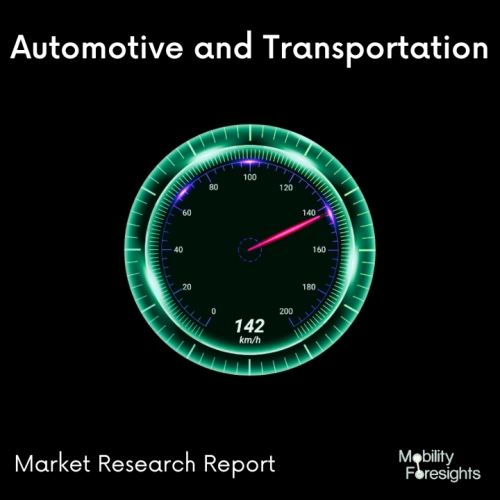
- Get in Touch with Us
Last Updated: Apr 25, 2025 | Study Period: 2024-2030
The issue of battery drain can be completely solved with a battery isolator. The isolator's job is to prevent the primary battery from being drained by other loads in the charging system while still allowing the alternator to help charge it.
An Isolator directs incoming microwave energy using a transversely magnetised ferrite junction. A signal that enters the gadget moves in the direction of the magnetic field's flow. The appropriate port on the gadget receives the signal in this manner. In order to repair or replace a circuit breaker without risk, isolators are typically utilised on both ends of the breaker.
The Global EV Battery Isolator market accounted for $XX Billion in 2023 and is anticipated to reach $XX Billion by 2030, registering a CAGR of XX% from 2024 to 2030.
Vibracoustic develops battery pack isolation systems for large body-on-frame EVs. OEMs are extending the integration of battery electric vehicle (BEV) technology to new vehicle classes and platforms as electrification of the world's fleet of vehicles progresses. Larger vehicles like pick-up trucks and commercial vehicles typically use body-on-frame (body-on-chassis) designs, which presents considerable hurdles when it comes to safe and durable battery pack integration, in contrast to the majority of existing unibody BEVs.
In these larger BEVs, the battery is frequently the most expensive component, therefore safeguarding it against unwelcome loads and vibrations is a crucial NVH goal. The torsional bending stresses within the vehicle chassis are one of the main issues with body-on-frame cars.
While this may have benefits for things like manufacturing efficiency and off-road performance, a firmly mounted battery pack may be exposed to potentially hazardous torsional pressures. A well-engineered isolation system is required for passenger comfort in addition to the safety concerns.
Vibracoustic employs numerous mounts made up of a stamped steel casing, elastomer dampers, and an extruded aluminium core as part of its "whole vehicle" and systems-based approach to NVH performance. Each unit has been built to withstand peak loads between 50 and 60 kN, similar to those brought on by hitting a pothole. The number of attachment points can be increased for larger battery packs to improve NVH performance and battery pack durability. The current design is capable of handling all typical battery packs, which typically weigh 500 to 800 kilogrammes.
For manufacturers wishing to electrify larger, body-on-frame cars, the system is readily available worldwide and has already proven successful in OEM hybrid applications. It comes at a key time, since there is a rising global demand for electric pickup trucks as well as zero-emission SUVs and light commercial vehicles.