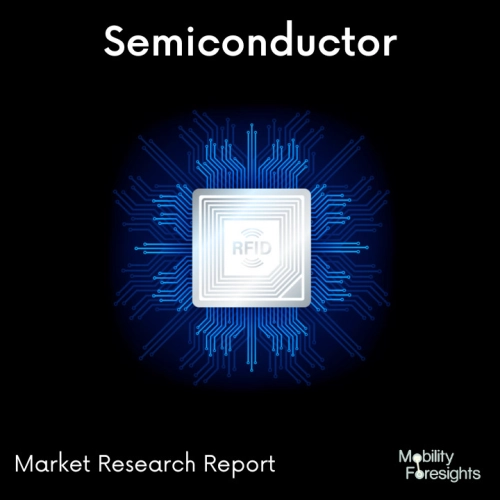
- Get in Touch with Us
Last Updated: Apr 26, 2025 | Study Period: 2023-2030
A dry film laminator designed specifically for use in research and development departments, schools, and small businesses. The mold-etching part technique can be processed with any commercial laminate.
Application of a solder mask is also possible without difficulty thanks to the adjustable laminating speed and pressure control. two hot-roll laminators that are made to apply dry film photo-resist sheets to a wide range of materials, including stainless steel, copper, and PCB laminates. They can also apply to process wafers quickly and easily. The coating, calendering, and machine presses all play a role.
Choose from pouch laminators, roll laminators, cold laminators, and film laminators as your laminating options. Compared to thermal processing or hot lamination, cold lamination is much simpler.
With such a machine, the primary goal of laminating is to protect or embellish printed documents or images. From pouch laminators used in offices to industrial-sized heated roll laminators, the sizes of heated roll laminators can vary.
The Global dry film lamination equipment market accounted for $XX Billion in 2022 and is anticipated to reach $XX Billion by 2030, registering a CAGR of XX% from 2023 to 2030.
The RLM is a dry film laminator designed specifically for use in research and development departments, small businesses, and schools. The mold-etching part technique can be processed with any commercial laminate. Application of a solder mask is also possible without difficulty thanks to the adjustable laminating speed and pressure control.
The RLM is a dry film laminator designed specifically for use in research and development departments, small businesses, and schools. The mold-etching part technique can be processed with any commercial laminate.
Application of a solder mask is also possible without difficulty thanks to the adjustable laminating speed and pressure control. The machine is also used extensively in wafer masking, smt stencil production, and metal working, among other applications.
As a medium for 3D printing, LOM technology makes use of adhesive-coated paper, plastic, or metal laminates. Using a knife or a laser cutter, these material sheets are joined layer by layer before being shaped. After the LOM process has been completed, the objects can be further modified through machining or drilling.
The actual structure of laminate flooring is four layers; design, the back layer, wear, and the core The layers are fused together with a lot of pressure and high heat for a specific purpose.
The heated rollers of a heated roll laminator melt the glue that has been extruded onto the lamination film. Pressure rollers are used to apply this film to a substrate like card or paper. With such a machine, the primary goal of laminating is to protect or embellish printed documents or images.
Sl no | Topic |
1 | Market Segmentation |
2 | Scope of the report |
3 | Abbreviations |
4 | Research Methodology |
5 | Executive Summary |
6 | Introduction |
7 | Insights from Industry stakeholders |
8 | Cost breakdown of Product by sub-components and average profit margin |
9 | Disruptive innovation in the Industry |
10 | Technology trends in the Industry |
11 | Consumer trends in the industry |
12 | Recent Production Milestones |
13 | Component Manufacturing in US, EU and China |
14 | COVID-19 impact on overall market |
15 | COVID-19 impact on Production of components |
16 | COVID-19 impact on Point of sale |
17 | Market Segmentation, Dynamics and Forecast by Geography, 2023-2030 |
18 | Market Segmentation, Dynamics and Forecast by Product Type, 2023-2030 |
19 | Market Segmentation, Dynamics and Forecast by Application, 2023-2030 |
20 | Market Segmentation, Dynamics and Forecast by End use, 2023-2030 |
21 | Product installation rate by OEM, 2023 |
22 | Incline/Decline in Average B-2-B selling price in past 5 years |
23 | Competition from substitute products |
24 | Gross margin and average profitability of suppliers |
25 | New product development in past 12 months |
26 | M&A in past 12 months |
27 | Growth strategy of leading players |
28 | Market share of vendors, 2023 |
29 | Company Profiles |
30 | Unmet needs and opportunity for new suppliers |
31 | Conclusion |
32 | Appendix |