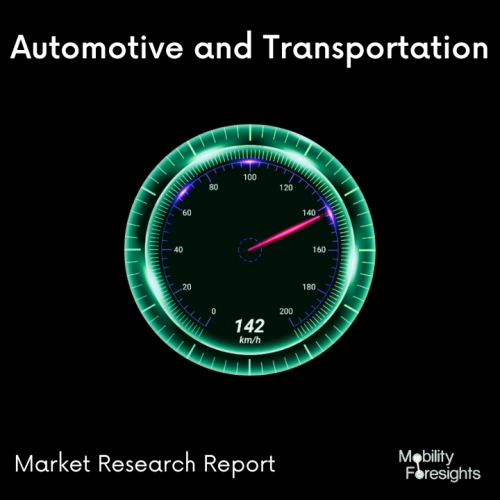
- Get in Touch with Us
Last Updated: Apr 25, 2025 | Study Period: 2024-2030
Lithium-ion (Li-ion), Nickel Manganese Cobalt (NMC), Nickel Metal Hydride (Ni-MH), Lithium Sulphur (Li-S), and Lead-Acid are the five battery chemistries that are most frequently used in electric vehicles. Instead of Lithium-ion batteries, hybrid vehicles frequently use nickel-metal hydride batteries.
The powder coating on electric vehicle (EV) batteries is particularly prepared for electrical insulation applications and possesses dielectric insulator qualities.
Plastic can act as an insulator or a conductor for electricity. It thus fills distinct roles in batteries, alternative drivetrains, and propulsion. There is increasing international pressure to keep reducing greenhouse gas emissions.
Electric car batteries are made of a variety of metals, each having advantages. Lithium, nickel, cobalt, manganese, etc., are some of the most popular metals. These metals are appropriate for usage in batteries since they are crucial to the battery's performance and lifespan.
Glass that has a coating put to it, known as low emissivity glass or low E glass, makes windows and doors significantly more energy efficient. They were first created to keep infrared light for colder climates, but they are now a practical choice that works in many places.
Electrocoating is preferred in applications where a hard finish is required since it leaves a finish that is stronger than paint. By means of electroplating, metallic particles are applied to the surface of the goods.
The metallic particles, which can be silver, gold, copper, chrome, nickel, etc., can be utilised on metal, plastic, and even glass. V denotes electric vehicles (or electric cars). In place of a conventional internal combustion engine, EVs use a battery-powered motor.
The Global EV Fiberglass Resin market accounted for $XX Billion in 2023 and is anticipated to reach $XX Billion by 2030, registering a CAGR of XX% from 2024 to 2030.
Addwaya Chemicals Private Limited,The usage of EV adhesives in numerous electric vehicle applications, including the exterior, interior, and battery, is one of the main drivers of the business for these adhesives. The switch from internal combustion engines (ICE) to electric vehicles will be crucial for the risein EV adhesive usage. Global demand for electric vehicles is being driven by tighter emission regulations and growing concerns about climate change.
To increase the battery pack's integrity and crashworthiness, epoxy adhesives are used. Epoxies are the strongest and longest-lasting structural adhesives of all resin types. In addition, epoxy bonding exhibit outstanding resistance to shock, vibration, and impact loads.
Because it distributes stress evenly along the entire bond, thinner and lighter materials can be used in electric car construction.
The development of battery electric vehicles was fueled by significant legislative changes made by the world's top producers of electric mobility.
In addition to providing incentives for battery electric vehicles, these nations have tightened environmental regulations and are encouraging investments in the value chain of the electric vehicle industry to achieve price parity between electric and internal combustion engine (ICE) vehicles.
The same factors will increase global demand for battery electric vehicles even further. Due to its widespread use in various industries, adhesive technology is essential to an electric vehicle's ability to be lightweight.
Electric vehicle adhesive producers will have chances for growth throughout the projection period because to the expanding markets for electric vehicles in regions including Europe, Asia Pacific, and North America.
Sl no | Topic |
1 | Market Segmentation |
2 | Scope of the report |
3 | Abbreviations |
4 | Research Methodology |
5 | Executive Summary |
6 | Introduction |
7 | Insights from Industry stakeholders |
8 | Cost breakdown of Product by sub-components and average profit margin |
9 | Disruptive innovation in the Industry |
10 | Technology trends in the Industry |
11 | Consumer trends in the industry |
12 | Recent Production Milestones |
13 | Component Manufacturing in US, EU and China |
14 | COVID-19 impact on overall market |
15 | COVID-19 impact on Production of components |
16 | COVID-19 impact on Point of sale |
17 | Market Segmentation, Dynamics and Forecast by Geography, 2024-2030 |
18 | Market Segmentation, Dynamics and Forecast by Product Type, 2024-2030 |
19 | Market Segmentation, Dynamics and Forecast by Application, 2024-2030 |
20 | Market Segmentation, Dynamics and Forecast by End use, 2024-2030 |
21 | Product installation rate by OEM, 2023 |
22 | Incline/Decline in Average B-2-B selling price in past 5 years |
23 | Competition from substitute products |
24 | Gross margin and average profitability of suppliers |
25 | New product development in past 12 months |
26 | M&A in past 12 months |
27 | Growth strategy of leading players |
28 | Market share of vendors, 2023 |
29 | Company Profiles |
30 | Unmet needs and opportunity for new suppliers |
31 | Conclusion |
32 | Appendix |