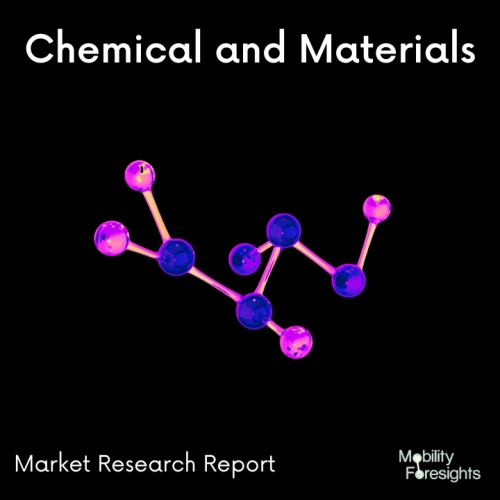
- Get in Touch with Us
Last Updated: Apr 25, 2025 | Study Period: 2024-2030
An electron beam is used in a metal deposition by an e-beam to heat the target material and sufficiently raise its vapor pressure in a vacuum.
The production of an e-beam involves either thermionic emission (heating a filament to a temperature high enough to extract electrons) or field emission (using a high electric field to extract electrons).
E-beam is accelerated with the help of a controlled electric and magnetic field, then directed towards the target material.
Typically, the material is stored inside or on top of the crucible in the shape of little pellets, such as those measuring 1 mm (e.g. Boron Nitride ceramic).
In order to keep the crucible from heating up, water is kept at a cold temperature underneath. The material for the crucible is chosen such that it has a greater melting point and does not combine with the material of interest to form an alloy.
The evaporated substance is subsequently applied to the desired substrate. The majority of evaporated material is guaranteed to be deposited on the substrate of interest due to the high mean free path in a vacuum.
The process of building a three-dimensional object from a CAD model or digital 3D model is known as additive manufacturing or E-Beam Metal Additive Manufacturing 3D Printer.
It can be done via a variety of procedures in which material is combined together, connected, or solidified under computer control, usually layer by layer (such as fusing plastics, liquids, or powder grains).
At the time, the phrase "rapid prototyping" was more fitting because 3D printers or printing techniques were thought to be solely useful for producing functional or aesthetically pleasing prototypes.
The terms additive manufacturing and 3D printing can be used interchangeably because of the advancements in 3D printing's accuracy, repeatability, and material selection, which have led to some 3D printing techniques being viewed as viable as industrial production technologies.
The Global E-Beam Metal Additive Manufacturing 3D Printer market accounted for $XX Billion in 2023 and is anticipated to reach $XX Billion by 2030, registering a CAGR of XX% from 2024 to 2030.
Wayland Additive, a manufacturer of original equipment (OEM) metal additive manufacturing (AM) systems, its production has been scaled up as intended so far.
This includes Wayland's initial transfer of its star E-Beam Metal Additive Manufacturing 3D Printer Calibur3 machine, which it initially sold to the Exergy Solutions energy engineering firm in Canada.
The Calibur3 relies on Wayland's exclusive NeuBeam technology, an electron-beam melting (EBM) AM technique.
The fundamental advantage of Wayland's EBM over rivals is that the former heats only the powder being printed, as opposed to the entire powder bed.
This keeps a "sinter cake" from forming during the production process along with the printed item, substantially simplifying the post-processing stage.
Sl no | Topic |
1 | Market Segmentation |
2 | Scope of the report |
3 | Abbreviations |
4 | Research Methodology |
5 | Executive Summary |
6 | Introduction |
7 | Insights from Industry stakeholders |
8 | Cost breakdown of Product by sub-components and average profit margin |
9 | Disruptive innovation in the Industry |
10 | Technology trends in the Industry |
11 | Consumer trends in the industry |
12 | Recent Production Milestones |
13 | Component Manufacturing in US, EU and China |
14 | COVID-19 impact on overall market |
15 | COVID-19 impact on Production of components |
16 | COVID-19 impact on Point of sale |
17 | Market Segmentation, Dynamics and Forecast by Geography, 2024-2030 |
18 | Market Segmentation, Dynamics and Forecast by Product Type, 2024-2030 |
19 | Market Segmentation, Dynamics and Forecast by Application, 2024-2030 |
20 | Market Segmentation, Dynamics and Forecast by End use, 2024-2030 |
21 | Product installation rate by OEM, 2023 |
22 | Incline/Decline in Average B-2-B selling price in past 5 years |
23 | Competition from substitute products |
24 | Gross margin and average profitability of suppliers |
25 | New product development in past 12 months |
26 | M&A in past 12 months |
27 | Growth strategy of leading players |
28 | Market share of vendors, 2023 |
29 | Company Profiles |
30 | Unmet needs and opportunity for new suppliers |
31 | Conclusion |
32 | Appendix |