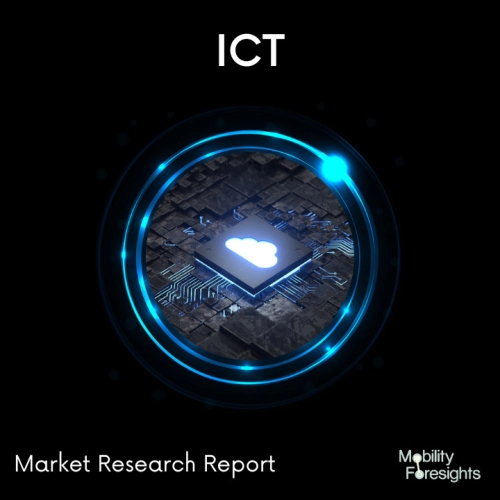
- Get in Touch with Us
Last Updated: Apr 25, 2025 | Study Period: 2024-2030
A passive sensor based on the electrostatic induction concept is an electrostatic sensor. The sensor is employed in the electrostatic monitoring system to identify changes in the electrostatic field in the sensing zone that are brought on by the influence of adjacent charges.
An electric field is created around an electrified object that is inversely correlated to the charge. The strength of this electric field is measured by electrostatic sensors, who convert it to electric potential.
A capacitor is connected in series with the input of the charge sensor, which is a very high impedance voltage sensor. Until the source voltage is attained, or when equilibrium is established, the capacitor will continue to charge up.
Electroscope. A gadget called an electroscope uses thin metal or plastic leaves that split when charged to detect static electricity. A suspected static electric charge-containing object is brought close to the electroscope's metal plate or ball.
The capacitance is set at a distance of 100 mm from the measuring point using the formula Q (charge) = C m (capacitance) x V (voltage). As a result, the charge Q fluctuates in direct proportion to the voltage V.
Fraser metres are easy to use and excellent for problem analysis. In the actual world, static electricity has a variety of applications. Static electric charges are mostly used in printers and photocopiers to draw ink or toner to the paper. Air filters and paint sprayers are further uses.
The Global Electrostatic sensor market accounted for $XX Billion in 2023 and is anticipated to reach $XX Billion by 2030, registering a CAGR of XX% from 2024 to 2030.
Nokomis Incâs electrostatic sensor is a type of sensor that determines whether an object or material is present or absent using the electrostatics principles. The sensor can detect voltage changes brought on by the presence of an object or substance. Numerous applications for this kind of sensor exist, such as security, medical diagnostics, and industrial inspection and quality control.
The electronics sector is aware of the issue of ESD. Electronics are becoming more susceptible to ESD as their parts and devices get smaller and smaller. Electronics that are prone to breakage during production, shipping, or storage can result in significant financial losses.
Factory floor employees can wear specialised apparel composed of ESD-proof materials or components wrapped in ESD-compatible packaging to prevent damage.
Plastics that are electrically conductive are a very adaptable solution for such settings. They can be utilised in a variety of products, including fibres, films, filaments, sheets, tubes, hoses, profiles, and more. Plastic packaging and parts can be extruded or moulded into stiff or flexible shapes using a variety of polymers.
Applications made of conductive plastic are less expensive, lighter, corrosion-free, and simpler to make than those made of other materials.
Sl no | Topic |
1 | Market Segmentation |
2 | Scope of the report |
3 | Abbreviations |
4 | Research Methodology |
5 | Executive Summary |
6 | Introduction |
7 | Insights from Industry stakeholders |
8 | Cost breakdown of Product by sub-components and average profit margin |
9 | Disruptive innovation in the Industry |
10 | Technology trends in the Industry |
11 | Consumer trends in the industry |
12 | Recent Production Milestones |
13 | Component Manufacturing in US, EU and China |
14 | COVID-19 impact on overall market |
15 | COVID-19 impact on Production of components |
16 | COVID-19 impact on Point of sale |
17 | Market Segmentation, Dynamics and Forecast by Geography, 2024-2030 |
18 | Market Segmentation, Dynamics and Forecast by Product Type, 2024-2030 |
19 | Market Segmentation, Dynamics and Forecast by Application, 2024-2030 |
20 | Market Segmentation, Dynamics and Forecast by End use, 2024-2030 |
21 | Product installation rate by OEM, 2023 |
22 | Incline/Decline in Average B-2-B selling price in past 5 years |
23 | Competition from substitute products |
24 | Gross margin and average profitability of suppliers |
25 | New product development in past 12 months |
26 | M&A in past 12 months |
27 | Growth strategy of leading players |
28 | Market share of vendors, 2023 |
29 | Company Profiles |
30 | Unmet needs and opportunity for new suppliers |
31 | Conclusion |
32 | Appendix |