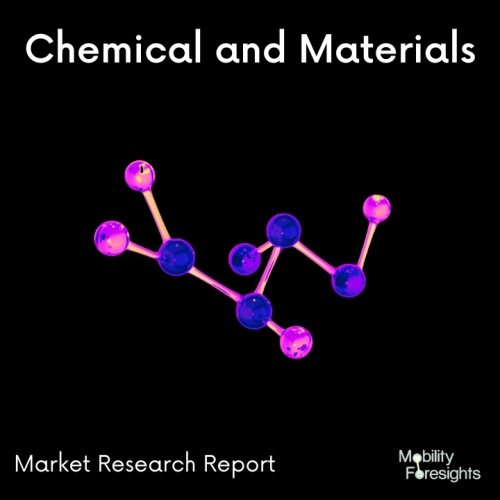
- Get in Touch with Us
Last Updated: Apr 25, 2025 | Study Period: 2024-2030
Epoxy molding compounds were developed specifically for the encapsulation of electrical devices. High-performance integrated circuits (ICs) include reducing device features and high speed characteristics on larger semiconductor dies in smaller and thinner packaging. In VLSI and microprocessor units, the degree of integration keeps rising. Complexity has increased with plastic packaging.
Automobile applications, automation, and the development of strong, portable computer architectures are all driving drivers. The car industry serves as an illustration of how much people are depending on microelectronic gadgets.
The future belongs to surface mount technology. Cost is a big factor in a lot of contemporary electronic applications. Due to its importance to high technology, semiconductor epoxy molding compounds have kept up with all of these rigorous improvements.
The Global Epoxy molding compounds market accounted for $XX Billion in 2023 and is anticipated to reach $XX Billion by 2030, registering a CAGR of XX% from 2024 to 2030.
Kyocera Announces Innovative Epoxy Molding Compound, High-Thermal-Conductive Silver Sintering Paste. Higher alumina filler loading allowed the new product to attain an extraordinarily high thermal conductivity while still keeping outstanding flow ability. Both compression and transfer moldings are offered.
It is conceivable to do away with the heatsink and make the package structure easier to design by employing this high-thermal-conductivity molding compound to increase the thermal dispersion of packages.
An innovative, environmentally friendly silver sintering paste will also be made available by the firm. This formulation is a patented one that was created expressly to outperform high-lead solders in terms of advantages and performance. Lead-free pressure less silver sintering paste from Kyocera has a very strong bond to bare copper and good thermal and electrical performance.
The newly developed paste is perfect for high-reliability applications where heat dissipation is important, such as power semiconductors, automotive modules, and high-brightness LEDs, thanks to these properties.
Based on Nano-Silver technology, Kyocera's silver sintering paste shows exceptional die-shear adhesion to bare copper, silver, and gold-plated surfaces and thermal conductivity of more than 200W/mK.
The heat conductivity of Kyocera's silver sintering paste is more than three times greater than that of conventional solders and electrically conductive die-attach pastes. Moreover, the paste exhibits outstanding interface dependability in the most demanding applications because to the use of a new resin-dispersion technology.
The early microelectronic powders, which were crystalline silica-filled, anhydride-cured Bis-A type epoxies, had low glass transition temperatures and high coefficients of thermal expansion.
The usage of (FS) fused silica-filled systems based on ECN (Epoxy Cresylic Novo lac) resins and phenolic novo lac hardeners considerably improved both characteristics.
With normal TGs of 150â175°C, ECN evolved as the workhorse resin. The glass transition temperature (Tg) argument is now taking place in the industry, and depending on the application, both are pursued. Epoxies in the CTE region are moving in the direction of continuously reducing thermal expansion, mostly by raising their FS level, which is a reasonable progression given the demands of low-stress packages.
Package performance has improved due to developments in resin and filler technologies, including the introduction of spherical FS and a move towards finer filler particles. It is necessary to gradually reduce package stress as memory devices (including those with 4â16 Megabits), SOICs, QFPs, and many other packages advance.
Using CTE/modulus data from Thermal or Dynamic Mechanical Analyses, one may determine the compressive stress of epoxy packages. The current low-stress situation and trend are reflected in these phrases. Improved thermal cycle and thermal shock performance are related to low stress. As a result, there are rising trends in certain epoxy characteristics.
For improved moisture performance, it's crucial to choose pure raw materials for epoxies. Ionic contaminants can swiftly erode ever-finer and thinner alienization patterns on highly integrated silicon circuits.
Epoxies and their basic ingredients now contain much less impurities than they did twenty years ago. Hydrogen ion concentration (pH) and water extract conductivity are other factors that affect aluminum corrosion. Because mobile ions like Cl- and Na+ are so dangerous, their concentrations have been greatly lowered.
Epoxies must support, not impede, package manufacture while placing a focus on excellent performance. In comparison to automatic molding (in 1-4 cavities with multi-plungers), conventional multi-cavity transfer molding has lost productivity and quality uniformity. Important moldability factors include cure time, hot strength, and release without early cavity staining.
The proportion of non-staining injections is rising over time. The impact of molding on internal IC features like wire sweep and paddle shift are also taken into account.
Epoxy packaging made of thin, big chips requires anti-popcorn functionality and extremely low stress. Epoxies for megabit memory devices must have minimal alpha radiation and meet higher requirements for moisture reliability. This study examines the state-of-the-art, technique, recent advancements in semiconductor grade epoxies, and some property predictions for the near future.