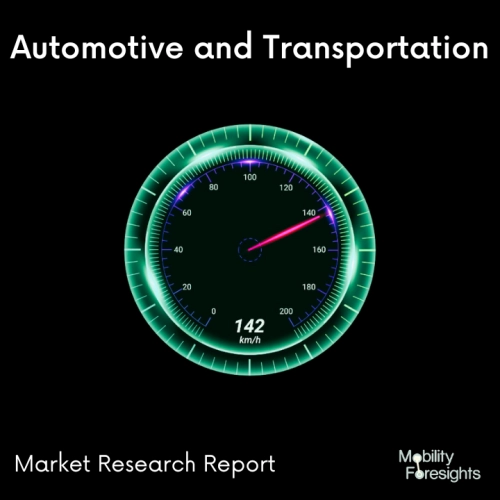
- Get in Touch with Us
Last Updated: Apr 25, 2025 | Study Period: 2024-2030
Electronic circuit board coating is a useful process used in the production of printed circuit boards. It is a valuable and essential step that helps protect the components on the board from corrosion and other environmental factors.
Circuit board coating is typically done with a conformal coating material such as a polymer-based solution. This coating creates a protective barrier that seals the board from contaminants and moisture.
It also helps to protect the board from electrical shorts and oxidation.
The EV circuit board coating process is similar to the traditional method of circuit board coating but with some differences. The main difference is that the EV coating materials have the ability to create an electrical insulating barrier.
This makes them suitable for use in Electric Vehicles, where electrical insulation is a major requirement. Additionally, EV coating materials are also designed to be more heat-resistant to meet the demands of high-temperature vehicles.
EV circuit board coating materials are typically applied with a spray gun, but they can also be applied using a brush. This kind of coating process is used to cover the board in a thin, even layer that also conforms to the board's shape and any changes in direction.
The coating also creates a seal that helps to protect the components from contaminants and dust.
EV circuit board coatings provide several benefits for Electric Vehicles. By providing an electrical insulating barrier, it helps to improve the reliability of electrical components and reduce the risk of electrical shock.
Additionally, the coating also helps protect the components from environmental factors such as corrosion and moisture, resulting in a longer lifespan for the vehicle.
In addition, EV circuit board coatings provide a cost-effective solution for improving the performance of Electric Vehicles and ensuring their safe and reliable use.
The Global EV circuit board coating market accounted for $XX Billion in 2022 and is anticipated to reach $XX Billion by 2030, registering a CAGR of XX% from 2024 to 2030.
Electronic components and printed circuit boards (PCBs) are shielded from corrosion and excessive humidity by Dow's DOWSIL CC-2588 Conformal Coating, a hard, abrasion-resistant silicone-based substance.
Extremely low levels of volatile organic compounds (VOCs) are released by the coating, making it nearly odourless. With CC-2588, it may reduce energy consumption by curing at room temperature, increase throughput by supporting spraying, and use UV light to detect voids in the conformal coating using automated inspection equipment.
In terms of durability, the new DOWSIL substance is similar to existing resin conformal coatings once it has dried. The mechanical strength of DOWSIL CC-2588 is good enough to withstand damage, with a durometer of 76 Shore A.
Additionally, it offers trustworthy adherence without the darkening or delamination that come with polyurethane goods or acrylate conformal coatings. The coating includes five minutes of tack time at room temperature to allow for assembly modifications before definitive bonding takes place.
According to lab testing, this protective coating satisfies the requirements for insulation resistance and dielectric withstanding voltage specified in IPC-CC-830B, Amendment 1.
The dielectric insulation, vibration damping, and moisture protection required in PCB assembly and manufacturing for home appliances and automobile electronics are provided by DOWSIL CC-2588. Conformal coatings from Dow, which are silicone-based, can withstand highly hostile environments and promote environmental sustainability as well as manufacturing productivity.
The MR-COAT-01F and 02F conformal coating series has been introduced by Shin-Etsu Silicones of America, Inc. The line offers superior abrasion resistance and reduced stress on printed circuit board (PCB) components, according to the business, by combining high hardness with exceptionally high elongation.
Wire bonding and other circuitry components in printed wiring board (PWB) systems and applications are subjected to tremendous stress, which can shorten their useful lives.
The hard resin-based, one-component MR-COAT solutions don't require toluene as a solvent, which makes them appropriate for protective coating applications on both flexible and rigid PCB and PWB systems. According to SES, compared to conventional resin-based conformal coatings, the series delivers noticeably better elongation.
Sl no | Topic |
1 | Market Segmentation |
2 | Scope of the report |
3 | Abbreviations |
4 | Research Methodology |
5 | Executive Summary |
6 | Introduction |
7 | Insights from Industry stakeholders |
8 | Cost breakdown of Product by sub-components and average profit margin |
9 | Disruptive innovation in the Industry |
10 | Technology trends in the Industry |
11 | Consumer trends in the industry |
12 | Recent Production Milestones |
13 | Component Manufacturing in US, EU and China |
14 | COVID-19 impact on overall market |
15 | COVID-19 impact on Production of components |
16 | COVID-19 impact on Point of sale |
17 | Market Segmentation, Dynamics and Forecast by Geography, 2024-2030 |
18 | Market Segmentation, Dynamics and Forecast by Product Type, 2024-2030 |
19 | Market Segmentation, Dynamics and Forecast by Application, 2024-2030 |
20 | Market Segmentation, Dynamics and Forecast by End use, 2024-2030 |
21 | Product installation rate by OEM, 2023 |
22 | Incline/Decline in Average B-2-B selling price in past 5 years |
23 | Competition from substitute products |
24 | Gross margin and average profitability of suppliers |
25 | New product development in past 12 months |
26 | M&A in past 12 months |
27 | Growth strategy of leading players |
28 | Market share of vendors, 2023 |
29 | Company Profiles |
30 | Unmet needs and opportunity for new suppliers |
31 | Conclusion |
32 | Appendix |