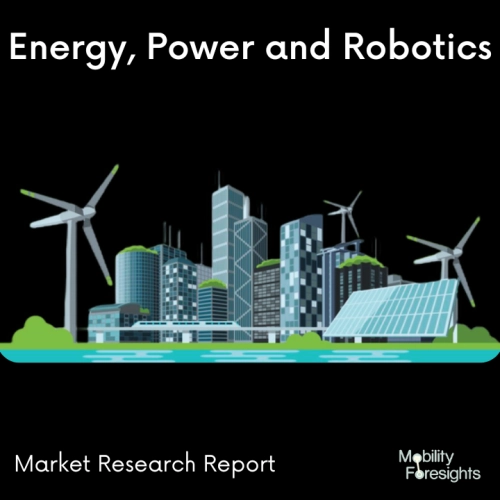
- Get in Touch with Us
Last Updated: Apr 25, 2025 | Study Period: 2023-2030
Injection molding is a manufacturing process for producing parts from both thermoplastic and thermosetting plastic materials. It is widely used in Europe for producing a variety of complex parts with high precision and accuracy.
Injection molding machines are made up of two main components: a hopper and an injection unit. The hopper holds the raw material in either solid pellets or liquid form. The injection unit melts the material, injects it into the mold cavity under pressure, and then cools it to form the final product.
Injection molding machines come in a variety of sizes suitable for both small and large production runs. Generally, smaller machines are used for prototyping, while large machines are for mass production. An important factor to consider is clamping force, which determines the size of the machine required to achieve the desired result.
European-made injection molding machines range from 450 to 3000 metric tons in clamping force.
In terms of features, some injection molding machines are equipped with additional capabilities such as multi-color production, robot integration, and hot runner systems. Depending on the purpose, special auxiliary equipment can be added for temperature control or process automation.
To facilitate the efficient production of parts, special molds are designed by the molding process and machined to precision tolerances. Nowadays, injection molding machines have become highly advanced, providing more flexibility and efficiency for manufacturers.
With the help of European injection molding machines, designers and manufacturers can produce sophisticated parts without compromising on the quality.
The Europe injection molding machine market accounted for $XX Billion in 2022 and is anticipated to reach $XX Billion by 2030, registering a CAGR of XX% from 2023 to 2030.
To make the dry molded fiber more widely available, PulPac is introducing the PulPac Scala, a new machine platform that combines its Mill-to-Web fiber unit with injection molding technology. An estimated yearly production of injection molding machines is made, many of which are limited to producing single-use plastic. To address this, the PulPac Scala fits into a foot container, requires less money upfront than the PulPac Modula, and offers Dry Molded Fiber to consumers.
PulPac is now releasing the small, purportedly scalable Dry Molded Fiber machine platform in conjunction with its turnkey partner Huarong Group. The fiber-forming technology aims to surpass the global consumption of single-use plastics and promises efficiency in terms of resources, energy, and cost.
To satisfy the rising demand for environmentally friendly packaging options, Curt G. Joa, Inc. collaborated with PulPac earlier to introduce the PulPac Modula production platform for Dry Molded Fiber to the North American market. In addition, SustainaPac LLC became a part of PulPac's licensee network to utilize Dry Molded Fiber technology to create single-use foodservice packaging items for the quick service restaurant industry in North America.
Sl no | Topic |
1 | Market Segmentation |
2 | Scope of the report |
3 | Abbreviations |
4 | Research Methodology |
5 | Executive Summary |
6 | Introduction |
7 | Insights from Industry stakeholders |
8 | Cost breakdown of Product by sub-components and average profit margin |
9 | Disruptive innovation in the Industry |
10 | Technology trends in the Industry |
11 | Consumer trends in the industry |
12 | Recent Production Milestones |
13 | Component Manufacturing in US, EU and China |
14 | COVID-19 impact on overall market |
15 | COVID-19 impact on Production of components |
16 | COVID-19 impact on Point of sale |
17 | Market Segmentation, Dynamics and Forecast by Geography, 2023-2030 |
18 | Market Segmentation, Dynamics and Forecast by Product Type, 2023-2030 |
19 | Market Segmentation, Dynamics and Forecast by Application, 2023-2030 |
20 | Market Segmentation, Dynamics and Forecast by End use, 2023-2030 |
21 | Product installation rate by OEM, 2023 |
22 | Incline/Decline in Average B-2-B selling price in past 5 years |
23 | Competition from substitute products |
24 | Gross margin and average profitability of suppliers |
25 | New product development in past 12 months |
26 | M&A in past 12 months |
27 | Growth strategy of leading players |
28 | Market share of vendors, 2023 |
29 | Company Profiles |
30 | Unmet needs and opportunity for new suppliers |
31 | Conclusion |
32 | Appendix |