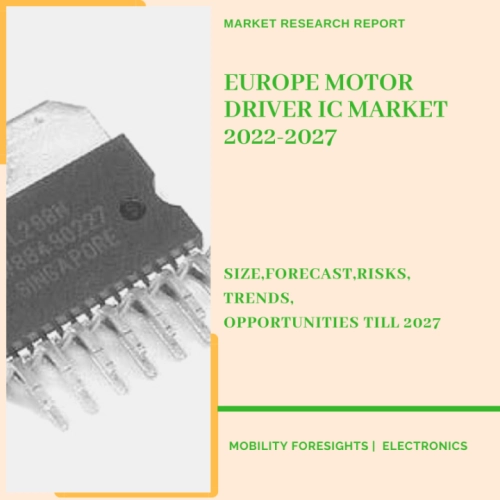
- Get in Touch with Us
Last Updated: Apr 26, 2025 | Study Period: 2022-2027
In robotics, motor driver ICs are frequently used to operate DC motors from microcontrollers.
They are commonly utilized in automation since they are an important component in controlling motion in autonomous robots. They're also found in more everyday places like workplace appliances and automobile electronics.
The Europe motor driver IC market accounted for $XX Billion in 2021 and is anticipated to reach $XX Billion by 2026, registering a CAGR of XX% from 2022 to 2027.
Toshiba Electronics Europe GmbH ("Toshiba") has announced the release of a three-phase brushless DC (BLDC) motor control pre-driver IC for high-speed motors such as server fans, pumps, blowers, and suction motors for cordless and robotic vacuum cleaners.
The new Toshiba TC78B011FTG features a sine-wave drive system that reduces vibration and noise. Its sensorless design saves space and money by eliminating the need for a Hall sensor.
Without the use of an external microcontroller, the built-in closed loop speed control regulates and maintains the motor's rotational speed throughout dynamic power supply fluctuations and load variations (MCU). The built-in non-volatile memory can be programmed to precisely set a speed profile (NVM).
Allegro MicroSystems Europe's A3903 is a low-voltage bidirectional DC motor driver IC in a 2 mm square and 0.55 mm high ultra-compact packaging.
The new device has a typical input voltage range of 3 to 5.5 V and can deliver up to 500 mA of output current. To provide a constant voltage across the motor coil, the output uses a full-bridge circuit with source-side linear operation.
Motor voltage changes caused by current variations and battery voltage fluctuations are minimised with this regulated output.
Sl no | Topic |
1 | Market Segmentation |
2 | Scope of the report |
3 | Abbreviations |
4 | Research Methodology |
5 | Executive Summary |
6 | Introduction |
7 | Insights from Industry stakeholders |
8 | Cost breakdown of Product by sub-components and average profit margin |
9 | Disruptive innovation in the Industry |
10 | Technology trends in the Industry |
11 | Consumer trends in the industry |
12 | Recent Production Milestones |
13 | Component Manufacturing in US, EU and China |
14 | COVID-19 impact on overall market |
15 | COVID-19 impact on Production of components |
16 | COVID-19 impact on Point of sale |
17 | Market Segmentation, Dynamics and Forecast by Geography, 2022-2027 |
18 | Market Segmentation, Dynamics and Forecast by Product Type, 2022-2027 |
19 | Market Segmentation, Dynamics and Forecast by Application, 2022-2027 |
20 | Market Segmentation, Dynamics and Forecast by End use, 2022-2027 |
21 | Product installation rate by OEM, 2022 |
22 | Incline/Decline in Average B-2-B selling price in past 5 years |
23 | Competition from substitute products |
24 | Gross margin and average profitability of suppliers |
25 | New product development in past 12 months |
26 | M&A in past 12 months |
27 | Growth strategy of leading players |
28 | Market share of vendors, 2022 |
29 | Company Profiles |
30 | Unmet needs and opportunity for new suppliers |
31 | Conclusion |
32 | Appendix |