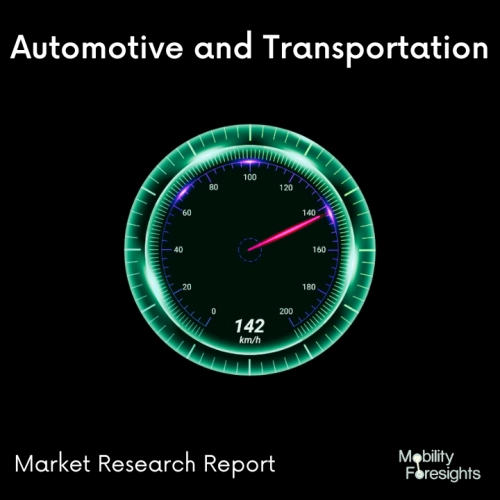
- Get in Touch with Us
Last Updated: Apr 25, 2025 | Study Period: 2024-2030
When contrasted to the internal-combustion engine (ICE) cars they displace, the lithium-ion batteries in electric vehicles (EVs) have substantially different basic necessities at the cell and pack levels.
While ICE drivetrain components rely mainly on steel and aluminium compositions, Li-ion battery packs use a wide range of materials just at cellular and pack levels, including nickel, cobalt, lithium, copper, insulation, thermal interface materials, and many more.
A vast amount of electricity, thousands of times greater than that of a smart phone, is required to operate an electric car.
As a result, EVs require dozens to thousands of battery cells. The makeup of an EV battery may differ significantly dependent on the kind of electric motor, however EV battery packs are typically made up of cells, modules, and a pack.
To handle the numerous battery cells put in a single EV in a safe and effective way, the cells are mounted in the manner of packages and modules. Another of the dangers associated with cars is combustion. Batteries have grown increasingly obvious in EVs as the quantity of EVs has increased.
The majority of BEV and PHEV fires, particularly those caused by self-ignition, begin in the rechargeable electricity system. The battery size can be compared to the gasoline volume in an ICEV's fuel tank in considerations of performance.
As a result, the EV fire is linked to the fire danger and hazard related with the battery cell and integrated services, and also the battery pack's size and volume. In general, the more batteries there are and the more electricity they can hold, the higher the flame danger for EVs.
S No | Overview of Development | Development Detailing | Region of Development | Possible Future Outcomes |
1 | Posco Chemical enters US EV battery market via GM joint venture | Posco Chemical and General Motors would create a strategic alliance and construct a facility in North America to manufacture crucial electric car materials locally. | Global Scale | This would enhance better Technologies and production |
Battery packs go through phases of 'release' during travelling and charging whenever the car is connected in. The electric potential the batteries can retain decreases when this procedure is repeated over time.
This reduced power and time needed among charging trips. Batteries have a greater energy density than standard recharging lead-acid or nickel-cadmium battery packs.
This indicates that batteries makers will be able to conserve space, resulting in a smaller total dimensions of the rechargeable battery. The electric car's batteries is a tried-and-true innovation that will survive for several generations.
OEMs are going to change the way battery packs are manufactured. Developments in power density seem to be important, but so is the sustainable development of the materials utilised.
Many of the commodities under concern have dubious mining techniques or fragile supply networks. Cobalt is however one substance, which is not only extremely expensive and seems to have a limited supply and mined in China and the Democratic Republic of the Congo.
As a consequence, OEMs are increasingly using stronger nickel cathode compositions in newer products, such as NMC 622 or NMC 811.
While Li-ion cell energy density increases may be the most visible battery advances in the public eye, we are also witnessing an increase in pack-level energy density at a faster rate than cell-level enhancements.
Suppliers are upgrading their battery architectures; the volume of components used to surround the cells is continually decreasing, permitting for a smaller battery system including the use of additional cells for much the same weight.
Those enhancements are also influenced by the substances used in numerous pack elements. Composites containers for light-weighting, fire-retardant compounds, thermally conductive equipment, and other applications are gaining popularity.
Solid Power, a maker of solid-state batteries for electric vehicles, said it plans to start shipping pre-production battery cells by the end of the year for validation testing by BMW and Ford Motor.
Solid Power's has put up a pilot production line to deliver validation samples to automakers while looking for a manufacturing partner to begin producing its cells as early as 2026, according to Solid Power's.
Korea's SK Innovation, which is establishing joint-venture battery plants with Ford in Tennessee and Kentucky, is one potential partner, he said.
Solid Power has enough pilot production capability to supply other car manufacturers with prototype battery cells. Hyundai and Samsung, as well as Ford and BMW, were among the early investors in the firm, which went public through a reverse merger.
The Global EV Battery Cell Market can be segmented into following categories for further analysis.
Battery packs are not exclusive to these already found in consumer technology including such laptop phones and computers. Consumers must manage considerable strength (up to a hundred kW) and high energy capacity (up to tens of kWh) while occupying a limited amount of space and mass and at a low cost.
Substantial investigation and financing have been made in sophisticated lithium batteries suitable for EVs across the entire globe. The key element in the EV grid implementation issues covered in the literature is the energy storage system from the inside of the EVs.
Cell technology has been focusing on the implanting of better polarised store energy capacitance in the market. Energy is stored in a polarised solvent between being an electrode and a reference electrode in energy storage devices.
As that of the contact area of a fluid increases, so does its capacity of the battery. Ultracapacitors can also provide extra power to automobiles throughout kinetic energy and hill climbing, as well as assist in the recovery of braking power generation.
Since it helps electrical and chemical battery packs level power demand, it may also be helpful as a supplementary energy conversion device in powered mobility.
With both the specific structure of nanoparticles combined with anti-oxidation analytes, the output power possibility is continuously enlarged, and much more active lithium is unshackled, finally continuously enhancing the power density and realising the cheapest and best effectiveness.
Volkswagen and Bosch have signed a memorandum of understanding to investigate the formation of a European battery equipment solution supplier.
The two companies seek to provide battery cell and system makers with integrated battery production solutions as well as on-site ramp-up and maintenance assistance.
In the industrialization of battery technology and the bulk manufacture of sustainable, cutting-edge batteries, the firms are aiming for cost and technology leadership.
This will also be a step toward the goal of carbon-neutral mobility, thanks to the "local for local" production method. The Volkswagen Group wants to develop six cell plants in Europe alone.
This partnership is a step forward for both partners in their quest to become leaders in the field of e-mobility. The collaboration will draw on a variety of resources.
With growing worries about the environmental consequences of standard automobiles, governments throughout the world are supporting the use of vehicles that run on alternative energy sources.
EVs are negligible cars that are becoming popular for sustainable public transportation in several nations. To stimulate the adoption of Electric vehicles, some national governments provide monetary incentives like as tax deductions and refunds, subsidies, reduced parking/toll rates for EVs, and free charging. As a result, the global demand for EV batteries is increasing at a rapid rate.
Samsung SDI is involved in development of specialised prismatic cells for electric vehicle battery packs. Samsung SDI has created a comprehensive rechargeable battery architecture portfolio and is competent of mass-producing a wide range of sophisticated automobile rechargeable batteries.
Inside the industry, it has created variable compositions needs, among which Hi Cap changeable is of considerable value. It is intended for low-voltage systems that require rapid charging and draining.
The Hi Cap changeable integrates electrochemical capacitors technology with lithium - ion rechargeable technology.
CATL is also a global leader in the development of the cell technology required for battery packs. It has been developing the ground-breaking and market-oriented technology of multi part integration in the market.
The CTP (cell to pack) innovation, essentially streamlines the modular architecture, increases the volume utilisation rate of a rechargeable battery by 20â30%, decreases the number of components in a rechargeable battery by 40%, and increases efficiency of production by 50%.
Cell to chassis (CTC) innovation combines the rechargeable battery with the vehicle body, chassis, electric drive, heat dissipation, and other different voltage management components, allowing for a driving range of over 1,000 kilometres. It also optimises energy distribution and minimises thermodynamic efficiency to around 12 kWh per 100 km.
Sl no | Topic |
1 | Market Segmentation |
2 | Scope of the report |
3 | Abbreviations |
4 | Research Methodology |
5 | Executive Summary |
6 | Introduction |
7 | Insights from Industry stakeholders |
8 | Cost breakdown of Product by sub-components and average profit margin |
9 | Disruptive innovation in the Industry |
10 | Technology trends in the Industry |
11 | Consumer trends in the industry |
12 | Recent Production Milestones |
13 | Component Manufacturing in US, EU and China |
14 | COVID-19 impact on overall market |
15 | COVID-19 impact on Production of components |
16 | COVID-19 impact on Point of sale |
17 | Market Segmentation, Dynamics and Forecast by Geography, 2024-2030 |
18 | Market Segmentation, Dynamics and Forecast by Product Type, 2024-2030 |
19 | Market Segmentation, Dynamics and Forecast by Application, 2024-2030 |
20 | Market Segmentation, Dynamics and Forecast by End use, 2024-2030 |
21 | Product installation rate by OEM, 2023 |
22 | Incline/Decline in Average B-2-B selling price in past 5 years |
23 | Competition from substitute products |
24 | Gross margin and average profitability of suppliers |
25 | New product development in past 12 months |
26 | M&A in past 12 months |
27 | Growth strategy of leading players |
28 | Market share of vendors, 2023 |
29 | Company Profiles |
30 | Unmet needs and opportunity for new suppliers |
31 | Conclusion |
32 | Appendix |