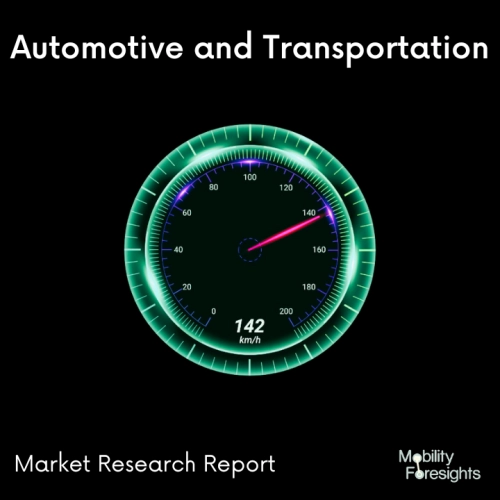
- Get in Touch with Us
Last Updated: Apr 25, 2025 | Study Period: 2024-2030
As automakers commit to electrifying significant segments of their fleets, the manufacturing of electric vehicle (EV) batteries will increase over the next years, and plastics are anticipated to play an increasingly important role in that production. In an EV, the battery enclosure is in charge of offering crash-safe battery protection from electric shock and fire risks. The increasing trend toward reducing vehicle weight by adopting lightweight materials is largely responsible for the growth of the global market for battery housing for electric vehicles.
The primary function of the EV battery housing is to protect the battery pack from external damage, such as impacts, vibrations, and harsh environmental conditions. It must be able to withstand extreme temperatures, moisture, and debris to ensure the integrity of the battery cells and prevent potential hazards.
Plastic EV battery housings are typically made from a variety of high-performance plastics, each offering unique properties that meet the specific requirements of EV battery applications. Here are some of the most commonly used plastics for EV battery housings: Polyamide, Polycarbonate, Polybutylene terephthalate, Thermoplastic polyurethane, Polyphenylene sulfide, and Polyaryletherketone.
Plastic battery housings offer several advantages over traditional metal housings for electric vehicles (EVs), making them an increasingly popular choice in the automotive industry. Here are some of the key benefits of using plastic battery housings:
Multilayer plastics are gaining traction due to their ability to combine the properties of different materials, offering enhanced flame retardancy, chemical resistance, and mechanical strength. The incorporation of sensors and electronics into EV battery housings is increasing the demand for plastics that can withstand electromagnetic interference (EMI) and provide electrical insulation.
The growing emphasis on sustainability is driving the adoption of bio-based plastics, such as polylactic acid (PLA) and bio-based polyethylene terephthalate (PET), which offer reduced environmental impact.
The trend towards smaller and lighter EVs is driving the need for thinner and more compact battery housings, requiring high-performance plastics that can maintain strength and durability without compromising size or weight. The automotive industry is continuously seeking lightweight and high-performance plastics to reduce the weight of EV battery housings, improving vehicle range and energy efficiency.
Battery housing plastics are not just about functionality; they also contribute to the overall aesthetics and user experience of EVs. Manufacturers are paying attention to design elements and surface finishes to enhance the appearance and appeal of battery housings. Significant investments are being made in research and development for battery housing plastics. This includes exploring new materials, enhancing existing plastics, and developing innovative manufacturing techniques to meet the demands of the future EV industry.
Public awareness and education about the importance of sustainable and high-performance battery housing plastics are growing. This is driving consumer demand for eco-friendly and durable EV battery housings, influencing manufacturer decisions.
The global EV Battery Housing Plastic market accounted for $XX Billion in 2023 and is anticipated to reach $XX Billion by 2030, registering a CAGR of XX% from 2024 to 2030.
The SCALEbat scalable battery housing aids new businesses and automakers in creating adaptable electric vehicle platforms. The EDAG Group used the scalable floor assembly that was already being successfully marketed under the name SCALEbase as the foundation for the creation of this concept. Not only is SCALEbaseâs scalability a standout feature; it is also the best method for structurally integrating diverse battery systems.
Depending on regional preferences and the size of the vehicle, automakers and startups can define and approximately design the various power levels for the eDrive and battery module with us. During development, the crash requirements for various markets were taken into consideration.
The extensive usage of steel roll-formed profiles for the battery housingâs structural structure has a huge potential for savings, especially when working with large numbers.
Makrolon CHARGE 2408: A high-impact polycarbonate resin specifically designed for EV battery housings. It offers excellent impact resistance, chemical resistance, and flame retardancy.
Bayblend FR20: A blend of polycarbonate and acrylonitrile butadiene styrene (ABS) with enhanced flame retardancy. It is suitable for EV battery housings that require exceptional fire protection.
Ultramid B3EG7: A polyamide (PA) resin with enhanced glass fiber reinforcement. It is suitable for EV battery housings that require high strength, impact resistance, and thermal stability.
Valox FR: A polyphenylene sulfide (PPS) resin with exceptional heat resistance, chemical resistance, and flame retardancy. It is suitable for EV battery housings that operate in extreme conditions.
Xenoy HPF: A polycarbonate (PC) resin with enhanced high-flow properties. It is suitable for EV battery housings that require thin walls and complex geometries.
Sl no | Topic |
1 | Market Segmentation |
2 | Research Methodology |
3 | Executive summary |
4 | Avg B2B Price Of EV Battery Housing Plastic, By Region |
5 | Key Predictions For Global EV Battery Housing Plastic Market |
6 | Major Drivers For EV Battery Housing Plastic Market |
7 | Global EV Battery Housing Plastic Production Footprint |
8 | Challenges In EV Battery Housing Plastic Market |
9 | Trends In EV Battery Housing Plastic Market |
10 | New Product Development In EV Battery Housing Plastic Market |
11 | Increasing EV sales and Its Impact on EV Battery Housing Plastic Market |
12 | OEM Stance on EVs and Its Impact on EV Battery Housing Plastic Market |
13 | Renewable Energy Projects and Its Impact on EV Battery Housing Plastic Market, By Region |
14 | Latest Technological Advancement in EV Battery Housing Plastic. |
15 | Research Focus Area in EV Battery Housing Plastic |
16 | Market Size, Dynamics And Forecast By Geography, 2024-2030 |
17 | Market Size, Dynamics And Forecast By Vehicle Type, 2024-2030 |
18 | Market Size, Dynamics And Forecast By Battery Capacity, 2024-2030 |
19 | Competitive Landscape Of EV Battery Housing Plastic Market |
20 | Market Share in the EV Battery Housing Plastic Market |
21 | Recent M&A in the industry |
22 | Growth strategy of Major Suppliers |
23 | Company Profiles |
24 | Conclusion |