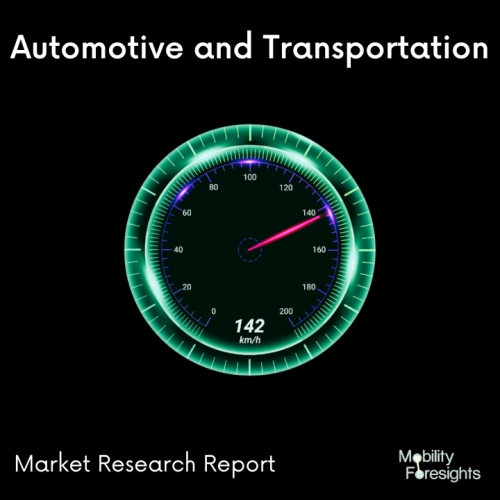
- Get in Touch with Us
Last Updated: Apr 25, 2025 | Study Period: 2024-2030
INTRODUCTION TOEV BATTERY RECYCLING MARKET
EV batteries are thicker and heavier than ordinary automobile battery packs, and they are composed of hundreds of individual lithium-ion cells, all of which must be dismantled.
These contain hazardous ingredients and have a bad habit of exploding if dismantled wrong. Many different materials are recovered as a result of the recycling process.
As a first phase, cathode minerals such as cobalt, nickel, lithium, and manganese are being prioritized. Disassembled batteries system components, including such aluminum and copper, are recycled through established mechanisms.
A variety of novel EV battery recycling methods that are now being developed aim to boost the recovery rate of certain minerals such as cobalt and nickel through the recycling process. These innovations are centered on hydrometallurgical processes, which need less power compared pyrometallurgical procedures.
The latest EV battery recycling innovations pledge to improve recycling and reuse to an estimated 80%. The potential advantages of EV battery recycling are related to prolonging the current battery longevity and lowering the need for raw materials used in the manufacture of replacement EV batteries.
EV battery recycling ensures the availability of minerals such as cobalt, which would be required for the creation of EV batteries.
The technological issue connected with the accessibility of a broad range of battery sizes, topologies, chemistries, and metallurgy, as well as a lack of engineering for straightforward disassembling and regeneration, is shared by both recovery and recycling of EV batteries. That renders typical procedures very difficult at this moment, necessitating specialized approaches.
S No | Overview of Development | Development Detailing | Region of Development | Possible Future Outcomes |
1 | Ford signs deal with Redwood Materials to recycle EV Batteries | Ford is partnering with battery recycling start-up Redwood Materials to reuse the raw materials from EV battery packs. | Global Scale | This would enhance better Technologies and production |
Reuse and recycling are further hampered by a lack of collecting infrastructures to transport stockpiled EV batteries to a centralized location where huge quantities might result in scale economies.
There's still currently no organized collecting network for Battery systems in various nations because the quantities are low and they have been dispersed in tiny numbers at vehicle dealerships, repair shops, and scrap metals shredding plants situated around the nation.
Battery packs are starting to appear in sufficient numbers at salvage yards to raise issues regarding their management via reprocessing.
Assuming concerns of accountability and standards can be handled, EV battery reuse looks to be a feasible business model with high profit margins.
Because of the advantageous finances, it is predicted that EV batteries will indeed be redirected to reuse (storage technology systems, backup generators, EVs and numerous other technologies including such wheelchairs and drones, etc.) for just the conceivable future. The global industry for electric car battery recycling is exploding.
This market has a potential due to a number of things. Among these prospects is an increasing emphasis on decreasing the use of natural resources in battery manufacture. Aside from the use of ecologically responsible battery packs, the emergence and development of the battery supply chain benefits the economies of developing nations and many others.
This market's expansion is hampered by a few constraints. Infrastructure investment is one of these constraints. In addition, lower adoption of electric vehicles due to increased costs contributes to the market's downturn.
ACE Green Recycling (ACE), a green recycling technology business, recently announced intentions to construct and operate four additional lithium-ion battery recycling plants with a total annual capacity of more than 30,000 tonnes.
To encourage the global adoption of lithium-ion batteries, the four locations will tap into previously neglected recycling markets and provide regional markets with an emissions-free, carbon-neutral recycling solution.
The company is currently planning facilities in Thailand, India, and the United States, with anticipated capacity of 10,000 tonnes between India and Thailand and 20,000 tonnes in the United States, according to the company.
With the opening of these four new sites, we will be able to strategically leverage our global supply chain experience to serve markets not just in North America but also in Asia, where we have a strong presence.
The Global EV Battery Recycling Market can be segmented into following categories for further analysis.
EV batteries typically have a lifetime of 8 years or 100,000 miles (or maybe more), and energy guarantees that cover this serviceability are common. In practice, however, it emerges that Battery packs can live considerably longer than anticipated.
Whereas a tiny fraction of EV batteries reach EOL earlier than 8 years due to battery failure or vehicle crashes, this is anticipated to be roughly 1% to 3% of the EV stock. Manufacturing flaws from extraction issues, rising temperatures, improper recharging, electrolytes or separation damage, and long-term, repeated cycling deterioration are all common causes of EV battery problem.
The most conventional technological advancement has been the energy storage systems (ESS), which serve the electricity network in a variety of ways, involving maximum load shaving, load control, backup generators, frequency regulation, and a variety of other uses.
Because ESSs allow electricity generated to be saved for later use, energy storage ensures the sustainability of alternative renewable energy sources like solar and wind.
EV batteries may have been used to build long term storage similar systems to the Tesla Powerwall, which offers backup power throughout rolling blackouts and can store the energy generated by solar installations for subsequent use during the household or to send back into to the electricity network at peak price periods.
There seems to be an incorporated use of pyrometallurgy â which involves burning batteries to eliminate undesired organic compounds and polymers â and hydrometallurgical, which involves soaking lithium-ion batteries in chemicals to breakdown the elements into a solvent.
MG Motor India has recycled its first electric vehicle battery in collaboration with Attero. According to the company, metal extracts and several other commodities from the recycling process can be used to manufacture new batteries.
With this accomplishment, MG Motor India has bolstered its efforts to develop the electric vehicle ecosystem, ultimately making it greener and more sustainable. The move also aligns with MG's #ChangeWhatYouCan campaign, which encourages people to make a positive change in their own life and in the world around them.
Ensuring end-to-end sustainability for electric vehicles is something we are enthusiastic about at MG, stated MG Motor India. Because battery waste is a problem for sustainable mobility, we feel that battery recycling is the best way to fill the gap. We're excited to continue working in this area to develop long-term, end-to-end solutions that will help us make a significant impact.
Taniobis GmbH and Partners announced today that they are working with a Volkswagen-led research team to enhance battery recycling technologies.
The HVBatCycle research consortium intends to maintain a closed material cycle for cathode metals, electrolytes, and graphite.
Only by focusing on sustainability in as many areas as possible will European battery manufacture be successful. For an energy and transportation transformation guided by high environmental and social norms, long-lasting batteries are essential.
Taniobis GmbH, J. Schmalz GmbH, and Viscom AG have been researching and developing the processes required for this for three years under the leadership of the Volkswagen Group, in collaboration with researchers from RWTH Aachen University, TU Braunschweig, and the Fraunhofer Institute for Surface Engineering and Thin Films.
The battery powered renaissance, fueled by the need to reduce carbon emissions private transportation in order to fulfil global objectives for reducing greenhouse gas emissions and improving air quality in cities, is likely to drastically alter the automotive sector.
Whenever these cars come to the end of their lifespan, the resultant package wastes would be roughly 250,000 tonnes and half a million cubic metres of untreated pack waste, based on reasonable estimations of an approximate battery pack weight of 250 kg and dimensions of half a cubic metre.
Despite re-use and existing recycling technologies can remove most of these pollutants from landfill, the accumulated load of electric-vehicle trash is important considering the industry's development of the countries.
Spiers New Technologies is involved in implementation and innovation of latest recycling technologies within the market focusing on better and efficient ecological usage.
SNT has already been currently developing a wrap technology that ends the loop using EV batteries which are being prepped for a rechargeable functionality.
SNT creates ESSs using both original and used battery components and packs. SNT manufactures these reconditioned battery modules, packs, and storage technologies using both new and recovered EV battery cells. Inside the market, it is based on a closed loop vision. All battery packs that have been improved so that they have enough power capacity for their refurbished function. This level is established on a particular circumstance situation by the customer.
Retriev Technologies have been involved in development of the recycling technologies. It is involved in recycling requirements of various battery compositions present in the market. It uses a sophisticated approach of technology to intervene as required and recover the minerals. To retrieve the different components of a lead acid battery, an automated recycling process called as a battery breaker is utilized.
The battery packs are sent to an elevated crusher, which is contained to minimize fugitive lead pollutants from escaping. This same crusher successfully extracts all of the battery components before employing different material separating procedures to provide clean flows of raw resources for use in innovative products.
Furthermore, they have a manual process for physically disassembling the battery components into clean flows of raw resources. This manual line is useful for some consumers who prefer lead plate and over crushed lead generated by the automatic breakers.
Sl no | Topic |
1 | Market Segmentation |
2 | Scope of the report |
3 | Abbreviations |
4 | Research Methodology |
5 | Executive Summary |
6 | Introduction |
7 | Insights from Industry stakeholders |
8 | Cost breakdown of Product by sub-components and average profit margin |
9 | Disruptive innovation in the Industry |
10 | Technology trends in the Industry |
11 | Consumer trends in the industry |
12 | Recent Production Milestones |
13 | Component Manufacturing in US, EU and China |
14 | COVID-19 impact on overall market |
15 | COVID-19 impact on Production of components |
16 | COVID-19 impact on Point of sale |
17 | Market Segmentation, Dynamics and Forecast by Geography, 2024-2030 |
18 | Market Segmentation, Dynamics and Forecast by Product Type, 2024-2030 |
19 | Market Segmentation, Dynamics and Forecast by Application, 2024-2030 |
20 | Market Segmentation, Dynamics and Forecast by End use, 2024-2030 |
21 | Product installation rate by OEM, 2023 |
22 | Incline/Decline in Average B-2-B selling price in past 5 years |
23 | Competition from substitute products |
24 | Gross margin and average profitability of suppliers |
25 | New product development in past 12 months |
26 | M&A in past 12 months |
27 | Growth strategy of leading players |
28 | Market share of vendors, 2023 |
29 | Company Profiles |
30 | Unmet needs and opportunity for new suppliers |
31 | Conclusion |
32 | Appendix |