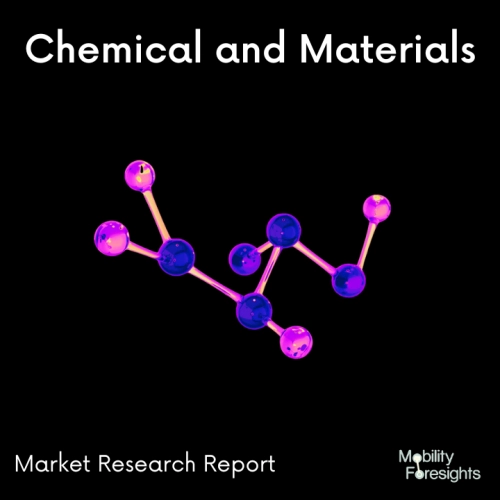
- Get in Touch with Us
Last Updated: Apr 25, 2025 | Study Period: 2024-2030
Electrical components are shielded from the outside world through a method called electronic encapsulation. This can be accomplished using substances like silicone, epoxy, or potting compound.
Electronic encapsulation includes coating an electronic assembly with a substance to protect it against corrosion, stress, and vibration. Encapsulation protects your electronic assemblies against various severe environments and tin whiskers since it is thicker and more durable than conformal coating.
Maintaining them at their peak working levels over extended periods of time is beneficial. Electronic and electrical components that are encapsulated are also protected from tampering, reverse engineering, and other security risks. Encapsulation's goal is to surround the component with protection without really embedding it.
It enhances electrical insulation, flame retardancy, and heat dissipation while providing resistance to significant threats like shock, vibration, moisture, and corrosive chemicals.
The Global Electronic Encapsulation market accounted for $XX Billion in 2023 and is anticipated to reach $XX Billion by 2030, registering a CAGR of XX% from 2024 to 2030.
First Encapsulated Surface Mount Fuse from Little fuse Is Designed for Intrinsic Safety Protection The first encapsulated surface mount fuse has been unveiled by Little fuse, Inc., the industry pioneer in circuit protection, in accordance with the UL 913 Standard.
It is intended to provide inherent safety protection for equipment used in or near hazardous places and explosive atmospheres.
The PICO® 304 Series surface mount fuse's 1mm-thick encapsulation around the body reduces the amount of heat produced during overcurrent and short circuit fault conditions and contains any sparks or arcs inside the fuse assembly, preventing them from being exposed to potentially explosive gases or dust outside.
This encapsulation eliminates the requirement to pot or coat printed circuit boards or assemblies, saving time and resources and lowering the cost of the finished product.
For example, measuring or processing electronic and electrical equipment, motor controllers, communication handsets/two-way radios and related battery chargers, process control and automation equipment, sensors, lighting, and flow/gas meters are typical applications for the PICO® 304 Series in the oil, gas, mining, chemical, pharmaceutical, food and beverage, and other process industries.
Sparks are not exposed to potentially explosive gases or particles in the environment thanks to encapsulated and sealed design, which satisfies safety regulations for hazardous settings. Circuit boards can be manufactured for less money overall by not needing to be coated or potted.
Sl no | Topic |
1 | Market Segmentation |
2 | Scope of the report |
3 | Abbreviations |
4 | Research Methodology |
5 | Executive Summary |
6 | Introduction |
7 | Insights from Industry stakeholders |
8 | Cost breakdown of Product by sub-components and average profit margin |
9 | Disruptive innovation in the Industry |
10 | Technology trends in the Industry |
11 | Consumer trends in the industry |
12 | Recent Production Milestones |
13 | Component Manufacturing in US, EU and China |
14 | COVID-19 impact on overall market |
15 | COVID-19 impact on Production of components |
16 | COVID-19 impact on Point of sale |
17 | Market Segmentation, Dynamics and Forecast by Geography, 2024-2030 |
18 | Market Segmentation, Dynamics and Forecast by Product Type, 2024-2030 |
19 | Market Segmentation, Dynamics and Forecast by Application, 2024-2030 |
20 | Market Segmentation, Dynamics and Forecast by End use, 2024-2030 |
21 | Product installation rate by OEM, 2023 |
22 | Incline/Decline in Average B-2-B selling price in past 5 years |
23 | Competition from substitute products |
24 | Gross margin and average profitability of suppliers |
25 | New product development in past 12 months |
26 | M&A in past 12 months |
27 | Growth strategy of leading players |
28 | Market share of vendors, 2023 |
29 | Company Profiles |
30 | Unmet needs and opportunity for new suppliers |
31 | Conclusion |
32 | Appendix |