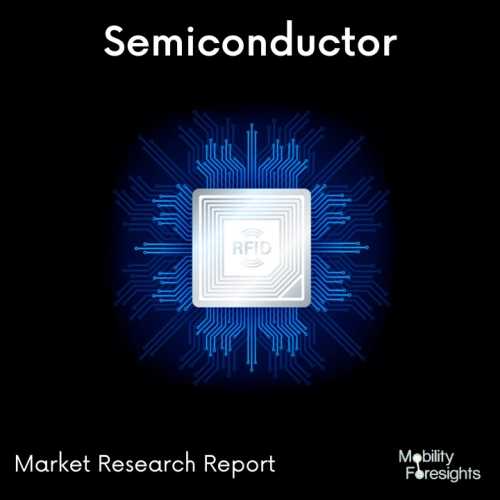
- Get in Touch with Us
Last Updated: Apr 25, 2025 | Study Period: 2022-2030
An energy purification module, and more specifically, an energy purification module with a protective layer formed on a graphite element, is the subject of the present invention.
Ion bombardment is used to implant dopant materials or impurities into a substrate layer in a process called ion implantation.
Implanting a dopant material can change the electrical, optical, or mechanical properties of the original material layer in a semiconductor process.
Conductivity can be altered by implanting a dopant into an existing semiconductor substrate layer, for instance. As a result, the process of doping impurities into an integrated circuit (IC) can enhance the IC's existing properties.
An ion source and a collection of ion beam elements are typical components of an ion implantation system.
An ion beam-producing chamber is also included in the ion source. An extraction electrode assembly and power supply are also included in the ion source, which is attached to the chamber.
For various ionic species and extraction voltages, ion implantation systems can generate ion beams. The guided ion beam line elements can be coated with wafer residues, such as germanium and photoresist compounds, during the ion implantation system's operation.
These residues build up on the aforementioned ion beam line elements and have the potential to detach, contaminating the fabricated wafer with particles.
The Global energy purity module market accounted for $XX Billion in 2021 and is anticipated to reach $XX Billion by 2030, registering a CAGR of XX% from 2022 to 2030.
An insulating bush is inserted into a number of mounting holes made in the housing plate, and both ends of the electrode rods are provided on the corresponding insulating bushings on the left and right sides of the housing plate, which is separated from the left and right sides by a supporting bar .
In the ion beam, the energy purity module assembly acts as an electrical filter to remove ions with a potential that is lower than the desired potential.
An electrode rod made of graphite is provided to fulfill this function. Graphite is a conductor that can withstand high temperatures and apply high voltages.
However, since the graphite electrode rod is not heat-treated after the product has been processed, it contains a lot of impurities.
The impurities that were contained by the impact with the ion beam that had energy are released and act as contaminants in the vacuum chamber, resulting in a decrease in the wafer's quality and the energy purity module assembly's durability.
Additionally, the energy purity module assembly is where the horizontal edge ions of the ion beam are applied when the horizontally equilibrated ion beam is passed through the analyzer.
The electrode rod in the main passage section of the ion beam receives the majority of the ion beam's application. With time, the impurities in the graphite itself and the ion beam that was deposited on the electrode rod's graphite material are separated from the electrode rod and transported to the process chamber together to produce particles.
To put it another way, the electrode rod is separated into a vacuum and serves as a contamination source because the ion beam that is applied to the surface of the thin cylindrical electrode has a small external cross-sectional area.
As a result, the coating film is thickly accumulated despite the equipment's short use time and various conditions, such as a vacuum break or glitch caused by high voltage.
This eventually reduces the energy purity module assembly's durability and necessitates numerous replacements over an extended period of time, thereby extending the equipment's stopping time and preventing process continuity.
In addition, the initial ion beam that passes through the analyzer before being focused in the energy purity module assembly is scattered or defocused before being focused when the equipment is restarted as a result of preventative maintenance or a failure.
Ions are directly deposited on the insulator feedthrough of the electrode rod during the entry process due to the ion beam's weak density and spread at this point.
All in all, the particle shaft is consumed by the protection bushing, which is introduced at the two finishes of the cathode pole and goes about as a feedthrough between the high vacuum and the air while a high voltage is applied.
The glitch is caused by the insulation breaking down as a result of the deposition film and high voltage shakes in the part of the connection where the ion beam is deposited in this manner.
When the glitch occurs, the film quality that was deposited on the electrode rod separates, resulting in a large number of particles and a decrease in the energy purity module assembly's durability.Additionally, equipment failure is common as a result of voltage instability brought on by the mass production of particles.
Sl no | Topic |
1 | Market Segmentation |
2 | Scope of the report |
3 | Abbreviations |
4 | Research Methodology |
5 | Executive Summary |
6 | Introduction |
7 | Insights from Industry stakeholders |
8 | Cost breakdown of Product by sub-components and average profit margin |
9 | Disruptive innovation in the Industry |
10 | Technology trends in the Industry |
11 | Consumer trends in the industry |
12 | Recent Production Milestones |
13 | Component Manufacturing in US, EU and China |
14 | COVID-19 impact on overall market |
15 | COVID-19 impact on Production of components |
16 | COVID-19 impact on Point of sale |
17 | Market Segmentation, Dynamics and Forecast by Geography, 2022-2030 |
18 | Market Segmentation, Dynamics and Forecast by Product Type, 2022-2030 |
19 | Market Segmentation, Dynamics and Forecast by Application, 2022-2030 |
20 | Market Segmentation, Dynamics and Forecast by End use, 2022-2030 |
21 | Product installation rate by OEM, 2022 |
22 | Incline/Decline in Average B-2-B selling price in past 5 years |
23 | Competition from substitute products |
24 | Gross margin and average profitability of suppliers |
25 | New product development in past 12 months |
26 | M&A in past 12 months |
27 | Growth strategy of leading players |
28 | Market share of vendors, 2022 |
29 | Company Profiles |
30 | Unmet needs and opportunity for new suppliers |
31 | Conclusion |
32 | Appendix |