29 | Company Profiles |
30 | Unmet needs and opportunity for new suppliers |
31 | Conclusion |
32 | Appendix |