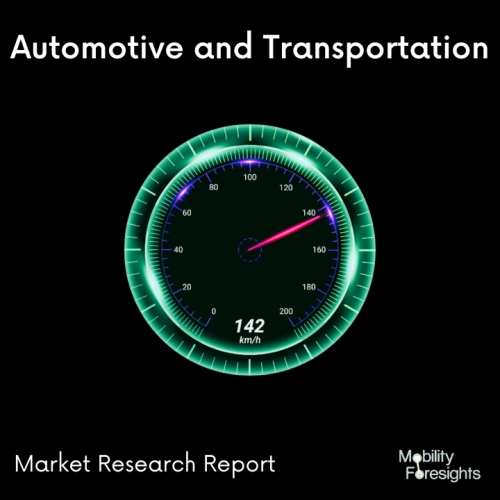
- Get in Touch with Us
Last Updated: Apr 25, 2025 | Study Period: 2023-2030
Shielding agents are smeared on the plastic enclosure enclosing delicate electronics in EMI shielding polymers. Plastics can be used for EMI shielding in one of two ways: by coating with conductive metals or by combining with conductive materials.
A tried-and-true technique for EMI shielding in consumer electronics and the automotive sector is coating polymers with conductive metals.
Given the significance of weight in electronics design. Space and weight are optimised through design iterations without compromising the circuit's reliable operation.
The metal enclosure used in electronic circuits for electromagnetic interference (EMI) shielding adds a significant amount of weight. However, because they shield circuits from both incoming and outgoing EMI, these enclosures cannot be removed.
Advancements in plastic technology include EMI shielding polymers, a new development in the electronics sector that uses plastic enclosures in place of shielding cans or Faraday cages. Plastic EMI shielding is portable and gives shielded circuits high EMC.
The need for EMI shielding grows along with the introduction of microprocessors. These barriers significantly improve the electromagnetic immunity of equipment.
Using EMI shielding polymers is a popular, practical way to prevent EMI. This EMI mitigation method makes use of shielding materials attached to the plastic housing of a delicate circuit.
The size of the moulded plastic part and the needed immunity to electromagnetic interference are taken into consideration when choosing the kind and form of shielding agent. Conductive coatings are utilised to cover the plastic enclosure in EMI shielding polymers for EMI shielding.
The Global EV EMI shielding plastics market accounted for $XX Billion in 2022 and is anticipated to reach $XX Billion by 2030, registering a CAGR of XX% from 2023 to 2030.
3M EMI Grounding and shielding tapes for EV Battery - 3M grounding and shielding tapes feature pressure-sensitive acrylic and silicone adhesives which serves multiple global markets including electronics and automotive.
They are specially engineered with conductive particle fillers for low and stable contact resistance, uniform conductivity and maintaining adhesion in the harsh environments.
3M ECATTs, electrically conductive foil tapes and fabric tapes are suitable for xEV battery module and cooling plate grounding, battery cover grounding and shielding, battery management system (BMS) grounding and shielding and other EV battery applications.
Sl no | Topic |
1 | Market Segmentation |
2 | Scope of the report |
3 | Abbreviations |
4 | Research Methodology |
5 | Executive Summary |
6 | Introduction |
7 | Insights from Industry stakeholders |
8 | Cost breakdown of Product by sub-components and average profit margin |
9 | Disruptive innovation in the Industry |
10 | Technology trends in the Industry |
11 | Consumer trends in the industry |
12 | Recent Production Milestones |
13 | Component Manufacturing in US, EU and China |
14 | COVID-19 impact on overall market |
15 | COVID-19 impact on Production of components |
16 | COVID-19 impact on Point of sale |
17 | Market Segmentation, Dynamics and Forecast by Geography, 2023-2030 |
18 | Market Segmentation, Dynamics and Forecast by Product Type, 2023-2030 |
19 | Market Segmentation, Dynamics and Forecast by Application, 2023-2030 |
20 | Market Segmentation, Dynamics and Forecast by End use, 2023-2030 |
21 | Product installation rate by OEM, 2023 |
22 | Incline/Decline in Average B-2-B selling price in past 5 years |
23 | Competition from substitute products |
24 | Gross margin and average profitability of suppliers |
25 | New product development in past 12 months |
26 | M&A in past 12 months |
27 | Growth strategy of leading players |
28 | Market share of vendors, 2023 |
29 | Company Profiles |
30 | Unmet needs and opportunity for new suppliers |
31 | Conclusion |
32 | Appendix |