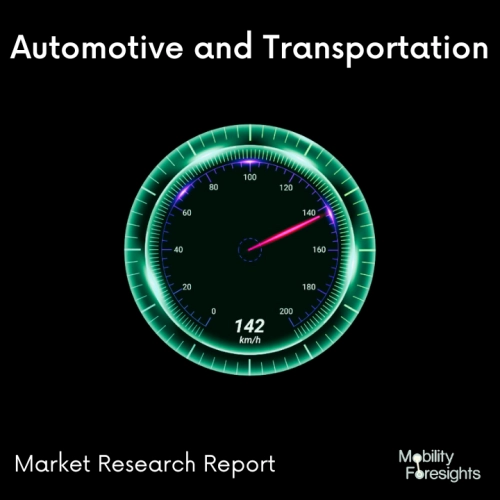
- Get in Touch with Us
Last Updated: Apr 25, 2025 | Study Period: 2024-2030
Laser welding is the best approach for battery pack applications since it is a non-contact process that allows for high-speed operations, the execution of custom weld patterns, and the welding of any joint geometry while joining dissimilar metals.
Lasers have a tiny focal point diameter and a high energy density. Laser welding melts thin or thick metal contacts by utilizing the heat from a high-power concentrated laser beam. Laser welding is used in a variety of industries, including automotive, aerospace, and electronics. However, it is becoming increasingly popular in the EV battery manufacturing industry
Electric vehicle (EV) battery laser welding is a process of using a laser beam to join the various components of an EV battery cell together, including the case, electrodes, and tabs. Laser welding is a fast, efficient, and non-contact process that produces high-quality welds
Laser welding is used to weld the various parts of the battery case together. This includes welding the top and bottom covers to the sides of the case, as well as welding the terminals to the case. Laser welding is a key technology in the manufacturing of EV batteries. It is a fast, efficient, and precise process that produces high-quality welds. This makes it an ideal choice for welding the various components of an EV battery cell together.
Despite the challenges, the benefits of EV battery laser welding outweigh the costs. Laser welding is a fast, efficient, and precise process that produces high-quality welds. This makes it an ideal choice for welding the various components of an EV battery cell together. EV battery laser welding is a promising technology with the potential to revolutionize the EV battery manufacturing industry.
The Global EV battery laser welding market accounted for $XX Billion in 2023 and is anticipated to reach $XX Billion by 2030, registering a CAGR of XX% from 2024 to 2030.
Tesla is building a new EV battery factory in Brandenburg, Germany. The factory is expected to start production in 2023 and will have an annual capacity of 50 GWh. Tesla is planning to use laser welding to assemble the EV batteries at the new factory.
SKI, a South Korean battery manufacturer, is building a new EV battery factory in Norway. The factory is expected to start production in 2025 and will have an annual capacity of 12 GWh. SKI is planning to use laser welding to assemble the EV batteries at the new factory.
Carrs Welding and BIC are working together on a new project to develop a new laser welding process for EV batteries. The Soni-Laser project is expected to be completed in 2023.
Northvolt, a Swedish battery manufacturer, is building a new EV battery factory in Skellefteå, Sweden. The factory is expected to start production in 2024 and will have an annual capacity of 60 GWh. Northvolt is planning to use laser welding to assemble the EV batteries at the new factory.
The Asia Pacific region is the largest market for EV battery laser welding, followed by North America and Europe.
German laser technology company Trumpf is investing â¬100 million in laser welding for EV batteries. The investment will be used to develop new laser welding systems and to expand production capacity.
IPG Photonics, a leading supplier of fiber lasers, has been selected to supply laser welding systems for a new EV battery production line in China. The laser welding systems will be used to weld the various components of EV battery cells together.
Amada, a Japanese metalworking machinery manufacturer, is planning to introduce a new laser welding system for EV batteries in early 2024. The new system is designed to weld EV battery cells together at a high speed and with high precision.
The Chinese government is planning to invest in laser welding for EV batteries as part of its efforts to promote the development of the EV industry. The investment will be used to support the development of new laser welding technologies and to promote the adoption of laser welding in the EV battery manufacturing process.
The demand for laser welding systems is increasing from EV battery manufacturers in China and other emerging markets. This is due to the rapid growth of the EV market in these regions. For example, China is now the world's largest EV market, and it is expected to continue to grow rapidly in the coming years.
Brunel University London is working on a new project to develop a new ultrasonic assisted laser welding process for EV batteries. The project is expected to be completed in 2024.
The Fraunhofer Institute for Laser Technology is working on a new project to develop a new laser welding process for solid-state batteries. The project is expected to be completed in 2025.
LG Energy Solution, a South Korean battery manufacturer, is building a new EV battery factory in Arizona, USA. The factory is expected to start production in 2024 and will have an annual capacity of 11 GWh. LG Energy Solution is planning to use laser welding to assemble the EV batteries at the new factory.
The Trumpf TruLaser Cell 8000 is a new laser welding system that is specifically designed for the production of EV batteries. It is a high-speed, high-precision system that can weld a variety of materials, including steel, aluminum, and copper. The system is also equipped with a number of safety features, such as laser protection and fume extraction.
The IPG Photonics YLS-15000-F fiber laser is a new high-power laser that is well-suited for laser welding EV batteries. It produces a powerful and consistent beam that can weld a variety of materials with high precision. The laser is also very energy-efficient, which helps to reduce operating costs.
Amada has developed a new laser welding system that is specifically designed for the production of EV batteries. The system is capable of welding a variety of materials, including steel, aluminum, and copper. It is also very flexible and can be customized to meet the specific needs of different EV battery manufacturers.
The global EV battery laser welding market can be segmented in a number of ways, including:
1 | Market Segmentation |
2 | Scope of the report |
3 | Research Methodology |
4 | Executive Summary |
5 | Potential Opportunities for Client |
6 | Global Ev Battery Laser Welding Market Manufacturing Footprint |
7 | Recent and upcoming EV Platforms |
8 | EV product plan of OEMs (Top 10 OEMs) -2023 |
9 | Rise in average Ev Battery Laser and impact on Global Ev Battery Laser Welding Market |
10 | Breakdown of The BDU By Sub Components |
11 | Over View Of Laser in The Ev Battery Laser |
12 | Global Upcoming Ev Battery Laser Welding Map |
13 | Upcoming Ev Battery Laser Welding By Region |
14 | Market Segmentation, Dynamics And Forecast By Region, 2024-2030 |
15 | Market Segmentation, Dynamics And Forecast By battery Type, 2024-2030 |
16 | Market Segmentation, Dynamics And Forecast By laser type, 2024-2030 |
17 | Market Segmentation, Dynamics And Forecast By End Use Vehicle Type, 2024-2030 |
18 | Growth strategy of leading players |
19 | Recent mergers & acquisition in the Global Ev Battery Laser Welding industry |
20 | List of Ev Battery Laser Welding Suppliers |
21 | Market Share Of Vendors, 2023 |
22 | Automotive Battery Disconnect Unit Products- By Major Companies |
23 | Merges And Acquisitions in the past 5 years |
24 | Unmet Needs And Opportunity For New Suppliers |
25 | Conclusion |