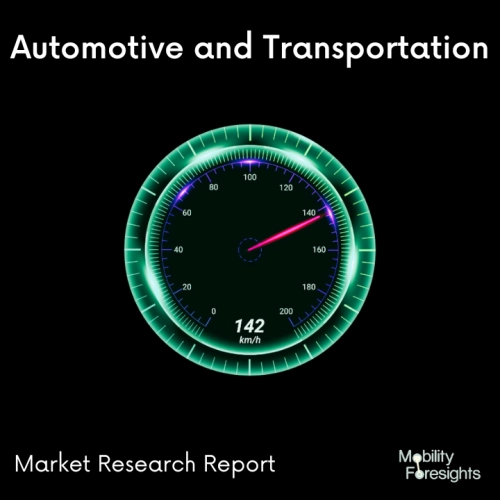
- Get in Touch with Us
Last Updated: Apr 25, 2025 | Study Period: 2024-2030
Specialty chemicals, often part of performance chemicals, have been used to enhance manufacturing technology and as constituents in final goods. Because specialty chemical development is dependent on combining technical as well as operational features, knowing the chemical properties and characteristics, and therefore how they provide advantage to the specific applications, is critical.
Any significant effect on health or the environment must also be evaluated and handled. Their manufacture necessitates complicated techniques as well as substantial research and development.
Typical specialty chemical products are additives that are applied to other goods in tiny quantities to enhance their qualities. Food additives, fire retardants, even lighting stabilizers are a few examples.
Due to various patents, specialized chemicals are frequently confined to individual producers; but, when those patents expire and market demand develops, specialty compounds can also become commodities compounds. Specialty chemical products play a significant part in improving the appearance and feel of your car.
Motor oil, for example, takes heat off from such an engine's combustion process and allows its mechanical components to function successfully.
Elastomeric black, but at the other extreme, are employed as a productivity component in tyres, whereas the architecture of a car necessitates the employment of many structural adhesives and high-performance composite materials. These are found in gasoline additives, coatings, refrigerants, noise-cancelling insulators, airbags, battery packs, tyres, and a variety of other items.
Polymers are always an important component of engine oils and transmission fluids, allowing today's high-performance motors to operate over a wide range of temperature while maximizing performance and decreasing formulation expenses.
Several Asian Pacific nations are likewise focused on investments in specialized compounds. Asia Pacific is also becoming a significant market for vehicle lubricants. Extended vehicle operating lives, higher vehicle manufacturing, and more customer perception have all contributed to a rise in demand for automotive coolants.
Chemicals are even being employed to improve the production process for automobiles. For example, original equipment manufacturers (OEMs) are transitioning numerous stamping as well as soldered steel critical elements to less mass dyed casting aluminum elements.
Chemical businesses will play a significant role in the whole mobility production chain, forcing manufacturing to reconsider existing supply models. For instance, rechargeable batteries construction will necessitate the acquisition of critical minerals like lithium, copper, and specialty polymers.
By broadening Chemical businesses may benefit on the possibility to be a part of these new value streams by tailoring their services to satisfy such market requirements.
Ultimately, whenever full independence is achieved, autonomous technology will have an impact on chemistry, forcing altogether new vehicle designs without drivers' seating, steering wheels, as well as other components typical in ordinary automobiles.
In the long run, a totally autonomous and accident-free society may even allow for automobiles constructed entirely of plastic, however safety standards and criteria are doubtful to be loosened in the near future.
Shifting legislation and advancements in rechargeable batteries may herald a new phase of growth for electric vehicles, implying a drastically simpler engine requiring less fluids as well as other compounds.
Although much remains unknown, autonomous vehicles might be commercially available, as well as the innovation could eventually enable reinvented vehicle interiors and new body materials for cars that seldom crash.
Neogene has recently begun producing electrolytes for lithium-ion batteries, utilizing its decades of lithium salts knowledge.
Gujarat Fluorochemicals, a producer of fluoropolymers, fluor-specialties, and bulk chemicals, is branching out into new areas such battery chemicals for electric vehicles, solar panels, and hydrogen fuel cells.
The demand for polyvinylidene fluoride is fast increasing, according to the company's management, due to its use as a cathode binder in electric vehicle batteries.
Glencore and General Motors Co. recently signed a multi-year sourcing arrangement under which Glencore will provide cobalt to GM from its Murrin Murrin plant in Australia.
The cobalt processed in Australia will be used in GM's Ultrium battery cathodes, which will power electric vehicles such as the Chevrolet Silverado EV, GMC HUMMER EV, and Cadillac LYRIQ.
Cobalt is an important metal in the production of EV batteries, and the cobalt processed in Australia will be used in GM's Ultrium battery cathodes, which will power electric vehicles such as the Chevrolet Silverado EV, GMC
BHP Group's capacity to diversify beyond bulk mining will be put to the test in the coming year with a move into specialized chemicals for the battery industry by its once-struggling Nickel West division.
In the second quarter of next year, the global miner expects to begin producing nickel sulphate, a higher-value, higher-purity product for sale to customers along the electric vehicle (EV) supply chain.
Nickel West, which consists of mines, a smelter, and a refinery that produces nickel as powder or briquettes, is constructing the world's largest nickel sulphate facility, according to BHP, to supply material for lithium-ion batteries.
BHP has evolved from a high-volume, low-cost producer of bulk commodities to a high-quality chemical manufacturer in demand by the battery industry.
The Global Electric Vehicle Specialty Chemicals Market can be segmented into following categories for further analysis.
Communication has little structural consequences, with the exception of enhanced car panels as well as detectors that utilize materials such as LED screens, smart glass, liquid-crystal polymers, and other technologies used for 5G network accessibility.
As connection improves the usefulness of technologies in automobiles, chemical manufacturers in the electronics sector may benefit. Shared mobility, which is presently based on standard automobiles, will rapidly migrate to purpose-built vehicles and, subsequently, autonomous vehicles.
Versatile architecture is used in purpose-built EV based vehicles to provide transportation alternatives adapted to particular preferences or demands, and this versatility may motivate the redesigning of the EV interior.
Virgin polymers have a greater carbon footprint than steel, ranging from 2.5 to 4.5 tonnes every tonne of polymer manufactured. High efficiency savings can easily outweigh the process emissions of polymer manufacture in the case of traditional electric and hybrid cars.
A considerable gain in fuel economy balances the process emissions of the polymers used in an electrified or hybrid-powered car. Almost every aspect of a contemporary automobile is made of synthetic components, including the leather seats.
Airbags may be hidden below molded instrument cluster coverings, composite foam sitting can provide convenience, and touchscreens have essentially replaced mechanical dials and gauges.
Compounded natural rubber, EPDM and other synthetic elastomers, mineral oil lubricants, synthetic lubricants such as polyalphaolefins, polyamide electrical connections, polyolefin ducting among fuel tanks, and so many more are examples of particular goods from the C&SM industry.
To attain this lofty goal, foreign corporations must strengthen and grow their top management teams in India. Local management teams need to strategize on how to enter the market, which cannot be done from regional headquarters in China or Singapore, let alone company headquarters in Europe, the United States, or Japan.
Continuous R&D in this industry has aided in the production of items with superior and cutting-edge characteristics. This is one of the primary drivers driving the market's expansion. With rising industrialization, substantial consumption has emerged from Asian nations such as India and China.
Evonik is a leading developer of the specialty chemical manufacturing focusing on the electric vehicles manufacturing. VESTANAT is a non-yellowing crosslinker for thermosetting at 2K or 1K. PUR coverings enhance performance in a variety of applications and services, including extremely chemical-resistant 2K and 1K mechanisms.
High Tg and rapid drying coverings, PCM adaptability, solvent-borne, water-borne, solvent-free (e.g. powder coating systems), as well as many other benefits. IPDI is distinguished by its exceptional compliance with any type of coating resin and its low addition polymerization stiffness.
H12MDI has a high chemical resistance and outstanding mechanical qualities for PUD and TPU purposes. TMDI also demonstrates outstanding compliance and impressive performance in UV resin flexibilization. This is indeed a novel class of urethane-alkoxysilane binders and cross linkers that give outstanding abrasion resistance, particularly in automobile OEM and maintenance coatings.
This innovative technology serves as a flexible foundation for high-performance isocyanate-free (NISO) technology that may be employed in both ambient-temperature drying as well as thermosetting solutions.
BASF Chemicals is also a leading developer of the specialty chemicals focused on various parts and elements of the Electric Vehicles. It has produced the Elastosis Material of series production which is focused on better flow and sectional integrity of the Electric Vehicle bodies considering their light weight requirements.
Elastosis's production process comprises Elastosis R, Elastosis D, and Elastosis K (rigorous integrated foam) With something like a wide range of qualities, these polyurethane solutions are high-quality, cost-effective alternative to conventional materials like metals, thermosetting compounds, and engineered thermoplastics.
Elastolit K is a micro-cellular nearly solid substance with good processability. Large-format pieces with lengthy flow paths and wall thicknesses of 3 to 6 mm may be manufactured with relatively high ultimate tensile strength. Because of the viscos-plastic characteristics of Elastosis K, component shapes are easily manufactured.
Molded pieces can sometimes be supplied with snap-in connections. Because low-cost aluminum molds may be used while process durations are fast, this technology is indeed appealing for medium-sized batches.
Sl no | Topic |
1 | Market Segmentation |
2 | Scope of the report |
3 | Abbreviations |
4 | Research Methodology |
5 | Executive Summary |
6 | Introduction |
7 | Insights from Industry stakeholders |
8 | Cost breakdown of Product by sub-components and average profit margin |
9 | Disruptive innovation in the Industry |
10 | Technology trends in the Industry |
11 | Consumer trends in the industry |
12 | Recent Production Milestones |
13 | Component Manufacturing in US, EU and China |
14 | COVID-19 impact on overall market |
15 | COVID-19 impact on Production of components |
16 | COVID-19 impact on Point of sale |
17 | Market Segmentation, Dynamics and Forecast by Geography, 2024-2030 |
18 | Market Segmentation, Dynamics and Forecast by Product Type, 2024-2030 |
19 | Market Segmentation, Dynamics and Forecast by Application, 2024-2030 |
20 | Market Segmentation, Dynamics and Forecast by End use, 2024-2030 |
21 | Product installation rate by OEM, 2023 |
22 | Incline/Decline in Average B-2-B selling price in past 5 years |
23 | Competition from substitute products |
24 | Gross margin and average profitability of suppliers |
25 | New product development in past 12 months |
26 | M&A in past 12 months |
27 | Growth strategy of leading players |
28 | Market share of vendors, 2023 |
29 | Company Profiles |
30 | Unmet needs and opportunity for new suppliers |
31 | Conclusion |
32 | Appendix |