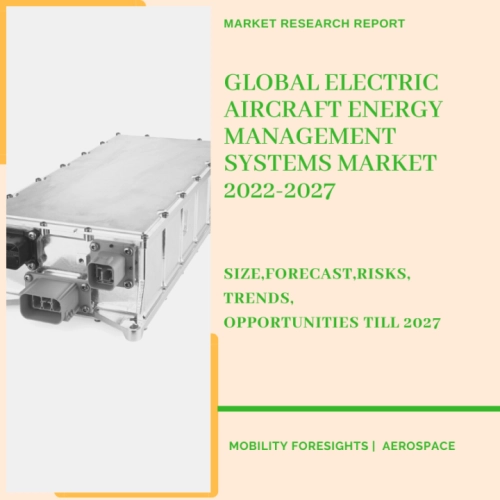
- Get in Touch with Us
Last Updated: Apr 25, 2025 | Study Period: 2022-2027
The typical electrical power distribution topologies used in modern aircraft are made up of switches, bus bars, feeders, converters, generators, and other similar devices. Generators cannot be paralleled because MEA frequently shifts between 3-phase constant frequency networks to wild frequency networks.
The simultaneity effect is reduced because of this lack of parallelism because many independent power distribution networks are required. Consequently, a typical power management function must make sure that the power generated at any given time equals the power used.
Power optimization is used in the more electric design to increase overall performance while using less power. By doing away with hydraulic storage, the switch from hydraulic towards electric power makes the aircraft lighter. Fuel economy is improved when the weight of the aircraft is decreased overall.
About 11% of hydraulically controlled systems on modern aircraft are being replaced with electric systems in an effort to increase economy. As a result, one of the main development drivers for the aviation electrical systems market is the improvement of aircraft performance. It costs a lot of money to install a fully automated, cutting-edge EMS system in a building or industry.
Every industry seeks to reduce its consumption costs. As a result, they need energy management systems to keep track of how much energy various factories and devices are using.
Component makers have many chances thanks to the most recent developments in electric and electronic aviation technology. At several stages of the value chain, aircraft manufacturers are investigating novel methods of power generation and distribution.
Future aeroplanes will likely use a variety of technologies, including distributed architectures, power electronics (in the starter/generation system of the main engines), and complex embedded digital systems.
BAE is a leading mobiliser of the equipment in the market. The latest integration has been for the Regional/business jets, as well as urban air mobility systems, use hybrid and fully electric aircraft's energy management and engine control technologies.
This latest discovery enables us to improve our tried-and-true energy management and control technologies and, in the future, work on hybrid electric demos.
It enters the market for energy management for hybrid and all-electric aircraft by fusing our flight and engine controls expertise with our power management expertise from ground-based hybrid buses.
Solar Eagle Project is part of the component manufacture trending companies in the current industry. The complementing advantage principle was used in the development of the HAPS hybrid energy system.
For HAPS, it comprises of fuel cells as the main electric power source (the energy production components), a battery system, and/or super capacitors as the backup power source (the energy storage components).
A more complex hybrid system results from the three power sources' dynamic properties. Therefore, it is crucial to offer effective power management. Management techniques allocate electricity among various sources.
Sl no | Topic |
1 | Market Segmentation |
2 | Scope of the report |
3 | Abbreviations |
4 | Research Methodology |
5 | Executive Summary |
6 | Introduction |
7 | Insights from Industry stakeholders |
8 | Cost breakdown of Product by sub-components and average profit margin |
9 | Disruptive innovation in the Industry |
10 | Technology trends in the Industry |
11 | Consumer trends in the industry |
12 | Recent Production Milestones |
13 | Component Manufacturing in US, EU and China |
14 | COVID-19 impact on overall market |
15 | COVID-19 impact on Production of components |
16 | COVID-19 impact on Point of sale |
17 | Market Segmentation, Dynamics and Forecast by Geography, 2022-2027 |
18 | Market Segmentation, Dynamics and Forecast by Product Type, 2022-2027 |
19 | Market Segmentation, Dynamics and Forecast by Application, 2022-2027 |
20 | Market Segmentation, Dynamics and Forecast by End use, 2022-2027 |
21 | Product installation rate by OEM, 2022 |
22 | Incline/Decline in Average B-2-B selling price in past 5 years |
23 | Competition from substitute products |
24 | Gross margin and average profitability of suppliers |
25 | New product development in past 12 months |
26 | M&A in past 12 months |
27 | Growth strategy of leading players |
28 | Market share of vendors, 2022 |
29 | Company Profiles |
30 | Unmet needs and opportunity for new suppliers |
31 | Conclusion |
32 | Appendix |