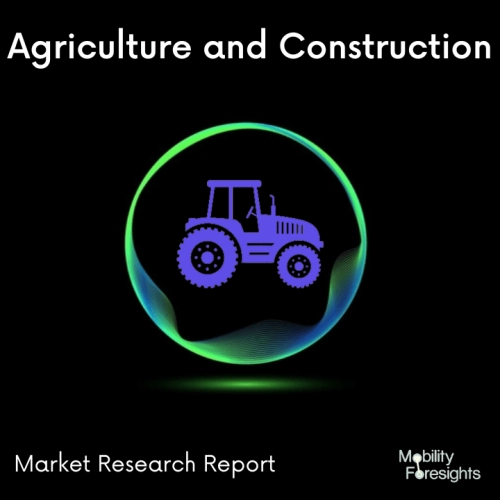
- Get in Touch with Us
Last Updated: Apr 25, 2025 | Study Period: 2024-2030
Steel tubing are manufactured with extremely tight tolerances. During the production process, tubulars are subjected to many dimensional quality inspections, including straightness, roundness, wall thickness, and surface.
Mechanical strength is an important consideration for tubes. Steel tubing is utilised in a variety of industrial applications, most notably the transmission of water, gases, and liquid waste.
Steel tubes are a typical component of industrial machinery, and may be found in conveyor belts, hydraulic lifts, mills, and a variety of other applications.
They are manufactured in two ways, resulting in either a welded or a seamless pipe. Raw steel is initially cast into a more practical beginning form in both procedures. It is then formed it in to a pipeline through extending the metal into a seamless tube or through pressing the edges together and sealing them with a sealant.
The earliest technologies for manufacturing steel pipe were established in the early 1800s, and they have gradually evolved into the current procedures designers employ nowadays.
Millions of tonnes of steel pipe are manufactured each year. Because of its flexibility, this was the most often utilised commodity manufactured by the steel production. Seamless tubes are lighter in mass and have smaller diameter. These have been used to carry bicycles and liquids. Seamed tubes are more stiff and heavier.
They are more consistent and usually straighter. Tubes can be used for a variety of purposes, including gas transfer, electrical conduits, and piping. They are often employed when the pipe is not subjected to a significant levels of sensitivity.
S No | Overview of Development | Development Detailing | Region of Development | Possible Future Outcomes |
1 | Tube manufacturer invests in flexible, automated mill technology | Although a small company making tube on just a couple of mills, Dundeeâs manufacturing capability was reasonably diverse then as it is now. | Global Scale | This would enhance better Technologies and production |
Steel tubes have risen in importance in the resource sector in conveying fluids and also in the shape of conveyor system rolling, bearings shells, and cement piling housings in recent years. In addition, as unconventional shale extraction has increased, steel tubing is being utilised to transport chromite, which now has resulted in an increase in output.
These are also employed in the mechanical construction of heat transfer, converters, and burner pipes in warming, ventilating, and air conditioning (HVAC) and cooling units.
Furthermore, there is now an increase in demand with metal tubes in the vehicle industry since they are dependable and have ideal toughness and chemical resistance capabilities. These tubing also have an energy absorbing capability and are well-built.
As a result of these features, the global usage of steel tubes has increased. Additionally, the decreased or cheap maintenance cost of steel tubes is an essential element contributing to the growth of the steel tubing industry.
Steel tubes have several uses in the engineering sector, which is a fast-growing end-user industrial area. Increased competition for metal tubes in European Nations expanding economies, as well as diverse technical requirements, are creating possibilities for the steel tubes market.
The use of new steel tubes in comparison to the traditional tubing is also propelling the steel tubes industry forward. These elements have an important role in influencing and contributing to the expansion.
The Europe Steel Tube Market can be segmented into following categories for further analysis.
Steel tubes are robust, strong, and long-lasting metallic tubing that come in a variety of forms, include squared, oblong, and then round. Those structures are made using iron alloys containing different additional components such as carbon, tungsten, manganese, aluminium, and titanium.
Steel tubing are classified into two varieties based on their process of production: smooth versus welding. Steel tubes offer a greater manufacture tolerances, which aids in their manufacture and assembly overall reliability.
They are employed in a variety of sectors because to their adaptability, encompassing oil and natural gas, chemical products, architecture and development, automobile, treatment plants, and so on.
Tubing cost efficiency and rising utilisation in different industry-based purposes in contrast to traditional tubing are also helping to the reinforced steel market development. This prototype of that front wheel carriers for hybrid vehicles was among the most recent developments in automotive tube solutions.
Another lightening breakthrough that may be of interest to automakers the use of welding tubing built from a chromoly steel with enhanced strength and above-average machinability.
Additionally, the automobile sector should soon profit from ultra-high-strength tubing, which appear to be suitable for use in novel car active suspension. Pre-tubes for the manufacturing of injection anchors are among the commercial processes of uninterrupted accuracy tubing.
Despite the increasing usage of metal tubes inside the household and business domains, finished are continuously seeking for less expensive and so more efficiency tubing replacements. The increasing availability of iron and plastic is resulting in the rise of iron and plastic tubes in end-user sectors, which have been significantly less expensive than metal tubes.
Additionally, new designs and properties of tubing allow greater effectiveness in a variety of end-use industries. This may result in steel tubing being replaced with plastic or iron tubes, restricting the development of the metal tubes industry in the next decades.
Thyssenkrupp Precision Steel is part of the growing force of consumers based upon the varied levels of products launched under steel tubes of the European market. The Thyssenkrupp Precision Steel in Hohenlimburg has unveiled a new element for fully electric underpinnings.
Inside this consortium, the firm specialised in medium-wide sheets and functioned as a collaboration collaborator in producing a super-light tube composed of high-strength steel (HBS 800). Because less material is required, the optimised chassis component seems to save all the manufacturers more than 34% in mass.
Because it is one-third lighter, the material is supposed to provide advantages such as faster manufacturing times and fewer waste. Tube stabilisers constructed of manganese-boron steel are another part of the future automobile idea.
Sandvik has been growing towards newer integration of the technologies focusing on better and optimised requirements based on the customer needs. The Sandvik's high-precision carbon steel tubes operation in Werther, Germany, is located here.
This has been making thick-walled continuous tubing with exceptionally low flaws (at least 50 m) that really can withstand loads of up to 160,000 psi (12,000 bar). Or creating tubing which retains structural qualities even after chilling a fusion generator running at 100 million degrees Celsius.
So because company's high-precision tubes part of a growing thick-walled accuracy tubes (OD 1-70 mm) in materials ranging from advanced steel material to unique superalloys. This high-pressure tube can withstand forces of up to 12,000 bar (160,000 psi).
Sl no | Topic |
1 | Market Segmentation |
2 | Scope of the report |
3 | Abbreviations |
4 | Research Methodology |
5 | Executive Summary |
6 | Introduction |
7 | Insights from Industry stakeholders |
8 | Cost breakdown of Product by sub-components and average profit margin |
9 | Disruptive innovation in theIndustry |
10 | Technology trends in the Industry |
11 | Consumer trends in the industry |
12 | Recent Production Milestones |
13 | Component Manufacturing in US, EU and China |
14 | COVID-19 impact on overall market |
15 | COVID-19 impact on Production of components |
16 | COVID-19 impact on Point of sale |
17 | Market Segmentation, Dynamics and Forecast by Geography, 2022-2027 |
18 | Market Segmentation, Dynamics and Forecast by Product Type, 2022-2027 |
19 | Market Segmentation, Dynamics and Forecast by Application, 2022-2027 |
20 | Market Segmentation, Dynamics and Forecast by End use, 2022-2027 |
21 | Product installation rate by OEM, 2022 |
22 | Incline/Decline in Average B-2-B selling price in past 5 years |
23 | Competition from substitute products |
24 | Gross margin and average profitability of suppliers |
25 | New product development in past 12 months |
26 | M&A in past 12 months |
27 | Growth strategy of leading players |
28 | Market share of vendors, 2022 |
29 | Company Profiles |
30 | Unmet needs and opportunity for new suppliers |
31 | Conclusion |
32 | Appendix |