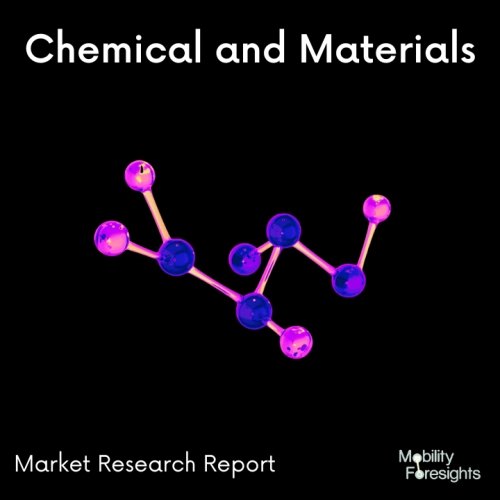
- Get in Touch with Us
Last Updated: Apr 25, 2025 | Study Period: 2023-2030
For the purpose of producing hollow thermoplastic objects, blow moulding is a sort of plastic forming method. A parison or preform, a plastic tube, is heated and inflated during the procedure.
The ancient technique of glass blowing gave rise to plastic blow moulding. A manufacturing method for creating hollow plastic parts is blow moulding (also known as moulding).
Glass bottles and other hollow objects can also be formed using this technique. Polyethylene (High Density, Low Density, and Linear Low Density), Polypropylene, Polyethylene-Terephthalate (PET), and PVC are among the materials used in blow moulding.
The Global EV blow molded plastics market accounted for $XX Billion in 2022 and is anticipated to reach $XX Billion by 2030, registering a CAGR of XX% from 2023 to 2030.
New Integrated Thermal Manifold Assemblies For Electric Vehicles Are Launched By TI Fluid Systems TI Fluid Systems (LSE:TIFS), a top provider of automotive fluid systems technology, has unveiled a cutting-edge method for managing coolant fluid on electric vehicles.
The latest innovation is an Integrated Thermal Manifold Assembly (ITMa), which substitutes many line bundle assemblies of thermal loops for heating and cooling on the next generation of electric vehicles with a single, lightweight, blow-molded plastic manifold to optimise complex line architecture.
Modern electric vehicles often require numerous intricate rubber, metal, or multi-layer plastic lines that are closely packed underneath the hood or mounted to the chassis.
The fuel tank blow moulding technology used by TI Fluid Systems' Fuel Tank and Delivery Systems (FTDS) division can now be improved to create a one-piece integrated thermal "manifold" (ITMa) design.
With its better flow performance for efficiency benefits, lower part count for sub and final vehicle assembly, lighter weight, and cheaper investment tooling costs, this single piece blow moulded plastic manifold provides significant OEM EV value.
The FTDS division of TI Fluid Systems has shown additional integration potential for "fluid storage" (coolant reservoir expansion tank), "fluid temp control" (heat exchangers/sensors), and "fluid delivery" (pumps), for a very compact module solution. This is in addition to the ITMa coolant "fluid carrying" design.
These integrated thermal modular components are extremely tailored to each OEM vehicle or application, much like a fuel delivery module is today, and can be developed for various system types of numerous thermal loops.
Sl no | Topic |
1 | Market Segmentation |
2 | Scope of the report |
3 | Abbreviations |
4 | Research Methodology |
5 | Executive Summary |
6 | Introduction |
7 | Insights from Industry stakeholders |
8 | Cost breakdown of Product by sub-components and average profit margin |
9 | Disruptive innovation in the Industry |
10 | Technology trends in the Industry |
11 | Consumer trends in the industry |
12 | Recent Production Milestones |
13 | Component Manufacturing in US, EU and China |
14 | COVID-19 impact on overall market |
15 | COVID-19 impact on Production of components |
16 | COVID-19 impact on Point of sale |
17 | Market Segmentation, Dynamics and Forecast by Geography, 2023-2030 |
18 | Market Segmentation, Dynamics and Forecast by Product Type, 2023-2030 |
19 | Market Segmentation, Dynamics and Forecast by Application, 2023-2030 |
20 | Market Segmentation, Dynamics and Forecast by End use, 2023-2030 |
21 | Product installation rate by OEM, 2023 |
22 | Incline/Decline in Average B-2-B selling price in past 5 years |
23 | Competition from substitute products |
24 | Gross margin and average profitability of suppliers |
25 | New product development in past 12 months |
26 | M&A in past 12 months |
27 | Growth strategy of leading players |
28 | Market share of vendors, 2023 |
29 | Company Profiles |
30 | Unmet needs and opportunity for new suppliers |
31 | Conclusion |
32 | Appendix |