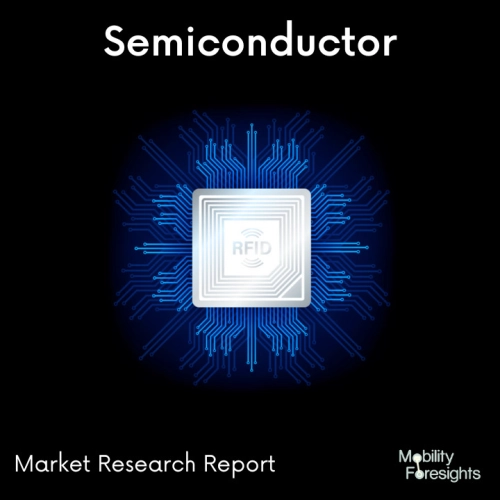
- Get in Touch with Us
Last Updated: Apr 25, 2025 | Study Period: 2024-2030
Equipment for epitaxy deposition is essential for research and production in the semiconductor industry. The process of depositing a thin crystalline layer onto a substrate with a compatible crystal structure is known as epitaxy, also known as epitaxial growth.
Electronic devices including integrated circuits (ICs), light-emitting diodes (LEDs), and solar cells are frequently made using this process.
The formation of these thin films may be precisely controlled using epitaxy deposition equipment, enabling for the construction of intricate semiconductor devices with the required characteristics. It usually includes a control unit, a substrate holder, a gas supply system, and a deposition chamber.
The epitaxial development takes place in a controlled environment provided by the deposition chamber.
In order to remove contaminants and guarantee the quality of the deposited film, it is normally a vacuum chamber. During the deposition process, the substrate, which is typically a semiconductor wafer, is held firmly in place by the substrate holder.
Precursor gases must be delivered into the deposition chamber via the gas delivery system. These precursor gases include dopants and semiconductor materials, which are necessary for the epitaxial development. To produce the required film formation, the gas flow rates and compositions are accurately regulated.
The entire deposition process is managed and watched over by the control unit. It has a number of sensors and tools for measuring and controlling variables including temperature, pressure, and gas flow. The control device makes sure that the deposition circumstances are ideal for the development of premium films.
The Global Epitaxy Deposition Equipment Market accounted for $XX Billion in 2022 and is anticipated to reach $XX Billion by 2030, registering a CAGR of XX% from 2024 to 2030.
For the large volume production of the most recent Silicon Carbide ("SiC") power devices on SiC wafers, AIXTRON SE unveiled its new G10-SiC 200 mm system.
This high-temperature CVD system was just unveiled at the International Conference on Silicon Carbide and Related Materials (ICSCRM), which is presently taking place in Davos, Switzerland. It advances innovation to a new level. SiC, a material with a broad bandgap, is expected to be widely used in future power electronics.
SiC makes a significant contribution to our modern society's decarbonization and so promotes climate protection. The need to minimise reliance on oil supply is fueling an increase in the demand for SiC wafers that is being driven by the increasing use of SiC-based power semiconductors in electromobility solutions.
Sl no | Topic |
1 | Market Segmentation |
2 | Scope of the report |
3 | Abbreviations |
4 | Research Methodology |
5 | Executive Summary |
6 | Introduction |
7 | Insights from Industry stakeholders |
8 | Cost breakdown of Product by sub-components and average profit margin |
9 | Disruptive innovation in the Industry |
10 | Technology trends in the Industry |
11 | Consumer trends in the industry |
12 | Recent Production Milestones |
13 | Component Manufacturing in US, EU and China |
14 | COVID-19 impact on overall market |
15 | COVID-19 impact on Production of components |
16 | COVID-19 impact on Point of sale |
17 | Market Segmentation, Dynamics and Forecast by Geography, 2024-2030 |
18 | Market Segmentation, Dynamics and Forecast by Product Type, 2024-2030 |
19 | Market Segmentation, Dynamics and Forecast by Application, 2024-2030 |
20 | Market Segmentation, Dynamics and Forecast by End use, 2024-2030 |
21 | Product installation rate by OEM, 2023 |
22 | Incline/Decline in Average B-2-B selling price in past 5 years |
23 | Competition from substitute products |
24 | Gross margin and average profitability of suppliers |
25 | New product development in past 12 months |
26 | M&A in past 12 months |
27 | Growth strategy of leading players |
28 | Market share of vendors, 2023 |
29 | Company Profiles |
30 | Unmet needs and opportunity for new suppliers |
31 | Conclusion |
32 | Appendix |