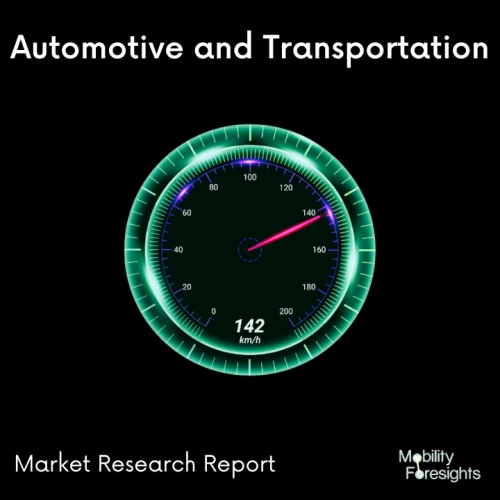
- Get in Touch with Us
Last Updated: Apr 25, 2025 | Study Period: 2024-2030
A gate driver is indeed a voltage regulator which receives a low-power input from a controller IC and generates the requirements of high gates output for a power supply. Modern power electronics systems are powered by power semiconductor devices.
Numerous gates semiconductor devices, including such conventional semiconductors, FETs, BJTs, MOSFETs, IGBTs, as well as others, are used as switching elements in switched-mode power supplies (SMPS), universal power supplies (UPS), and motor drives within those technologies.
Power electronics technological advance has largely tracked the advancement of power semiconductor devices. Inside the electronic power business, peak power needs and switching frequency are growing.
The gate of a power switch can never be operated by that of the production of something like a logical IC during high - voltage applications (PWM controller).
Since these reasoning terminals have limited current capacities, recharging the number of charge carriers would take an inordinate amount of time, almost certainly longer than the duration of a switching period.
As a result, separate controllers must always be utilised to apply a voltage and give driving current to both the energy product's gate. This might be a driving circuit, and it could be constructed using dedicated integrated circuits, individual transistors, or transducers.
It may also be included into a PWM controller IC. Large battery packages provide electricity to numerous energy conversion systems via high voltages and currents, while the primary DC-DC converter increases the energy towards the driver's low-voltage components.
The propulsion inverters are responsible for delivering mechanical power to the wheels. Finally, the battery charging mechanism supplies electricity to the batteries, restarting the complete experience.
S No | Overview of Development | Development Detailing | Region of Development | Possible Future Outcomes |
1 | TIâs New Isolated Gate Driver Aims to Boost Efficiency in EV Powertrains | The new isolated gate driver for high-powered SiC and GaN power devices is said to reduce PCB space, eliminate external components, and increase power efficiency in EVs. | Global Scale | This would enhance better Technologies and production |
Power is converted from one form to another by every technology. An elevated switching and a reduced switching simultaneously flip the load's connections between the high-voltage positive and negative rails in this design.
Driving the gates of these switches is critical to maximise productiveness devices operate as close to perfect switching as feasible. Several gate driver design requirements for something like the chosen SiC metal-oxide-semiconductor field-transistor (MOSFET) power devices have already been put on the market with the goal of developing a silicon carbide (SiC) inverter for electric vehicle/hybrid electric vehicle (EV/HEV) technologies.
Considering the demand for network power density, the gate driver engineering difficulties for commercial off-the-shelf (COTS) SiC modules are recognised, examined, and addressed.
With modest investments in development, research, and testing, the gate driver IC sector is predicted to yield significant revenue production in the next few years. The controller ICs industry, on the other hand, is reaching maturity and is likely to create moderate income for major players in the upcoming decades.
Gate driver integrated circuits are suitable for a wide range of purposes, including large household appliances, industrial motor drives, solar inverters, UPS, managed to switch power supply, and high - voltage power illumination.
Furthermore, the usage of power transistors in various renewable energy systems encourages the use of gate driver ICs by diverse producers.
The increased use of silicon carbide gate drivers and gallium nitride gate drivers ensures great energy capacity and better and more interesting safety.
Associated with increasing use of smart home and smart grid innovations, as well as increased need for operating power operational components, are likely to fuel upcoming gate driver IC growth in the economy.
Nevertheless, the design difficulties of gate driver ICs function as significant hurdles to industry expansion. Additionally, factors such as the increasing electrification of autos and a boom in power transistors in different renewable energy systems are likely to provide attractive development prospects.
The Global EV Gate Driver Integrated Circuit Market can be segmented into following categories for further analysis.
IGBT gate drive circuitry had already progressed beyond basic impedance selection in the gates drive circuit to much more vastly complicated modulation of the gate drive resistance during the switching event.
These enhanced approaches reduce collector current and voltage overshoots during IGBT changing occurrences whilst minimising shifting power outage.
This enables for greater efficiency of IGBT-based inverter circuits. Modern IGBT modules are also engineered to survive load short circuits. The IGBT collector current can surge to many points of time in a typical constant state throughout a loaded fault condition.
Many complicated power conversion systems have multiple half-bridge configurations. Motors used during electric car drive systems, for illustration, are normally three-phase electric motors with each component cycled from one to another to provide momentum.
To power each phase of the motor, the traction inverter employs three half-bridge circuitry. Because there are multiple power components and gate controllers, properly arranging the gate driver power distribution has a significant effect on the performance.
The three-phase inverters additionally demonstrates the swap for various power transmission topologies, which seem to be equally applicable to other circuits that use only one or two half-bridge circuits.
Electric cars, as well as the energy conversion technologies on which they rely, are here to stay. Voltage regulators will indeed be challenged to attain quicker changeover rates, more complex topologies, and higher voltages as expectations for efficiency improvements and greater duration continue to go up.
Future power switching components and developments in gate driver technology will push half-bridge circuit performance to greater heights. Whilst the half-bridge circuitry advances, power domain architecture will remain an important engineering concern for many years to come.
Numerous businesses have produced gate driver solutions as a result of the increasing usage of IGBTs for motor control. System design has been one of the primary issues impeding the growth of the gate driver IC industry.
Microprocessors, in principle, have a large number of transistors and long copper connections. Furthermore, semiconductors should really be extremely dependable.
Renesas is one of the leading developers of the Gate Integrated Circuits focused on Electric and Hybrid Vehicles in the market. The R2A25110KSP is one of the integrated solutions for the gate circuits in the industrial focus.
For data transfer with high voltage isolation between the primary circuit (MCU side) and the secondary circuit, a Micro Isolator with such a hollow shaft transformer construction is used (IGBT side).
This apparatus uses an IGBT gate drive circuitry, a Miller clamping loop, a soft switching raceway, and other protective circuits such as IGBT temperature sensing. This gadget can also drive parallel IGBTs.
It is an intelligent power device used in high voltage converter applications for IGBT gate-drive. For data transmission featuring high voltage isolation between the primary circuit (MCU side) and the secondary circuit, a Micro Isolator with such a coreless transformer construction is used (IGBT side).
ROHM Solutions is one of the integrated effort solution providers for EV Gate drivers in the industrial forefront. ROHM gate controllers include an isolated gate driver element that makes use of the most recent BiC-DMOS technologies as well as innovative on-chip transformers innovation.
This allows for the corporation's lowest usable capacity, which contributes to overall miniaturisation. Furthermore, gate drivers incorporate protection elements and meet automotive quality requirements while providing higher noise immunity, lower current usage, shortened integral gain, and outstanding thermal resistance when compared with conventional photocoupler forms, improving control performance, and reducing load capacity.
The engine in an EV is supplemented with high-voltage batteries and motors. The DC/DC conversion changes power components and employs a transformer to address the increasing voltage of the battery.
ROHM DC/DC converters with integrated SiC MOSFETs enable high-speed shifting, allowing for increased compactness and efficiency whilst boosting reliability.
Sl no | Topic |
1 | Market Segmentation |
2 | Scope of the report |
3 | Abbreviations |
4 | Research Methodology |
5 | Executive Summary |
6 | Introduction |
7 | Insights from Industry stakeholders |
8 | Cost breakdown of Product by sub-components and average profit margin |
9 | Disruptive innovation in the Industry |
10 | Technology trends in the Industry |
11 | Consumer trends in the industry |
12 | Recent Production Milestones |
13 | Component Manufacturing in US, EU and China |
14 | COVID-19 impact on overall market |
15 | COVID-19 impact on Production of components |
16 | COVID-19 impact on Point of sale |
17 | Market Segmentation, Dynamics and Forecast by Geography, 2024-2030 |
18 | Market Segmentation, Dynamics and Forecast by Product Type, 2024-2030 |
19 | Market Segmentation, Dynamics and Forecast by Application, 2024-2030 |
20 | Market Segmentation, Dynamics and Forecast by End use, 2024-2030 |
21 | Product installation rate by OEM, 2023 |
22 | Incline/Decline in Average B-2-B selling price in past 5 years |
23 | Competition from substitute products |
24 | Gross margin and average profitability of suppliers |
25 | New product development in past 12 months |
26 | M&A in past 12 months |
27 | Growth strategy of leading players |
28 | Market share of vendors, 2023 |
29 | Company Profiles |
30 | Unmet needs and opportunity for new suppliers |
31 | Conclusion |
32 | Appendix |