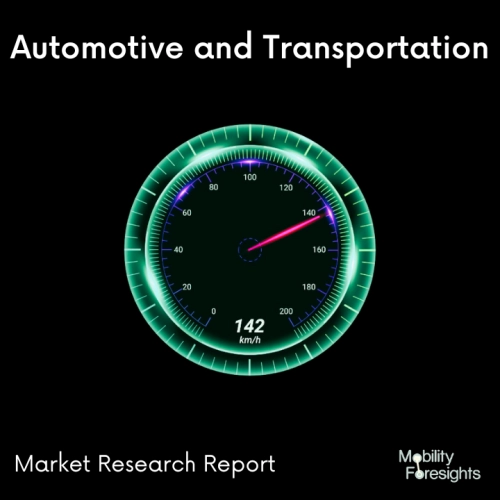
- Get in Touch with Us
Last Updated: Apr 25, 2025 | Study Period: 2024-2030
EV batteries are shielded to prevent battery explosion. The energy density of the battery is being increased through a lot of effort. With the use of shielding, advancements are made to prolong battery life and improve cycle performance. The big batteries generate a significant quantity of heat when they are forced to deliver high power and fuel the vehicle.
The battery could be harmed if this heat is not dispersed. It can result in significant battery wear if not addressed. Hence, there is a decrease in performance and charge efficiency. Moreover, the battery pack's thermal runaway can result in blatant safety risks. Optimising battery life and performance is crucial for efficient heat management. To achieve this, shielding.
The wires that connect the battery and charger to the battery and engine produce a stream of strong current at a low frequency. This in turn generates a strong magnetic field that adversely impacts other parts of the car. To protect the battery and its circuitry from entering EMI, substantial shielding attenuation is necessary.
Very high strength is provided by advanced high strength steels (AHSS). AHSS was created so that automakers could improve the safety capabilities of their automobiles. These slopes have contributed to the structure's weight being continuously reduced. The great formability is maintained in these grades.
They provide an incredibly broad selection of mechanical and technological characteristics for various car pieces, like the body-in-white (BIW).
The Global EV battery protection underbody shielding market accountedfor $XX Billion in 2022 and is anticipated to reach $XX Billion by 2030, registering a CAGR of XX% from 2023 to 2030.
Underbody shielding can be integrated with other vehicle systems, such as aerodynamics or thermal management, to optimize overall performance. For example, some shielding designs incorporate airflow management features to improve cooling of the battery pack, enhancing its efficiency and longevity.
Electric vehicle batteries are expensive and sensitive components. Protecting them from damage caused by road debris, stones, or other external factors is crucial for ensuring their safety and durability. Underbody shielding provides an additional layer of protection to the battery pack, safeguarding it from potential hazards.
Governments and regulatory bodies around the world are implementing stringent safety standards for electric vehicles. These standards often include provisions for battery protection and safety measures. Underbody shielding can help automakers meet these requirements and ensure compliance with safety regulations.
With the increasing number of electric vehicles on the road, there is also a growing aftermarket demand for battery protection solutions. Some companies specialize in developing aftermarket underbody shielding kits that can be retrofitted to existing EV models, providing an opportunity for vehicle owners to enhance their battery safety.
The global demand for electric vehicles has been rising due to environmental concerns and government initiatives promoting sustainable transportation. As the EV market expands, the need for efficient battery protection solutions, including underbody shielding, is also growing.
A multiply divided battery mounting section and an underbody portion are both included in an electric vehicle's underbody that is designed as the lower body of the vehicle. The multi-divided battery mounting component, which makes up part of the underbody, allows for multi-divided and selective attachment of batteries.
Another part of the underbody is formed by the connection between the underbody portion and the battery mounting piece.
The underbody for an electric vehicle that serves as the lower body of an electric vehicle is the subject of the present invention. More specifically, it relates to an underbody for an electric vehicle that not only offers a lighter underbody but also safely maintains its structural rigidity, allows for the selective mounting of multiple separate batteries on it to increase travel distance between battery charges, and
Manufacturers of EV batteries and original equipment manufacturers are working to find more effective ways to produce batteries at scale as the adoption and innovation of EVs picks up speed. Fire protection is also necessary to guarantee that vehicle batteries offer the highest level of protection in the event of accidents and fires.
Therefore, it's crucial to use EV battery safety devices that slow the spread of fire. To meet this problem, Henkel introduced Loctite EA 9400 and Loctite FPC 5060, two new protective coating materials that are intended to cover the battery housings from heat and fire in the event of a thermal runaway incident.
The coatings, when used on battery packs, aid in preventing and delaying the spread of flames. Nonetheless, their effective and affordable application procedures ensure that manufacturers can keep improving battery technology.
Battery safety solutions aid in reducing or delaying such occurrences, extending the window of opportunity for vehicle escape. With the development of regulatory frameworks for EV safety, this time window is becoming more and more regulated. China has already implemented laws that outline the necessary time window, and other markets are anticipated to do the same in due course.
Both Loctite EA 9400 and Loctite FPC 5060 were created for automated mass manufacturing and are compatible with popular automated dispensing systems. They can be applied by "spray" or "flat stream."
Sl. No | Topic |
1 | Market Segmentation |
2 | Research Methodology |
3 | Executive Summary |
4 | Insights from Industry Stakeholders |
5 | Platforms of top OEMs and Battery suppliers for each platform |
6 | EV product plan of OEMs (Top 10 OEMs) -2023-2030 |
7 | OEM Stance on EVs and impact on Battery Underbody Shielding market |
8 | Key Criteria of Underbody Battery Underbody Shield properties for selection by Manufacturers |
9 | Average B2B Price of Battery Underbody Shield, by Region |
10 | Average B2B Price EV Battery Underbody Shield, by OEM |
11 | New Product Launch In EV Battery Shield Market and future implications |
12 | R&D Focus area of Battery Shield Manufacturers |
13 | Patents filed in Battery Shield Manufacturing in the past 10 years |
14 | Decrease in battery price and impact on EV Battery Shield Market |
15 | Developments in Solid state battery and impact on Battery Shield Market |
16 | New materials launched for EV Battery Shield Market |
17 | Pricing trends of EV Battery Shield – 2018 - 2023 |
18 | Top 10 EV Platforms And Annual Value For Battery Shield – 2022-2025 |
19 | Trends is EV Battery Protection Underbody Shielding Market |
20 | Cost breakdown of EV Battery Protection Underbody Shield |
21 | Regulations in EV Battery Protection Underbody Shield |
22 | OEM Testing Requirements in EV Battery Protection Underbody Shield |
23 | Market Size, Dynamics And Forecast By Geography, 2023-2030 |
24 | Market Size, Dynamics And Forecast By Electric Vehicle Type, 2023-2030 |
25 | Market Size, Dynamics And Forecast By Vehicle Type, 2023-2030 |
26 | Market Size, Dynamics And Forecast By Material, 2023-2030 |
27 | Market Size, Dynamics And Forecast By Type, 2023-2030 |
28 | Competitive Landscape of EV Battery Shield Market |
29 | Market share of EV Battery Shield Market-2023 |
30 | OE-Supplier Alignment in EV Battery Shield Market |
31 | Recent M&A in the industry |
32 | Growth strategy of major suppliers |
33 | Company Profiles |