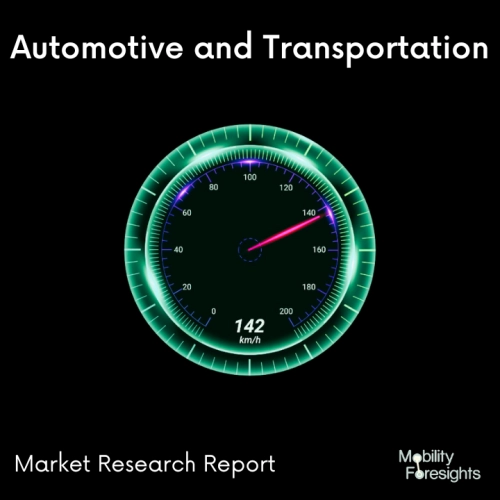
- Get in Touch with Us
Last Updated: Apr 25, 2025 | Study Period: 2023-2030
EPDM is a conformable, impermeable, and effective insulator elastomer that is long-lasting. As well as membranes and diaphragms, solid EPDM and expanded EPDM foam are frequently used for sealing and gasketing. When a component needs to be flexible and resist fluid flow, EPDM is frequently employed. It can also be used to offer flexibility or cushioning.
Despite having a respectable tensile strength, EPDM is too flexible to be used on rigid elements like gears, shafts, and structural beams. Weatherstripping, refrigerator and freezer door seals (where it also serves as an insulator), face masks for industrial respirators, glass run channels, radiators, garden and appliance hose (where it is used as a hose material as well as for gaskets), tubing, washers, O-rings, electrical insulation, and geomembranes are among the items made from it.
Ethylene propylene diene monomer rubber, or EPDM rubber, is a kind of synthetic rubber that has several uses. Ethylidene norbornene (ENB), dicyclopentadiene (DCPD), and vinyl norbornene (VNB) are dienes that are employed in the production of EPDM rubbers. According to ASTM standards, EPDM is an M-Class rubber, which includes elastomers with a saturated polyethylene chain (the M deriving from the more correct term polymethylene).
Ethylene, propylene, and a diene comonomer that facilitates crosslinking through sulphur vulcanization are the ingredients used to make EPDM. EPR, or ethylene propylene rubber, is EPDM's older sibling. It is excellent for high-voltage electrical cables but is not generated from any diene precursors and can only be crosslinked with radical chemicals like peroxides.
Like the majority of rubbers, EPDM is typically combined with fillers such as carbon black and calcium carbonate, plasticizers like paraffinic oils, and only when it is crosslinked does it acquire functional rubbery qualities.
While vulcanization with sulphur is the primary method for crosslinking, phenolic resins or peroxides can also be used (for higher heat resistance). Foams, wire, and cable are occasionally made using high-energy radiation, such as electron beams.
Below are listed some typical characteristics of EPDM vulcanizates. To a certain extent, EPDM can be blended to achieve specified qualities; however, this is dependent on the EPDM polymers available, followed by the processing and curing method(s) used. There are several different molecular weights of EPDMs available, as well as ones with different amounts of ethylene, a third monomer, and oil.
The Global EPDM fluid transfer system market accountedfor $XX Billion in 2021 and is anticipated to reach $XX Billion by 2030, registering a CAGR of XX% from 2022 to 2030.
EPDM, also known as ethylene propylene diene terpolymer, is a strong substance designed to survive the worst conditions. It is resistant to harsh chemicals and high heat. Despite being a rough material, it need not be difficult to work with. EPDM products enable effective manufacturing and are cleaner and simpler to use.
The industry's broadest variety of ethylene content is seen in NORDEL EPDM materials. These premium, essentially gel-free polymers, which come in grades with ultra-high molecular weight and oil extensions, are a great option for a wide range of automotive, building, consumer, and other applications.
The NORDEL EPDM portfolio, which is readily available in both bale and free-flowing pellet forms, is steadily growing with new solutions designed to address particular customer and industry needs.
Sl no | Topic |
1 | Market Segmentation |
2 | Scope of the report |
3 | Abbreviations |
4 | Research Methodology |
5 | Executive Summary |
6 | Introduction |
7 | Insights from Industry stakeholders |
8 | Cost breakdown of Product by sub-components and average profit margin |
9 | Disruptive innovation in the Industry |
10 | Technology trends in the Industry |
11 | Consumer trends in the industry |
12 | Recent Production Milestones |
13 | Component Manufacturing in US, EU and China |
14 | COVID-19 impact on overall market |
15 | COVID-19 impact on Production of components |
16 | COVID-19 impact on Point of sale |
17 | Market Segmentation, Dynamics and Forecast by Geography, 2023-2030 |
18 | Market Segmentation, Dynamics and Forecast by Product Type, 2023-2030 |
19 | Market Segmentation, Dynamics and Forecast by Application, 2023-2030 |
20 | Market Segmentation, Dynamics and Forecast by End use, 2023-2030 |
21 | Product installation rate by OEM, 2023 |
22 | Incline/Decline in Average B-2-B selling price in past 5 years |
23 | Competition from substitute products |
24 | Gross margin and average profitability of suppliers |
25 | New product development in past 12 months |
26 | M&A in past 12 months |
27 | Growth strategy of leading players |
28 | Market share of vendors, 2023 |
29 | Company Profiles |
30 | Unmet needs and opportunity for new suppliers |
31 | Conclusion |
32 | Appendix |