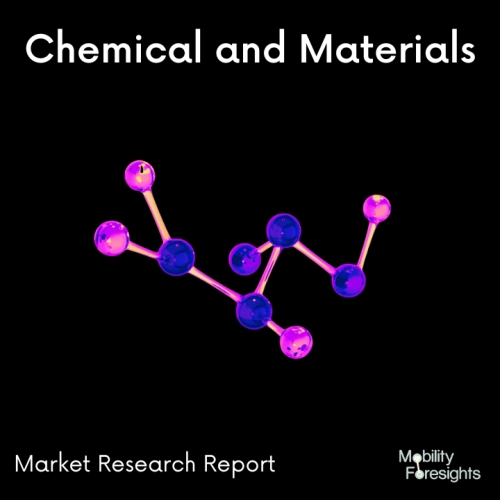
- Get in Touch with Us
Last Updated: Apr 25, 2025 | Study Period: 2023-2030
Medical-grade plastic materials are polymers that are used to produce medical items and devices such as prosthesis and syringes. It is also utilized in the production of in vitro diagnostic tests and primary pharmaceutical packaging, which retains and confines medications to prevent contamination.
Medical plastic devices are widely used. Polyethylene, for example, has a variety of medical applications. However, polyethylene is employed in both everyday life and industrial uses. It all boils down to how medical-grade polyethylene is defined.
A medical-grade polymer has no regulatory definition. The ISO 10993 standard specifies the specifications for materials that can be used in medical devices. In principle, producers can employ any material in medical devices as long as the overall device fits those specifications.
The concept of biocompatibility is the same for every material: the device must be compatible with biological systems, i.e. the human body.
ISO 10993-compliant devices fulfill high criteria.ISO 10993 is regarded as the standard for medical-grade materials, even if the materials are not exactly medical grade.
As a result, material suppliers and others in the medical-device sector have developed their own definition of what qualifies as a medical-grade plastic. As a result, the performance and quality of medical-grade polymers might vary from provider to supplier.
The German Engineers Europe Association, VDI, issued a voluntary advice document detailing the definition of medical-grade plastics. It has not yet been implemented, however it may be a question of time. As a result, producers of plastic medical devices would have to demonstrate that they employ consistent formulas.
Any plastic can be used in medical-grade products. Consider the polymer polystyrene. Medical-grade plastic producers design the resins with procedures that improve biocompatibility. Polystyrene medicinal uses range from petri dishes to implants as a result.
Another common material is medical-grade ABS plastic, which is utilized in drug-delivery systems and tracheal tubes. Catheters and surgical equipment are examples of polyethylene medical uses.
Medical-grade resins are becoming available in a variety of materials, including PEEK and Polyetherimide (PEI), but there is no hard-and-fast biocompatible plastics list to help designers. It is dependent on how the polymers are designed to be biocompatible.
The Europe Medical Grade Polymers Market accounted for $XX Billion in 2022 and is anticipated to reach $XX Billion by 2030, registering a CAGR of XX% from 2023 to 2030.
Navient Corporation, a leading producer of specialized and sustainable material solutions and services, announced today the extension of its bio-based Mevopur medical-grade polymer solutions line.
The bio-based polycarbonate, ABS, or styrenic polymers used in the new color and additive concentrates and customized ready-to-use formulations. These are in addition to the bio-based polyolefin materials introduced by Avient.
Pharmapack is featuring these more sustainable additions to the Mevopur range.Using the novel bio-based Mevopur polymer solutions instead of traditional materials can assist pharmaceutical packaging, medical device, and related product producers in lowering their carbon footprint.
Furthermore, because they are manufactured in accordance with Mevopur regulations, these polymer solutions can assist businesses in lowering their risk of regulatory noncompliance.
The new Mevopur concentrates, which are made from non-fossil feedstocks, contain polymers with bio-based content, according to the ASTM D6866 standard. They are more sustainable drop-in substitutes for fossil-based materials, as well as pre-colored formulas for consumers who want ready-to-use solutions.
These bio-based materials may be processed on regular injection molding machines and extruders and recycled through the same channels as traditional fossil-based polymers.
They, like other Mevopur formulations, are manufactured in dedicated facilities in accordance with ISO 13485-2016 regulations and are backed by testing in accordance with ISO 10993-1, USP, European Pharmacopoeia, and ICH Q3D requirements.
Documented change control beyond the CAS number is practiced, and documentation for the Registered Drug Master File (DMF) / Device Master File (MAF) is maintained.
Sl no | Topic |
1 | Market Segmentation |
2 | Scope of the report |
3 | Abbreviations |
4 | Research Methodology |
5 | Executive Summary |
6 | Introduction |
7 | Insights from Industry stakeholders |
8 | Cost breakdown of Product by sub-components and average profit margin |
9 | Disruptive innovation in the Industry |
10 | Technology trends in the Industry |
11 | Consumer trends in the industry |
12 | Recent Production Milestones |
13 | Component Manufacturing in US, EU and China |
14 | COVID-19 impact on overall market |
15 | COVID-19 impact on Production of components |
16 | COVID-19 impact on Point of sale |
17 | Market Segmentation, Dynamics and Forecast by Geography, 2023-2030 |
18 | Market Segmentation, Dynamics and Forecast by Product Type, 2023-2030 |
19 | Market Segmentation, Dynamics and Forecast by Application, 2023-2030 |
20 | Market Segmentation, Dynamics and Forecast by End use, 2023-2030 |
21 | Product installation rate by OEM, 2023 |
22 | Incline/Decline in Average B-2-B selling price in past 5 years |
23 | Competition from substitute products |
24 | Gross margin and average profitability of suppliers |
25 | New product development in past 12 months |
26 | M&A in past 12 months |
27 | Growth strategy of leading players |
28 | Market share of vendors, 2023 |
29 | Company Profiles |
30 | Unmet needs and opportunity for new suppliers |
31 | Conclusion |
32 | Appendix |