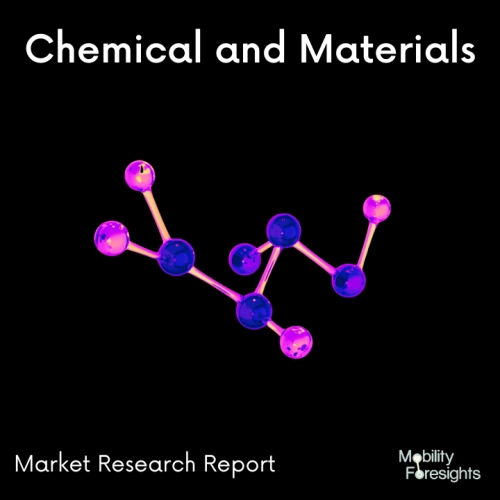
- Get in Touch with Us
Last Updated: Apr 25, 2025 | Study Period: 2024-2030
High-performance foam provides a range of advantages in the electronics industry, from insulation to shock absorption. It can be used in a vast range of applications, including soundproofing, subwoofer cabinet filling, OEMs, switchgear, and even supporting IT networks.
High-performance foam can help keep sensitive electronics safe from electrical short-circuits and mechanical shock. Through its insulation properties, high-performance foam can provide improved protection from dust, water, and other elements.
Its elastic nature increases sound and vibration dampening, while its lightweight nature reduces the overall weight of the application. The low thermal conductivity of the foam ensures the operation of electronic components without the risk of excessive heating.
High-performance foam can reduce noise pollution by blocking sound transmission. It can be used effectively in enclosures for acoustic solutions, loudspeakers, cabinets, and even in the interiors of commercial vehicles.
With its superior abrasive, electrical, and thermal insulation capabilities, high-performance foam is ideal for the challenging environments of the electronics industry, including extreme temperatures and pressure changes.
Due to its excellent resiliency, high-performance foam can withstand mechanical shocks without absorbing energy, which reduces the chances of damage to interior components.
The material can also perform effectively in humid environments, where standard materials can quickly become saturated and fail. It is also inherently difficult to ignite, making it safer for electrical applications.
The Global electronics high performance foam market accounted for $XX Billion in 2023 and is anticipated to reach $XX Billion by 2030, registering a CAGR of XX% from 2024 to 2030.
CHT introduced silicone foam for EV battery packs and Electronics. In addition to mitigating thermal runaway and protecting electronic components and EV battery packs from moisture, debris, vibration, and shock, CHT's Silos' Lite 21025 satisfies weight reduction requirements. When low smoke, flame, and toxicity are required, this silicone foam is also perfect.
CHT is creating novel lightweight silicone materials with great performance, which will spur innovation in a variety of sectors and applications. These materials are created with sustainability as a primary design consideration and are engineered to fulfil demanding performance standards.
The Sil So Lite 21025 is a liquid system that can be easily dispensed using an automated mixing machine or cartridge because of its low viscosity and 1:1 mix ratio. The primer less adherence of this silicone foam to a range of substrates and its quick gel time will assist boost production throughput.
Moreover, employing one of the primers suggested by CHT can result in increased adhesion. Regarding safety, Sil So Lite 21025 has outstanding flame retardancy, reducing the risk of a thermal runaway incident. To confirm that Sil so Lite 21025 satisfies the UL 94 V-0 classification, independent testing is now being conducted.
With the introduction of its new Power Store Aerogel Capacitor, Cooper Electronic Technologies has introduced a ground-breaking carbon aerogel foam technology. These ultra-high capacitance devices, also known as Electrochemical Double-Layer Capacitors (EDLC), feature ultra-low current leakage and exceptionally low Electric Series Resistance (ESR) values. Their volumetric capacitance is 2,000 times that of typical aluminum electrolytic capacitors.
An apparatus for storing energy is the aerogel capacitor. In the electrochemical double-layer that forms on the carbon surface, charge is electrostatically stored. Its ability to release charge quickly enough to provide specific power of up to 4,000 W/Kgâten times the power of "high power" batteries like Li-ion batteriesâmakes it a pulse power device as well.
Sl no | Topic |
1 | Market Segmentation |
2 | Scope of the report |
3 | Abbreviations |
4 | Research Methodology |
5 | Executive Summary |
6 | Introduction |
7 | Insights from Industry stakeholders |
8 | Cost breakdown of Product by sub-components and average profit margin |
9 | Disruptive innovation in the Industry |
10 | Technology trends in the Industry |
11 | Consumer trends in the industry |
12 | Recent Production Milestones |
13 | Component Manufacturing in US, EU and China |
14 | COVID-19 impact on overall market |
15 | COVID-19 impact on Production of components |
16 | COVID-19 impact on Point of sale |
17 | Market Segmentation, Dynamics and Forecast by Geography, 2024-2030 |
18 | Market Segmentation, Dynamics and Forecast by Product Type, 2024-2030 |
19 | Market Segmentation, Dynamics and Forecast by Application, 2024-2030 |
20 | Market Segmentation, Dynamics and Forecast by End use, 2024-2030 |
21 | Product installation rate by OEM, 2023 |
22 | Incline/Decline in Average B-2-B selling price in past 5 years |
23 | Competition from substitute products |
24 | Gross margin and average profitability of suppliers |
25 | New product development in past 12 months |
26 | M&A in past 12 months |
27 | Growth strategy of leading players |
28 | Market share of vendors, 2023 |
29 | Company Profiles |
30 | Unmet needs and opportunity for new suppliers |
31 | Conclusion |
32 | Appendix |