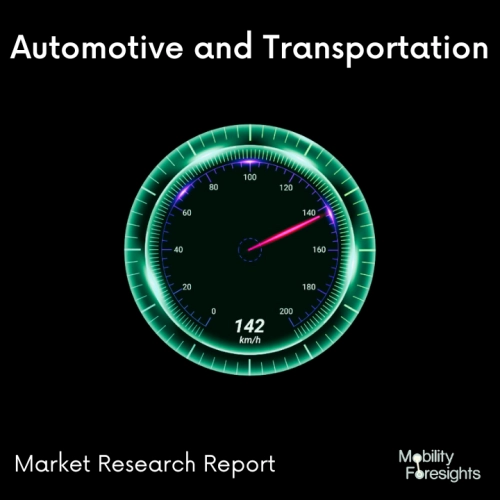
- Get in Touch with Us
Last Updated: Apr 25, 2025 | Study Period: 2024-2030
It consists of an underrun (underbody) protection, a housing cover, and a housing tray with crash structure. Direct long fibre thermoplastic (D-LFT) moulding is a single-stage method that can be used to create the housing components.
LANXESS has Durethan B24CMH2 optimised. The mechanical qualities of components constructed of carbon fibre reinforced plastic (CFRP) and glass fibre reinforced plastic (GFRP), such as high rigidity and strength while being lightweight, are exceptional.
When compared to aluminium or steel, a battery box made of CFRP can reduce weight by up to 40%. The battery cases are mostly made of a Ni-Fe alloy that has been "contaminated" by the electrolyte, glues, and other pollutants that have clung to the surface of the case.
The Global EV battery large-format plastic housings market accounted for $XX Billion in 2023 and is anticipated to reach $XX Billion by 2030, registering a CAGR of XX% from 2024 to 2030.
In an effort to determine whether technical thermoplastics can be used in the design and production of electric car battery housings, LANXESS and Kautex Textron GmbH & Co. KG have been working together. A near-series technology demonstration has been created.
The system is a huge, technically complex, all-plastic housing portion with dimensions of around 1,400 mm in length and width and a weight of about 20 kilograms.
The project's objective was to show how thermoplastics are superior to metals in terms of reduced weight and cost, functional integration, and electrical insulating behaviour.
In order to demonstrate that they can manufacture these very massive components on a commercial scale, they have completely abandoned the usage of metallic reinforcement structures.
Kautex and LANXESS intend to embark into development projects for series manufacturing with automakers using the outcomes of their collaboration in the future.
The battery housing of a C-segment electric vehicle served as the foundation for the demonstrator's development. It is made up of an underrun protection, a housing cover, and a housing tray with a crash structure.
A single-stage Direct Long Fiber Thermoplastic (D-LFT) moulding procedure can be used to create the housing components. Durethan B24CMH2.0, the material for the D-LFT moulding compound, has been optimised by LANXESS.
Glass fibre rovings are used by Kautex Textron to compound the PA6 for the procedure. Continuous fibre-reinforced thermoplastic composites of the Tepex Dynalite brand from LANXESS are used to locally reinforce the house structure.
Sl no | Topic |
1 | Market Segmentation |
2 | Scope of the report |
3 | Abbreviations |
4 | Research Methodology |
5 | Executive Summary |
6 | Introduction |
7 | Insights from Industry stakeholders |
8 | Cost breakdown of Product by sub-components and average profit margin |
9 | Disruptive innovation in the Industry |
10 | Technology trends in the Industry |
11 | Consumer trends in the industry |
12 | Recent Production Milestones |
13 | Component Manufacturing in US, EU and China |
14 | COVID-19 impact on overall market |
15 | COVID-19 impact on Production of components |
16 | COVID-19 impact on Point of sale |
17 | Market Segmentation, Dynamics and Forecast by Geography, 2024-2030 |
18 | Market Segmentation, Dynamics and Forecast by Product Type, 2024-2030 |
19 | Market Segmentation, Dynamics and Forecast by Application, 2024-2030 |
20 | Market Segmentation, Dynamics and Forecast by End use, 2024-2030 |
21 | Product installation rate by OEM, 2023 |
22 | Incline/Decline in Average B-2-B selling price in past 5 years |
23 | Competition from substitute products |
24 | Gross margin and average profitability of suppliers |
25 | New product development in past 12 months |
26 | M&A in past 12 months |
27 | Growth strategy of leading players |
28 | Market share of vendors, 2023 |
29 | Company Profiles |
30 | Unmet needs and opportunity for new suppliers |
31 | Conclusion |
32 | Appendix |