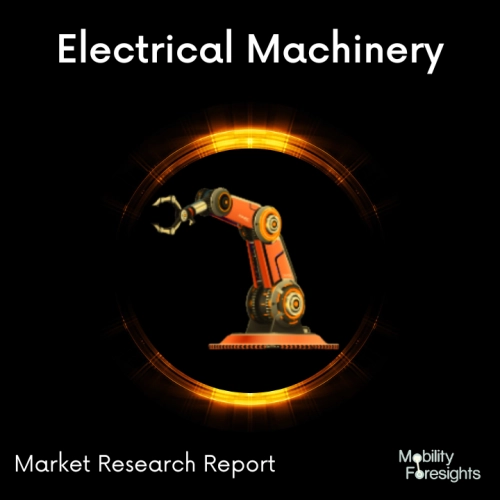
- Get in Touch with Us
Last Updated: Apr 25, 2025 | Study Period: 2023-2030
drill a hole A highly specialised technique called EDM (electrical discharge machining) machining was created to drill tiny, deep holes into conductive materials.A revolving hollow electrode is lowered into the material to be drilled in order for it to operate.
EDM hole drilling produces quick and accurate machining of small deep holes in conductive metals by using an energised spinning tube electrode with high pressure flushing.
EDM hole popping services to suit any industry or application's requirements. A great choice for any industrial machining project is CNC EDM popping because of its high precision and capacity to work with tough materials.
The process of electrical discharge machining (EDM) involves repeatedly subjecting material to controlled electric discharge. It operates using the thermoelectric effect. Thermal energy is produced on a workpiece as a result of the electric discharge that occurs between an electrode/wire and the workpiece.
Brass, copper, and copper-tungsten are also frequently used as EDM tool materials. With the use of graphite electrodes and a power supply of 30 A at a frequency of roughly 3000 kHz, the least amount of tool wear is possible in EDM.
To reduce actual tool wear, a steel coating is applied to graphite electrode tools. For the purpose of creating moulds and dies as well as fabricating automotive or aerospace components, electrically conductive and hard materials are machined using EDM. Low material removal rate (MRR) and high surface roughness are properties of EDM (SR).
The Global EDM Hole Drilling machine market accounted for $XX Billion in 2022 and is anticipated to reach $XX Billion by 2030, registering a CAGR of XX% from 2023 to 2030.
To facilitate drilling duties on large components, the Engineering Technology Group (ETG) introduces the Winbro HSD6-GT High-Speed EDM Drilling System from Winbro Group Technologies.
With a linear and rotational accuracy of 0.015 mm and 0.007°, respectively, the next-generation Winbro HSD6-GT exhibits precision and repeatability.
It delivers 0.010 mm of linear repeatability and 0.003° of rotating reproducibility. According to the business, this degree of accuracy can be attributed to a number of integrated advancements, including the proprietary 6-point probing technology and optical on-machine inspection.
The innovative 6-point probing technology enables precision positioning with only basic fixturing devices and provides accurate location of the component prior to drilling.
A laser opticator that offers comprehensive optical on-machine inspection to ensure precise hole location works in conjunction with this to complete the setup.
While the Winbro HSD6-GT's precision performance is supported by its laser opticator and 6-point probing system, its integrated signature analysis system checks drilling performance in real-time to minimise the need for manual inspection. The combination of these fascinating technologies gives the end-user total process control and trust.
Sl no | Topic |
1 | Market Segmentation |
2 | Scope of the report |
3 | Abbreviations |
4 | Research Methodology |
5 | Executive Summary |
6 | Introduction |
7 | Insights from Industry stakeholders |
8 | Cost breakdown of Product by sub-components and average profit margin |
9 | Disruptive innovation in the Industry |
10 | Technology trends in the Industry |
11 | Consumer trends in the industry |
12 | Recent Production Milestones |
13 | Component Manufacturing in US, EU and China |
14 | COVID-19 impact on overall market |
15 | COVID-19 impact on Production of components |
16 | COVID-19 impact on Point of sale |
17 | Market Segmentation, Dynamics and Forecast by Geography, 2023-2030 |
18 | Market Segmentation, Dynamics and Forecast by Product Type, 2023-2030 |
19 | Market Segmentation, Dynamics and Forecast by Application, 2023-2030 |
20 | Market Segmentation, Dynamics and Forecast by End use, 2023-2030 |
21 | Product installation rate by OEM, 2023 |
22 | Incline/Decline in Average B-2-B selling price in past 5 years |
23 | Competition from substitute products |
24 | Gross margin and average profitability of suppliers |
25 | New product development in past 12 months |
26 | M&A in past 12 months |
27 | Growth strategy of leading players |
28 | Market share of vendors, 2023 |
29 | Company Profiles |
30 | Unmet needs and opportunity for new suppliers |
31 | Conclusion |
32 | Appendix |