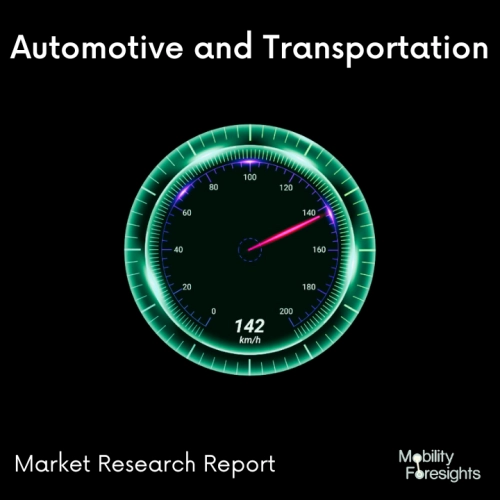
- Get in Touch with Us
Last Updated: Apr 25, 2025 | Study Period: 2023-2030
Plastics are an essential component of electric vehicles since they house the EV control unit. The battery, motor, and other internal electrical systems, as well as the EV control units, are under the supervision of these units.
An EV control unit's casing needs to be durable enough to survive the extreme conditions that arise from being in motion while also shielding the interior parts from the elements.
Plastics are the preferred material for EV control unit housing due to their strength, adaptability, and longevity. Plastics are perfect for building a unique enclosure for the EV control unit because they are lightweight and versatile. Plastics are perfect for use in automobiles because they are corrosion- and wear-resistant.
Plastic housings can also be easily modified to match the requirements of a certain vehicle or application. There are a number of things to take into account when choosing a plastic to be used in the casing of an EV control unit.
The kind of plastic chosen is the most crucial element. For usage in an EV control unit housing, materials including polypropylene, polyethylene, and ABS are all acceptable choices.
However, different materials can be more suited depending on the situation and use. When choosing a plastic for the enclosure of an EV control unit
The Global EV control unit housing plastics market accounted for $XX Billion in 2022 and is anticipated to reach $XX Billion by 2030, registering a CAGR of XX% from 2023 to 2030.
Mitsubishi Electric develops and produces EV ECUs leveraging the expertise in control of powertrain (engine, transmission) and power electronics (inverter, battery) for optimum control technology, and experience of powertrain ECU development for compact, light-weight and low cost design Unification of control and monitoring for EV functions, Lightweight plastic housing, Compact body with advanced micro computer and system LSI
Speciality chemicals company LANXESS and Kautex Textron GmbH & Co. KG, a Textron Inc. company, have been collaborating for several years to research whether battery housings for electric vehicles can be designed and manufactured from technical thermoplastics.
Together, they have developed a near-series technology demonstrator in a feasibility study. With a length and width of around 1,400 millimetres each, the system is a technically sophisticated, large-format all-plastic housing part with a weight in the mid-double-digit kilogram range.
The goal of the project was to demonstrate the advantages of thermoplastics over metals in terms of weight and cost reduction, functional integration and electrical insulation behaviour.
Sl no | Topic |
1 | Market Segmentation |
2 | Scope of the report |
3 | Abbreviations |
4 | Research Methodology |
5 | Executive Summary |
6 | Introduction |
7 | Insights from Industry stakeholders |
8 | Cost breakdown of Product by sub-components and average profit margin |
9 | Disruptive innovation in the Industry |
10 | Technology trends in the Industry |
11 | Consumer trends in the industry |
12 | Recent Production Milestones |
13 | Component Manufacturing in US, EU and China |
14 | COVID-19 impact on overall market |
15 | COVID-19 impact on Production of components |
16 | COVID-19 impact on Point of sale |
17 | Market Segmentation, Dynamics and Forecast by Geography, 2023-2030 |
18 | Market Segmentation, Dynamics and Forecast by Product Type, 2023-2030 |
19 | Market Segmentation, Dynamics and Forecast by Application, 2023-2030 |
20 | Market Segmentation, Dynamics and Forecast by End use, 2023-2030 |
21 | Product installation rate by OEM, 2023 |
22 | Incline/Decline in Average B-2-B selling price in past 5 years |
23 | Competition from substitute products |
24 | Gross margin and average profitability of suppliers |
25 | New product development in past 12 months |
26 | M&A in past 12 months |
27 | Growth strategy of leading players |
28 | Market share of vendors, 2023 |
29 | Company Profiles |
30 | Unmet needs and opportunity for new suppliers |
31 | Conclusion |
32 | Appendix |