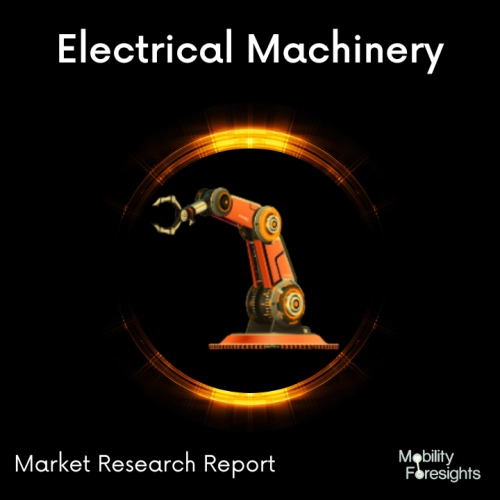
- Get in Touch with Us
Last Updated: Apr 25, 2025 | Study Period: 2024-2030
Utilised in the generation and damping of resistive forces are electrorheological fluids, which are completely reliant on the applied electric fields. Active vibration reduction and motion control are a couple of examples of uses.
Electrorheological (ER) materials have rheological characteristics, flow, and deformation behaviour that strongly depend on the strength of the electric field applied to them. As a material for creating intelligent machines and structures, electro-rheological (ER) fluids are today recognised as one of the most adaptable.
ER fluids, in theory, offer a sophisticated method of supplying continuously varying forces for the management of mechanical vibrations.
The Global Electrorheological fluid actuator market accounted for $XX Billion in 2023 and is anticipated to reach $XX Billion by 2030, registering a CAGR of XX% from 2024 to 2030.
actuator with electro-rheological fluid damping A moving element, such as a piston and rod assembly, is contained within the actuator housing of an electro-rheological fluid damped actuator. The actuator also has a hydraulic circuit that is filled with an electro-rheological fluid.
The moveable element is dampened actively and variably by the hydraulic circuit and rheological fluid. The output of an electrical circuit, which generates an electric field inside the hydraulic circuit, regulates the damping force.
The viscosity of the electro-rheological fluid exposed to the electric field will change in proportion to the strength of the electric field, depending on how much of it is there.
The current invention relates to the field of hydraulic dampers for actuator mechanisms, more particularly to a hydraulic damper with electro-rheological fluid that can alter the dampening level for the actuator mechanism.
It is frequently necessary for airframe reactions to command controls to be quick, precise, and long-lasting due to the high rates of speed and shortened flight periods of different missile systems.
Aerofin and thrust vector control are commonly handled by pneumatic, hydraulic, or electro-mechanical actuators in missile systems.
Furthermore, a hydraulic control valve that is positioned in the hydraulic circuit is used in the preferred form of the current invention.
The hydraulic circuit has a point of restriction thanks to the electro-rheological fluid valve. The output of the electric circuit generates an electric field near this electro-rheological fluid valve, which causes the viscosity of the electro-rheological fluid in the valve to change in proportion to the strength of the electric field.
Sl no | Topic |
1 | Market Segmentation |
2 | Scope of the report |
3 | Abbreviations |
4 | Research Methodology |
5 | Executive Summary |
6 | Introduction |
7 | Insights from Industry stakeholders |
8 | Cost breakdown of Product by sub-components and average profit margin |
9 | Disruptive innovation in the Industry |
10 | Technology trends in the Industry |
11 | Consumer trends in the industry |
12 | Recent Production Milestones |
13 | Component Manufacturing in US, EU and China |
14 | COVID-19 impact on overall market |
15 | COVID-19 impact on Production of components |
16 | COVID-19 impact on Point of sale |
17 | Market Segmentation, Dynamics and Forecast by Geography, 2024-2030 |
18 | Market Segmentation, Dynamics and Forecast by Product Type, 2024-2030 |
19 | Market Segmentation, Dynamics and Forecast by Application, 2024-2030 |
20 | Market Segmentation, Dynamics and Forecast by End use, 2024-2030 |
21 | Product installation rate by OEM, 2023 |
22 | Incline/Decline in Average B-2-B selling price in past 5 years |
23 | Competition from substitute products |
24 | Gross margin and average profitability of suppliers |
25 | New product development in past 12 months |
26 | M&A in past 12 months |
27 | Growth strategy of leading players |
28 | Market share of vendors, 2023 |
29 | Company Profiles |
30 | Unmet needs and opportunity for new suppliers |
31 | Conclusion |
32 | Appendix |