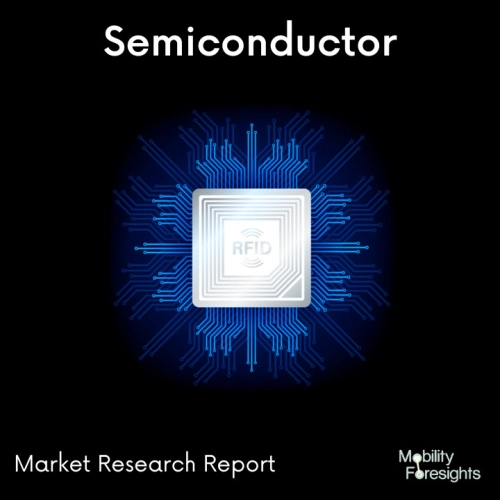
- Get in Touch with Us
Last Updated: Apr 25, 2025 | Study Period: 2024-2030
The advent of factory automation has revolutionized the manufacturing landscape, driving increased efficiency, precision, and productivity. At the heart of this transformation lie factory automation sensors, which serve as the critical link between physical processes and automated control systems.
These sensors enable the seamless integration of machinery, facilitate data-driven decision-making, and empower industries to achieve optimal performance in today's competitive market. This introduction provides an overview of factory automation sensors, emphasizing their significance, types, and their profound impact on modern industrial automation.
Sensors for factory automation are specialized tools used to record, gauge, and transform physical data into electrical impulses. Automated systems then make use of these signals to enable control, observation, and analysis of many aspects of the production environment. Factory automation sensors offer precise and quick modifications to improve manufacturing operations by continuously collecting real-time data.
The range of factory automation sensors is extensive, tailored to meet specific application requirements. Proximity sensors, for instance, are employed to detect the presence or absence of objects within a defined range, utilizing technologies like inductive, capacitive, or optical principles. Photoelectric sensors employ light beams to detect objects, enabling precise positioning, counting, or quality control in manufacturing operations.
Pressure sensors play a vital role in monitoring and regulating the pressure levels of liquids, gasses, or air, ensuring safe and efficient operation of pneumatic and hydraulic systems. Temperature sensors provide valuable insights into thermal conditions, enabling precise temperature control and preventing overheating or damage to machinery.
Level sensors are utilized for measuring the levels of liquids or solids in tanks or containers, facilitating inventory management and preventing spills or shortages. Flow sensors, on the other hand, monitor the flow rates of liquids or gasses, ensuring optimal flow control, and enabling accurate dosing, mixing, or distribution.
Industrial automation is significantly impacted by factory automation sensors. Real-time data collecting made possible by these sensors allows for proactive decision-making, preventive maintenance, and ongoing process improvement.
Automation sensors increase production by lowering the need for human involvement, eliminating human error, and enhancing efficiency. Additionally, by seeing risky situations and launching the proper responses, these sensors help to improve worker safety by lowering the likelihood of mishaps and injuries.
In conclusion, the success of contemporary industrial automation is greatly influenced by factory automation sensors. These sensors enable industries to reach previously unheard-of levels of efficacy, accuracy, and productivity by offering real-time data, precise control, and monitoring capabilities.
The future of manufacturing processes holds the promise of improved performance, cost-effectiveness, and sustainability thanks to the ongoing developments in sensor technology and their integration into automation systems.
The Europe Factory Automation Sensor market accounted for $XX Billion in 2022 and is anticipated to reach $XX Billion by 2030, registering a CAGR of XX% from 2024 to 2030.
With an emphasis on robotics and factory automation, Renesas Electronics has introduced three families of microcontrollers for motor control applications.Over 35 new goods from the three families are included, including RX and RA family devices.
Trigonometric function units (TFUs) for acceleration, a sophisticated ADC with an integrated PGA, as well as a variety of communication interfaces, including CAN FD, are just a few of the characteristics and capabilities that two sets of its ARM Cortex-M devices from the RA Family have specifically for motor control applications.
Nvidia is planning to build ten million electronics plants.RISC-V's first motor control-focused chipWith up to 256 KB of flash and 40 KB of SRAM, the RA4T1 Group operates at 100 MHz. The RA6T3 Group offers 256KB of flash and 40 KB of SRAM at a 200 MHz operating frequency. The Renesas Flexible Software Package (FSP) supports both groups for simple design porting from other RA family devices.
The RX26T Group, based on an internal RX core running at 120 MHz with up to 512KB of dual bank flash memory to allow no-wait access and 64KB SRAM, is the third group of microcontrollers. To ensure precise control and great noise immunity, these accept 5V power supplies.
Along with dual motor support, TFUs, on-chip clocking, interrupt control, and PFC control via a 120 MHz PWM (2 channels of three-phase complementary + 2 channels of single-phase complimentary), three 12-bit ADCs, these also offer these features. To minimize the size and material requirements, the device has a built-in high-speed on-chip oscillator in a tiny QFN packaging (48-HWQFN: 7x7mm, 64-HWQFN: 9x9mm). Additionally, it has compatibility for I3C basic and next-generation CAN FD.
1 | Market Segmentation |
2 | Scope of the report |
3 | Abbreviations |
4 | Research Methodology |
5 | Executive Summary |
6 | Introduction |
7 | Insights from Industry stakeholders |
8 | Cost breakdown of Product by sub-components and average profit margin |
9 | Disruptive innovation in the Industry |
10 | Technology trends in the Industry |
11 | Consumer trends in the industry |
12 | Recent Production Milestones |
13 | Component Manufacturing in US, EU and China |
14 | COVID-19 impact on overall market |
15 | COVID-19 impact on Production of components |
16 | COVID-19 impact on Point of sale |
17 | Market Segmentation, Dynamics and Forecast by Geography, 2024-2030 |
18 | Market Segmentation, Dynamics and Forecast by Product Type, 2024-2030 |
19 | Market Segmentation, Dynamics and Forecast by Application, 2024-2030 |
20 | Market Segmentation, Dynamics and Forecast by End use, 2024-2030 |
21 | Product installation rate by OEM, 2023 |
22 | Incline/Decline in Average B-2-B selling price in past 5 years |
23 | Competition from substitute products |
24 | Gross margin and average profitability of suppliers |
25 | New product development in past 12 months |
26 | M&A in past 12 months |
27 | Growth strategy of leading players |
28 | Market share of vendors, 2023 |
29 | Company Profiles |
30 | Unmet needs and opportunity for new suppliers |
31 | Conclusion |
32 | Appendix |