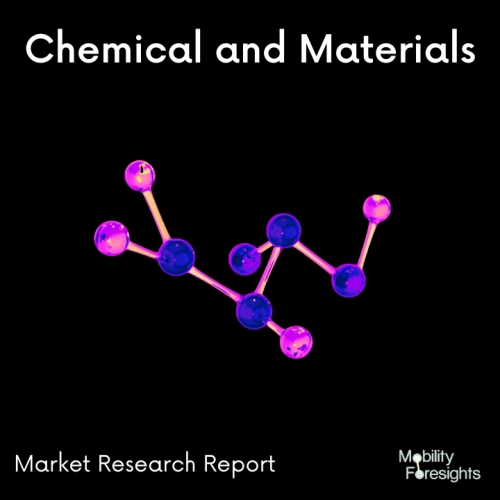
- Get in Touch with Us
Last Updated: Apr 25, 2025 | Study Period: 2024-2030
A thick iron tank coated with a high degree of enamel is used to create enamel reactors. This high degree of enamel coating is then firmly bonded to the surface of the metal iron by a specific chemical corrosion enamel to build a smooth and clean lining layer, giving both materials equal opportunity.
Enamel reaction kettles are manufactured by spraying a glaze with a high silicon concentration over the surface of metal tyres after roasting them at a high temperature for 900 Shan, resulting in a rich porcelain glaze that has the advantages of both strong metal and glass.
In place of stainless steel and non-ferrous metal equipment, enamel reactors are frequently used in the chemical, pharmaceutical, dyestuff, pesticide, organic synthesis, petroleum, food manufacturing, and defense industries as well as other industrial production and scientific research in the reaction, evaporation, concentration, synthesis, polymerization, saponification, sulfonation, chlorination, nitrification, etc.
The enamel/enameled glass reaction kettle (reaction tank) is a piece of chemical machinery that enamels high silicon dioxide glass enamels that are coated on the inside of steel containers and then evenly attached to the metal surface by burning at high temperatures.
The enamel reaction kettle is an outstanding piece of corrosion-resistant chemical equipment because it offers the combined benefits of glass stability and metal strength.
The Global enamel reactor market accounted for $XX Billion in 2023 and is anticipated to reach $XX Billion by 2030, registering a CAGR of XX% from 2024 to 2030.
Enamel glass-lined reactors are available from De Dietrich Process Systems to accommodate a wide range of chemical processes, volume needs from laboratory scale and pilot plant sizes to very large production units, and local design and international code requirements.
Design information, vessel dimensions in general, and nozzle placement are all standardized. with the benefits of Greater internal pressure rating is made possible by the top head strength.
Agitation-allowing openings are also minimized, increasing security by lowering cramps and gaskets. In comparison to the CE reactor, the vessel's height is reduced for the same usable capacity due to the simpler geometry that makes it easier to reach apertures designated for the operations.
Sl no | Topic |
1 | Market Segmentation |
2 | Scope of the report |
3 | Abbreviations |
4 | Research Methodology |
5 | Executive Summary |
6 | Introduction |
7 | Insights from Industry stakeholders |
8 | Cost breakdown of Product by sub-components and average profit margin |
9 | Disruptive innovation in the Industry |
10 | Technology trends in the Industry |
11 | Consumer trends in the industry |
12 | Recent Production Milestones |
13 | Component Manufacturing in US, EU and China |
14 | COVID-19 impact on overall market |
15 | COVID-19 impact on Production of components |
16 | COVID-19 impact on Point of sale |
17 | Market Segmentation, Dynamics and Forecast by Geography, 2024-2030 |
18 | Market Segmentation, Dynamics and Forecast by Product Type, 2024-2030 |
19 | Market Segmentation, Dynamics and Forecast by Application, 2024-2030 |
20 | Market Segmentation, Dynamics and Forecast by End use, 2024-2030 |
21 | Product installation rate by OEM, 2023 |
22 | Incline/Decline in Average B-2-B selling price in past 5 years |
23 | Competition from substitute products |
24 | Gross margin and average profitability of suppliers |
25 | New product development in past 12 months |
26 | M&A in past 12 months |
27 | Growth strategy of leading players |
28 | Market share of vendors, 2023 |
29 | Company Profiles |
30 | Unmet needs and opportunity for new suppliers |
31 | Conclusion |
32 | Appendix |