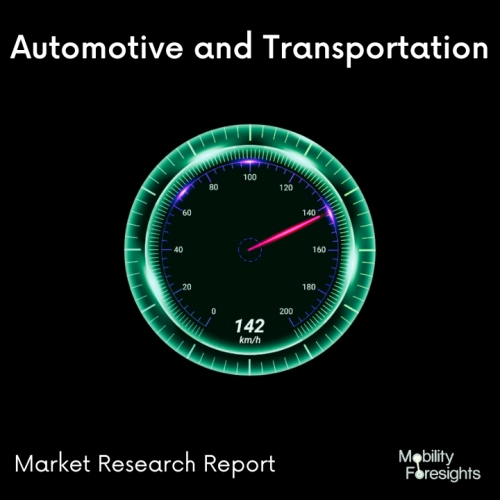
- Get in Touch with Us
Last Updated: Apr 25, 2025 | Study Period: 2024-2030
Subsystem design, material innovation, and vehicle integration are all flourishing in EV battery enclosures. The structures that enclose and safeguard EV battery cells and the hardware that supports them in terms of electrical and thermal management are among the top subsystem priorities in the industry, regardless of whether people refer to them as packs, boxes, or trays. There are several configurations required to integrate the EV battery with the platform it is mounted on.
A design known as "cell-to-pack" eliminates the intermediate module stage and inserts the cells right into the pack. This design is currently being produced by BYD. The battery cell, the vehicle chassis, the electric powertrain, and thermal management are all integrated via cell-to-chassis technology. There is no need for a separate pack because the vehicle's body is entirely made of white.
S No | Overview of Development | Development Detailing | Region of Development | Possible Future Outcomes |
1 | Novelis Introduces Second-Generation Aluminium Intensive Battery Enclosure Solution for Electric Vehicles | Novelis Inc., the world leader in aluminium rolling and recycling, announced today the introduction of new design innovations with Generation II of its lightweight electric vehicle (EV) battery enclosure solution for the rapidly growing EV market. | Global Scale | This would enhance better Technologies and production |
Sr. No. | Timeline | Company | Updates |
1 | January 2022 | Schneider Electric | Schneider Electric acquired start-up climate-tech platform Zeigo to enhance the companyâs digital capabilities in energy, sustainability, and environmental commodity consulting. The acquisition complemented Schneider Electricâs portfolio of clean energy services and solutions and advance the companyâs digital energy transformation ambitions. |
2 | July 2021 | Grevol | Grevol partnered with Contemporary Amperex Technology Co. Ltd. (CATL) for long-term cell procurement. The company will be using CATL cells for their upcoming cargo 3-wheeler (L5N) vehicles. |
3 | April 2021 | ABB | Hitachi ABB Power Grids formed Americas battery storage partnership with Atlas Renewable Energy. It supplied and integrated a 30MW BESS for the Energy Storage for Commercial Renewable Integration (ESCRI) project in South Australia. |
4 | March 2021 | Rittal and Stulz | Rittal and Stulz entered into a global partnership, with immediate effect. As a result, the two companies will be better equipped to offer customers end-to-end, tailored solutions to their needs. Rittalâs broad IT infrastructure portfolio will now be combined with liquid-based closed-circuit chillers, free-cooling products, side chillers and indoor chillers from Stulz. |
5 | February 2020 | Rittal and ZutaCore | Rittal and ZutaCore announced a strategic partnership to offer highly efficient data center cooling solutions and will enable customers to cool processors up to and above 900W. |
Strictly regulated lead emission regulations in electric vehicle batteries, but on the other hand, may stymie industry expansion. Furthermore, high import tariffs on Battery systems and price volatility in raw materials are projected to impede the expansion of the electric vehicle battery industry. Furthermore, the advancement of Lithium-ion technology in EV batteries and the expansion of battery enclosures provide profitable potential for the industry.
The safety of the vehicle is significantly dependent on the safety of the battery pack, which is based on mechanical properties such as the capacity to resist deformation and vibration shocks. Furthermore, a lighter vehicle is preferable since it can extend the range of the vehicle and the life cycle of the rechargeable battery.
Europeans have been expected to lead the worldwide battery enclosures market due to the region's huge installed base of renewable energy and electric cars. Increased environmental protections are also expected to enhance demand for batteries in power storage applications.Given the industry's growth, Asia Pacific is expected to be a particularly appealing location. Increased investment inside the renewables industry is expected to increase demand for batteries in energy storage systems.
Asia Pacific countries such as China, Japan, and India are transitioning to powered mobility in order to bring down pollutant concentrations. The expanding demand for zero-emission cars, the advancement of lithium-ion technology, and rising government rules on emission control systems are all key factors influencing the rise of enclosure requirements.
S No | Company Name | Development |
---|---|---|
1 | Linamar Corp | Three battery enclosure manufacturing facilities were acquired by Linamar Corp. from Dura-Shiloh. The new facilities will be organised as a part of a new Linamar Structures Operating Group by the Ontario-based maker of different industrial and transportation-related parts and systems. High strength steel and composite material designs with precise bonding are used in the battery enclosure business of the erstwhile Dura Shiloh. |
2 | UL Solution | Torch and Grit (TaG), a new test method for the material screening of electric vehicle (EV) battery enclosures, has been launched by UL Solutions, a world authority on applied safety science. Electric vehicle safety is greatly influenced by battery enclosures and the material used to construct them. The TaG test method includes small-scale testing that aids in the prediction of material performance in a thermal runaway event. EV batteries frequently encircle a car's entire base. The materials utilised to house these batteries must be able to endure thermal runaway stresses. |
3 | In order to provide battery enclosures for the brand-new Chevrolet Silverado EV, Magna revealed that it has won new business from General Motors (GM). | In addition to making the battery enclosure for the GMC HUMMER EV at its Magna Electric Vehicle Structures factory, the business will also manufacture the enclosures there. Magna also has intriguing new growth potential outside of the engine as the trend towards electrification of vehicles picks up speed. Battery enclosures are a product for which they see significant future potential and have been able to make use of their experience to supply them. |
They are thrilled to complete this transaction, which will strengthen their expanding Structures and Chassis business portfolio and mark another step in Linamar's shift to a "electrified mobility" world. Electric car batteries are often housed in metal or plastic enclosures that shield them from outside influence. They may also act as insulators or as a component of a battery cooling system.
In order to rank materials for battery enclosures, TaG simulates high temperatures and mechanical impact stresses in a battery thermal runaway event.Original equipment manufacturers (OEM) are progressively switching to plastics and composites for battery enclosure materials as the car industry seeks to lighten the weight of many components. In order to keep costs down and prevent any safety issues, OEMs must select the right enclosure material before developing an expensive prototype.
They are thrilled to be a key component of GM's next line of electric trucks. All battery electric vehicles need battery enclosures, which are where the high-voltage batteries, electrical parts, sensors, and connectors are kept.
Critical battery components are shielded from potential impact, heat, and water infiltration by these elements, which also help the vehicle's chassis to be structurally sound and safe. Magna can create these sophisticated assemblies in steel, aluminium, and multi-material configurations, including lightweight composites, to suit the specific requirements of its clients.
The trends reflect the ongoing evolution of the EV battery enclosure market, driven by technological advancements, sustainability goals, regulatory changes, and the expanding adoption of electric vehicles.
The Current Sensor Module (CSM) and the Battery Impact Detection (BID) system are two new sensors from Continental that are being introduced for electric vehicles. Both of the new technologies put a strong emphasis on maintaining battery parameters or safeguarding the battery. This year will see the introduction of the high-voltage Current Sensor Module (CSM), which simultaneously measures current and monitors temperature. A lightweight substitute for bulky underfloor "armoring" against damage is the Battery Impact Detection (BID) system.
Given that the battery is the most expensive component in an electric vehicle, the CSM was created to safeguard it from overcurrents as well as to maintain the battery's specifications by reducing ageing effects. The two critical pieces of information for battery protection and accurate driving range monitoring will be provided by the CSM, which can be included either in the battery disconnect unit or in the battery itself.
The CSM is a two-channel sensor that integrates shunt and hall technologies into a small, single instrument to measure current independently in order to fulfil stringent functional safety standards. When a stop at a garage is required as a result of underfloor impacts, the BID in conjunction with a lightweight structure warns the driver.
This spares the driver the difficult choice of determining whether a high-speed hit or a low-speed ground contact may have harmed the battery. The BID solution can save up to 50% of the weight of standard metal underfloor protection.
Sr. No. | Timeline | Company | Updates |
1 | December 2021 | Eaton | Eaton received a $4.9 million award from the U.S. Department of Energy (DOE) to reduce the cost and complexity of deploying direct-current (DC) fast electric vehicle charging infrastructure (EVCI). |
2 | October 2021 | Novelis Inc. | Novelis Inc. announced the introduction of new design innovations with Generation II of its lightweight electric vehicle (EV) battery enclosure solution for the rapidly growing EV market. |
3 | July 2021 | Grevol | Green Evolve Private Ltd. (Grevol) announced the launch of their cutting-edge lithium battery packs created for their own soon to be launched 3-wheeler (L5N category) light commercial vehicles. |
4 | May 2019 | Novelis Inc. | Novelis Inc. developed the first aluminum sheet battery enclosure solution to address customers' needs in the rapidly growing electric vehicle and battery markets. Available globally, this design for next-generation automobiles provides a more sustainable mobility solution in battery electric vehicles. |
The rechargeable batteries enclosure is important in collision electricity consumption because it prevents incursion into the rechargeable batteries while also absorbing energy to protect the occupants. The primary role of the internal framework is to minimize penetration into the cells, even though it results in metallic breakage. This exterior reinforcing is meant to collapse in a controllable environment without splitting, absorbing the maximum amount of energy.
Constellium's dual-frame concept uses two separate sophisticated extrusion technologies.Considering the low mass as well as recycled content, aluminium casings perform poorly when thermal runaway occurs, or a vehicle catches fire.
Aluminium seems to have a very high thermal conductivity and a melting temperature of 630 degrees Celsius. A battery fire can reach 1200°C or even more, as well as the aluminium housing will only endure a minimal lifespan eventually melting. As a result, again for a protective surface, a thicker steel sheet or a fire-retardant-loaded polymeric moulding will last longer and offer customers greater time to leave.
Heat created either by lithium batteries can also be an issue for aluminium casings, particularly for portions in direct contact with the cells or other parts of the high-voltage system that become hot while recharging or discharge. The secondary mass and cost reductions associated with being able to shrink the batteries and engine provide compensation for the higher cost of aluminium constructions.
Sr. No. | Timeline | Company | Sales |
1 | Q3-2021 | Eaton | Eatonâs sales in the third quarter of 2021 were $4.9 billion, up 9% from the third quarter of 2020 driven by strong operational performance despite supply constraints that impacted its organic sales growth while the operating cash flow in the third quarter of 2021 was $471 million. |
2 | Q3-2021 | Schindler Electric | Schindler Electricâs Q3 revenues were â¬7,221 million ($ 8.26 B), a growth of 11.8 percent from last year on a reported basis, and 8.8 percent organically. |
3 | Q3-2021 | Pentair plc | Pentair plc announced third quarter 2021 sales of $969 million. Sales were up 21 percent compared to sales for the same period last year. The operating income was $167 million, up 31 percent compared to operating income for the third quarter of 2020, and return on sales (âROSâ) was 17.3 percent, an increase of 130 basis points when compared to the third quarter of 2020 |
4 | Q3-2021 | Novelis Inc. | Novelis Inc.âs net income from continuing operations of $195 million, up 64 percent and 82 percent, respectively, versus the prior year. Adjusted EBITDA increased 46 percent to $501 million in the third quarter of fiscal 2021 compared to $343 million in the prior year period. |
Demand for battery enclosures has been expanding globally as a result of increased development of electrical cars and increased spending on infrastructure. Among the most important components of off-grid systems is the rechargeable batteries compartment. These enclosures protect batteries from harsh environmental conditions as well as other potentially damaging consequences. They also aid in regulating body temperature.
Battery enclosures components safeguard the batteries in electric and hybrid cars from puncture or infiltration, safeguarding occupants, bystanders, and the surroundings against potentially dangerous circumstances.
Novelis is one of the developers of the latest designs and integrations of the battery enclosures in the market. These same compartments are indeed being created with the intention of broadening the crate of aluminium alternatives available for worldwide high-volume EV manufacturing.
The Second-Generation of sophisticated aluminium sheet strenuous architecture minimises weight, reduces costs, and delivers higher pack energy density compared to traditional EV battery enclosures made from steel or aluminium mouldings. The innovative EV battery enclosures are 50 percent lighter than high strength steel containers attributable to the Novelis Advanz s650 alloy in roll-formed frame parts.
Improved cell-to-pack (CTP) package efficiency and structural performance results inside a 30% increase in the energy densities over the baseline. Technological advancements, along with Novelis' excellent material technology, result in a best-in-class frame mass efficiency of less than 1.0 kg/Kwh as well as a weight reduction enhancement of more than 20% over the foundation aluminium reference.
Constellium is also a leading developer focusing on the development of the battery enclosures strengthening the operability of all classes of vehicles in the industrial focus. Electric trucks will need very huge batteries, a high tonnage, plus low energy usage (operating costs). When contrasted to similar design considerations, aluminium battery enclosures or other platform sections often deliver a weight reduction of 40%. The most often used and best-suited alloys for battery enclosures are of the 6000-series Al-Si-Mg-Cu family, which is extremely well acceptable with end-of-life reprocessing.
The latest configuration option for underside panels is a high-strength 6111 alloy in peak aged temper, which saves 30% of the weight of the benchmarking 5754 O-temper composition. Constellium is working on 4xxx alloys with either an E-modulus of 80 GPa and a maximum stress of 350 MPa.
With the experimental 4xxx alloy, a reduced weight of 40% is technologically conceivable. A 7075 T6 alloy is also being developed, with a fracture toughness of 500 MPa as well as an E-modulus of 70 GPa. He highlighted that 7000-series Al-Zn-Mg-Cu alloys have not yet been commonly employed in automotive applications. 7000 might be used for bottom plates where impact resistance is important.
1. Africa â Africa is a region rich in raw materials, and supplies the raw materials mainly for batteries in the electric vehicle industry. It is also key in supplying copper, neodymium and graphite which are crucial for the EV industry.
2. Europe â Europe is a major market for the sales of electric vehicles and a major manufacturing region for EVs and components. The region is also rich in hardware and software development talent for the electric vehicle industry thereby playing a big role in technological innovation. The region has upcoming foundries for semi-conductors and battery plants which will decrease the reliance of the region on Asia mainly China. Regulations are a major driving factor for the electric vehicle industry in this region.
3. Asia â Asia is currently the largest market for the sales of electric vehicles as well as the largest hub for the manufacturing for EVs and components, currently with a monopoly in semiconductor manufacturing. Due to high localization in this region, there is immense hardware and software talent pool and innovation present in the region. The region also has hardware manufacturing with dominance in various finished materials such as steel and aluminium which are exported to Europe and North America.
4. North America â North America is a large market for electric vehicles and a ground for technological innovation. There are various component manufacturing grounds, as well as upcoming battery plants and semiconductor manufacturing that will enable North America to improve its EV market. Efforts are underway to develop a more localized supply chain including localized manufacturing and increasing recycling.
5. Latin America and ROW - Chile and Argentina, are key suppliers of lithium, a crucial component for EV batteries. Latin America has reserves of copper and other essential materials for EVs. Currently, it is a small market for EVs but manufacturing of EVs is expected to increase in this region.
The Global EV Battery Enclosure Market can be segmented into following categories for further analysis.
Sl no | Topic |
1 | Market Segmentation |
2 | Scope |
3 | Research Methodology |
4 | Executive Summary |
5 | Introduction |
6 | Global EV Battery Enclosure Manufacturers Footprint- 2023 |
7 | Global EV Battery Market Overview |
8 | Potential Opportunities For Client |
9 | Average B-2-B Price Of EV Battery Enclosure, By Region |
10 | Average Cost Of EV Battery Enclosure Material |
11 | New Product Development In EV Battery Enclosure Market |
12 | Platforms Of Top OEMs And Battery Enclosure Suppliers For Each Platform |
13 | EV Product Plan Of OEMs (Top 10 OEMs) -2024-2030 |
14 | Rise In Average Battery Capacity And Impact On EV Battery Enclosure Market |
15 | Upcoming Battery Chemistry For Passenger & Commercial Vehicles And Impact On Battery Enclosure Market |
16 | Market Size, Dynamics And Forecast By Enclosure Type, 2024-2030 |
17 | Market Size, Dynamics And Forecast By Vehicle Type, 2024-2030 |
18 | Market Size, Dynamics And Forecast By Battery Pack Size, 2024-2030 |
19 | Market Size, Dynamics And Forecast By Geography, 2024-2030 |
20 | Competitive Landscape |
21 | Market Share Of Major Players-2023 |
22 | OE-Supplier Alignment |
23 | Profitability Analysis Of Major Players |
24 | New Investments & Growth Strategies Of Major Companies |
25 | M&A Activity In Past 5 Years |
26 | Company Profiles |
27 | Unmet Needs And Opportunities For New Players In EV Battery Enclosure Market |
28 | Conclusion |