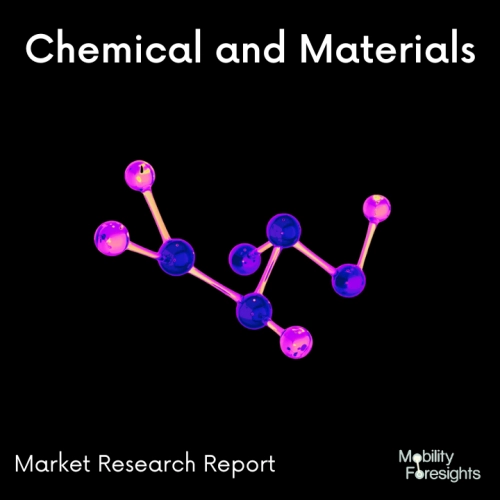
- Get in Touch with Us
Last Updated: Apr 25, 2025 | Study Period: 2024-2030
Electroless nickel plating is a process of applying a nickel-phosphorus alloy to the surface of a metal object in order to provide a corrosion-resistant coating. This plating method is known for its uniformity, as it does not require an electrical current to plate the surface.
Instead, the nickel-phosphorus plating is applied to the object through a chemical reaction, which is triggered when the object is immersed in the plating solution.
The nickel-phosphorus alloy is composed of about 10-15% phosphorus and the rest is nickel. This combination of metals gives the electroless nickel plating a slightly higher wear and corrosion resistance than standard nickel plating. It also has higher hardness and superior lubricity, which makes it useful for applications in hostile and high wear environments.
The plating process begins by preparing the surface of the object to be plated. This typically involves cleaning the surface to remove any contaminants, then activating the surface so that the plating solution can bond to it. Once the surface is ready, the object is submerged in the plating solution and the chemical reaction begins.
The plating process continues until the desired thickness is achieved. The nickel-phosphorus alloy is then hardened through a post-plating heat treatment that can be done in a furnace, oven, or other controlled environment.
The electroless nickel plating process is used in a wide range of industries, from automotive to aerospace, and is also popular for applications where uniform coating and corrosion resistance is needed. It is also relatively easy to use and cost-effective, making it a popular choice for many manufacturers.
The Global Electroless Nickel Plating Market accounted for $XX Billion in 2023 and is anticipated to reach $XX Billion by 2030, registering a CAGR of XX% from 2024 to 2030.
Electroless nickel plating is a process used to deposit a nickel-phosphorus alloy layer onto the surface of a substrate material. This process is performed in an autocatalytic chemical reaction and does not require electricity. The resulting electroless nickel plating provides a uniform coating of nickel alloy on the surface of the substrate.
This coating increases the surface hardness of the substrate and provides excellent corrosion resistance, electrical conductivity, and wear resistance.
The electroless nickel plating process can be used on a variety of substrates including aluminum, brass, carbon steel, and stainless steel. The thickness of the electroless nickel coating can be easily controlled, making it an ideal choice for high-precision engineering applications. The coating is also resistant to solderability, making it suitable for use in electrical and electronic components.
In recent years, the demand for electroless nickel plating has grown significantly due to its superior performance and the increasing need for corrosion protection. This has led to new product launches from several companies, including those specializing in electroless nickel plating services.
These companies offer a range of services and products, including electroless nickel plating solutions for automotive, aerospace, medical, and industrial applications.
The benefits of electroless nickel plating are numerous, including improved wear and corrosion resistance, improved electrical conductivity, and improved solderability.
The process is also cost-effective and versatile, making it a preferred choice for many industries. As such, electroless nickel plating is becoming increasingly popular for a variety of applications, and new product launches continue to appear on the market.
Sl no | Topic |
1 | Market Segmentation |
2 | Scope of the report |
3 | Abbreviations |
4 | Research Methodology |
5 | Executive Summary |
6 | Introdauction |
7 | Insights from Industry stakeholders |
8 | Cost breakdown of Product by sub-components and average profit margin |
9 | Disruptive innovation in theIndustry |
10 | Technology trends in the Industry |
11 | Consumer trends in the industry |
12 | Recent Production Milestones |
13 | Component Manufacturing in US, EU and China |
14 | COVID-19 impact on overall market |
15 | COVID-19 impact on Production of components |
16 | COVID-19 impact on Point of sale |
17 | Market Segmentation, Dynamics and Forecast by Geography, 2024-2030 |
18 | Market Segmentation, Dynamics and Forecast by Product Type, 2024-2030 |
19 | Market Segmentation, Dynamics and Forecast by Application, 2024-2030 |
20 | Market Segmentation, Dynamics and Forecast by End use, 2024-2030 |
21 | Product installation rate by OEM, 2023 |
22 | Incline/Decline in Average B-2-B selling price in past 5 years |
23 | Competition from substitute products |
24 | Gross margin and average profitability of suppliers |
25 | New product development in past 12 months |
26 | M&A in past 12 months |
27 | Growth strategy of leading players |
28 | Market share of vendors, 2023 |
29 | Company Profiles |
30 | Unmet needs and opportunity for new suppliers |
31 | Conclusion |
32 | Appendix |