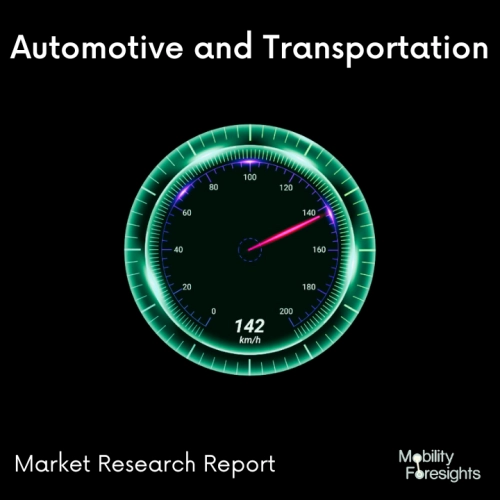
- Get in Touch with Us
Last Updated: Apr 27, 2025 | Study Period: 2024-2030
The optimization of electric car battery functional safety is complicated by cell chemistries, thermal dynamics, vehicle packing, and even weather.Batteries for electric vehicles (EVs) require protection from the elements.
EV battery enclosures, which are often positioned on the underside of the car, protect the cells from water, dust, debris, and other factors. EV battery enclosures, like other enclosures, experience temperature and pressure variations that might cause difficulties if not properly vented.
However, EV batteries provide unique venting issues, including the possibility of severe thermal runaway circumstances. Given these difficulties, integrating design, manufacture, installation, and testing is critical for optimal EV battery venting performance.
A variety of components in an EV require venting. Temperature variations in lighting, horns, electronics, powertrain, and other components are caused by weather, moisture, or heat from electrical circuits. Temperature variations cause pressure changes within the components. Pressure changes can be triggered by variations in altitude.
Expanded polytetrafluoroethylene (e PTFE) membranes have proven useful for venting and pressure equalization in EV enclosures. This material allows gasses to enter and exit the enclosure while also preventing liquid and particle impurities from entering.
Battery packs face unique issues due to their position, size, and chemical makeup, in addition to exposure to the different elements encountered by other automobile components. Packs on the undersides of vehicles may be subjected to water fording or submersion as the vehicle travels through standing water.
Salt and other corrosive substances may be present in road water. Vehicles may be subjected to high-pressure sprays of varied temperatures at car washes. Dust, grime, and vibration may all have an effect on the battery pack.
The size of EV battery packs also poses difficulties. The packs, which may weigh up to 2,000 pounds (907 kg), contain hundreds, if not thousands, of cells with huge air contents that can impose stresses on the enclosures as pressures rise. This needs extensive venting to allow for pressure differences caused by altitude or temperature changes.
Sealing and guarding against water, dust, contaminants, and hard automotive fluids. Continuous pressure equalization to assist safeguard the battery casing from excessive over- or pressure over the battery's life.
Effective ventilation allows moist air that may build inside the battery housing to be evacuated with each warming-up cycle, assisting in the avoidance of potential internal condensation concerns in certain meteorological circumstances. Helps to ensure proper mitigation in the event of a thermal runaway event within the battery, allowing significant volumes of gasses to be released in a short period of time.
Venting systems that are properly constructed provide contamination protection as well as pressure equalization during typical working circumstances, resulting in longer-lasting enclosures and battery life cycles. In the unlikely event of a thermal runaway, the venting system must also be capable of giving fast pressure relief, assisting in the prevention of component failure or the spread of the problem to other cells.
Pressure equalization is the first stage of dual-stage battery venting. The battery pack's permeable e PTFE membrane allows air and other gasses to travel in and out. Due to fluctuations in altitude and temperature, pressure equalization is required during typical vehicle operation.
The Global EV Battery Venting Film Market accounted for $XX Billion in 2023 and is anticipated to reach $XX Billion by 2030, registering a CAGR of XX% from 2024 to 2030.
PROSTECH e PTFE membrane materials come in a variety of widths, thicknesses, and densities, allowing designers to customize their airflow, particle, and liquid ingress protection requirements. These goods, which are made entirely of PTFE resin, may also be sterilized for usage in ultra-clean environments.
GM is carrying out plans to construct annual EV capacity in North America, aided by their U.S. battery cell joint venture sites with capacity, and to expand from there in following years. Annual manufacturing of Chevrolet, Cadillac, GMC, Buick, and Bright Drop automobiles will be supported by the Ultimo CAM joint venture.
Increasing CAM manufacturing capacity and adding p CAM to their joint venture is another key step towards developing a more secure and sustainable supply chain to serve GM's rapidly rising EV production demands, which began with the establishment of battery cell production in the United States.
From there, they worked their way down the battery supply chain, all the way to raw material recovery. They are increasing vertical integration, resulting in increased investment and employment creation.
Batteries for electric vehicles (EVs) require protection from the elements. EV battery enclosures, which are often positioned on the underside of the car, protect the cells from water, dust, debris, and other factors.
EV battery enclosures, like other enclosures, experience temperature and pressure variations that might cause difficulties if not properly vented. However, EV batteries provide unique venting issues, including the possibility of severe thermal runaway circumstances. Given these difficulties, integrating design, manufacture, installation, and testing is critical for optimal EV battery venting performance.
Expanded polytetrafluoroethylene (e PTFE) membranes have proven useful for venting and pressure equalization in EV enclosures. This material allows gasses to enter and exit the enclosure while also preventing liquid and particle impurities from entering.