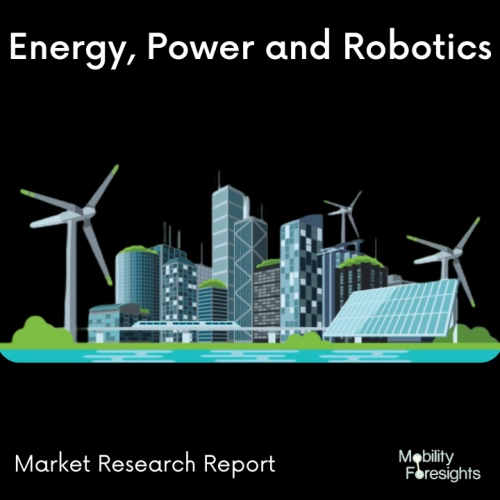
- Get in Touch with Us
Last Updated: Apr 25, 2025 | Study Period: 2023-2030
Heat shrink tubing, commonly known as electrical shrink tubing, is an important protective and organizational component found in a variety of electrical arrays.
Heat shrink tubing, in general, is a ubiquitous component in most electrical setups that insulates electrical components from external elements such as moisture, dust, abrasion, and sharp objects that may otherwise damage cables and electrical components.
This form of degradation eventually leads to shorts and failures. It will also connect loose wires, connections, joints, terminals, and splices, resulting in better organized and manageable bundles.
Heat shrink tubing is a thermoplastic tube that shrinks when heated. When heat shrink tubing is wrapped over wire arrays and electrical components, it shrinks radially to suit the shapes of the equipment, forming a protective coating.
It may protect against abrasion, mild impact, cuts, moisture, and dust by covering sections of individual wires or bundling complete arrays.
To make heat shrink tubing, plastic manufacturers first extrude a thermoplastic tube. The materials used in heat shrink tubing vary based on the intended purpose.
After the necessary plastic has been extruded, the material is heated and pushed to expand, increasing the diameter of the tube. The inflated tube is allowed to cool to ambient temperature before being set.
This extended thermoplastic tube is then heated to a precise temperature and wrapped around the wires or other required components. The heat softens and shrinks the tube back to its original extruded size, trapping the wires or other components behind a tight coating of protective plastic.
Heat shrink tubing offers electrical insulation, mechanical protection, environmental sealing, and strain relief. Heat shrinkable tubing is available in single and dual wall configurations and is designed for use in a variety of applications such as back-end connector sealing, breakouts, and connector-to-cable transitions.
It is a viable alternative to taping, molding, or potting. When heated, heat sleeves adapt to the size and shape of the substrate beneath, allowing for rapid and easy installation. Because of its high expansion ratio, it is easy to replace most damaged cable jackets without removing connections.
Heat shrink tubing comes in a variety of materials, colors, and sizes and is provided in spools and chopped sections. Clear kinds allow for examination of covered components and have high light transmittance.
Heat shrink tubing materials may protect and organize wires, connections, and other electrical components in low-impact domestic applications as well as heavy-duty industrial environments.
Consolidated Electronic Wire and Cable provides a broad assortment of heat-shrink coated wires, cables, and components to fulfill the demands of practically any application.
The Egypt Heat Shrink Tubing Market accounted for $XX Billion in 2022 and is anticipated to reach $XX Billion by 2030, registering a CAGR of XX% from 2023 to 2030.
Raychem heat shrink technology has been developed by TE Connectivity for energy applications. Heat shrink technique is based on specifically developed thermoplastic polymer ingredients, which helps optimize the product for applications.
Products are recognised for their excellent quality, dependability, and capacity to survive weathering processes such as pollution and contamination, UV-light, salt fog, and other hostile conditions. TE's outstanding heat shrink products are the foundation of a highly dependable cable accessory product portfolio.
Because of the extensive process controls used during the production of heat shrink tapes, tubing, wraparound sleeves, splices and terminations, they will retain their shape memory off the shelf for decades and work robustly in the field for years following installation.
Junkosha was the first business to include natural peelability into typical FEP heat shrink tubing used for reflow, laminating, masking, and heat sealing of different medical components. As a consequence, users of PHST system may effortlessly remove the heat shrinkable tubing by hand; no training or skiving with razor blades required.
It was noted for its great inherent peelability for simple removal following the heat shrinking process, and removal does not require any training or equipment, which considerably improves product throughput and reduces manufacturing costs.
It eliminates skiving operations, which greatly improves yield rates while protecting underlying, more expensive components from blade damage. It has a high shrink ratio type with regulated shrinking and elongation, as well as clear and coloured kinds with increased interior visibility.
Sl no | Topic |
1 | Market Segmentation |
2 | Scope of the report |
3 | Abbreviations |
4 | Research Methodology |
5 | Executive Summary |
6 | Introduction |
7 | Insights from Industry stakeholders |
8 | Cost breakdown of Product by sub-components and average profit margin |
9 | Disruptive innovation in the Industry |
10 | Technology trends in the Industry |
11 | Consumer trends in the industry |
12 | Recent Production Milestones |
13 | Component Manufacturing in US, EU and China |
14 | COVID-19 impact on overall market |
15 | COVID-19 impact on Production of components |
16 | COVID-19 impact on Point of sale |
17 | Market Segmentation, Dynamics and Forecast by Geography, 2023-2030 |
18 | Market Segmentation, Dynamics and Forecast by Product Type, 2023-2030 |
19 | Market Segmentation, Dynamics and Forecast by Application, 2023-2030 |
20 | Market Segmentation, Dynamics and Forecast by End use, 2023-2030 |
21 | Product installation rate by OEM, 2023 |
22 | Incline/Decline in Average B-2-B selling price in past 5 years |
23 | Competition from substitute products |
24 | Gross margin and average profitability of suppliers |
25 | New product development in past 12 months |
26 | M&A in past 12 months |
27 | Growth strategy of leading players |
28 | Market share of vendors, 2023 |
29 | Company Profiles |
30 | Unmet needs and opportunity for new suppliers |
31 | Conclusion |
32 | Appendix |