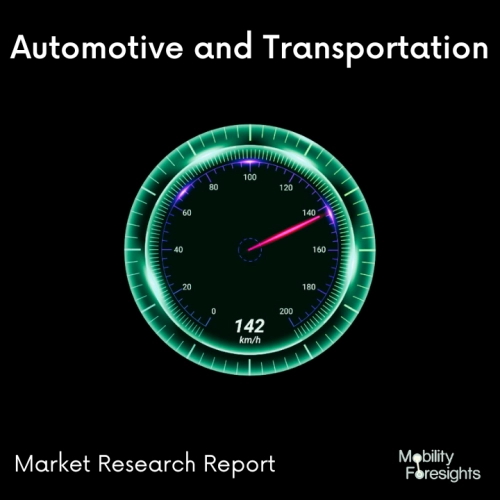
- Get in Touch with Us
Last Updated: Apr 25, 2025 | Study Period: 2023-2030
The thermal range of silicone rubber insulated cables is exceptional; some of them can withstand lows of -90°C and highs of 200°C. Silicone rubber wires are very flexible as well.
The cable that joins the vehicle to an electric charging station is known as an EV connector. One end of the connector, which has a "plug head" on either end, pushes into a port on their electric automobile, while the other end connects into a port on the charging station.
These single or multicore cables can withstand high temperatures. They are utilised in the shipbuilding, aviation, glass, cement, steel, and cement sectors. Flexible single-core cables with tinned copper conductor and silicon insulation are known as SiF and SIFF.
The Global EV cable silicon rubber market accounted for $XX Billion in 2022 and is anticipated to reach $XX Billion by 2030, registering a CAGR of XX% from 2023 to 2030.
The newest DiBO type 1 charging cable assemblies for electric vehicles (EVs) have been released by TE Connectivity (TE), a global pioneer in connectivity and sensors.
The new, improved design, known as DiBO+, incorporates a high flex cable certified for UL62 criteria while keeping the same ergonomic, stylish, low-profile design elements of the previous generation.
The redesigned design features a high flex cable for excellent flex life, maximum durability, and functionality for every movement, and a smaller, more ergonomic handle that makes it simpler to fit security enclosures.
The new DiBO+ EV charging cable assemblies from TE are packed with features and perfect for EV charging stations. The assemblies have a large capacity for mating cycles; testing was completed with 10,000 mating cycles.
The item is UL recognised in accordance with UL 2251 and complies with SAE J1772 requirements. The cable itself is RoHS compliant and complies with UL62's standards for cold impact while preserving flexibility.
Liquid silicon rubber is used to seal the contact assembly, preventing moisture and corrosion from entering the connection body. A crush-resistant connection body is provided by the materials employed, which also meet outdoor classification F1 (UL) requirements and are resistant to typical vehicle fluids.
Sl no | Topic |
1 | Market Segmentation |
2 | Scope of the report |
3 | Abbreviations |
4 | Research Methodology |
5 | Executive Summary |
6 | Introduction |
7 | Insights from Industry stakeholders |
8 | Cost breakdown of Product by sub-components and average profit margin |
9 | Disruptive innovation in the Industry |
10 | Technology trends in the Industry |
11 | Consumer trends in the industry |
12 | Recent Production Milestones |
13 | Component Manufacturing in US, EU and China |
14 | COVID-19 impact on overall market |
15 | COVID-19 impact on Production of components |
16 | COVID-19 impact on Point of sale |
17 | Market Segmentation, Dynamics and Forecast by Geography, 2023-2030 |
18 | Market Segmentation, Dynamics and Forecast by Product Type, 2023-2030 |
19 | Market Segmentation, Dynamics and Forecast by Application, 2023-2030 |
20 | Market Segmentation, Dynamics and Forecast by End use, 2023-2030 |
21 | Product installation rate by OEM, 2023 |
22 | Incline/Decline in Average B-2-B selling price in past 5 years |
23 | Competition from substitute products |
24 | Gross margin and average profitability of suppliers |
25 | New product development in past 12 months |
26 | M&A in past 12 months |
27 | Growth strategy of leading players |
28 | Market share of vendors, 2023 |
29 | Company Profiles |
30 | Unmet needs and opportunity for new suppliers |
31 | Conclusion |
32 | Appendix |