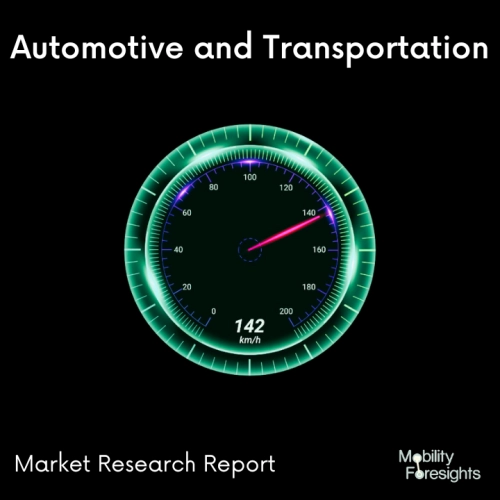
- Get in Touch with Us
Last Updated: Apr 25, 2025 | Study Period: 2023-2030
LSR is a thick liquid polymer that is produced using a clean liquid injection moulding technique to create components. The most stable LSRs are two-part, platinum-cured polymers used in liquid injection moulding.
A chemical link holds two parts of the silicone-based polymer known as liquid silicone rubber (LSR) together. It is most frequently used to produce injection moulded components for commodities utilised in sectors like consumer goods, automotive, food, appliances, and textiles.
The base-forming substance is kept in one container, and the catalyst is kept in the other. By means of a specialised pump, these two substances are combined and released into the mould cavity. The silicone is poured into the mould cavity at a high pressure using an injection screw once the mould has been constructed.
A two-part platinum-cured elastomer that can be injected into a mould cavity to create a part is called liquid silicone rubber. In the elastomer sector, LSR is particularly adaptable and is used in a wide range of components, from consumer goods to medical equipment and everything in between.
Long polysiloxane chains are strengthened with chemically treated silica in the two-component method known as liquid silicone rubber (LSR). A platinum catalyst is present in Component A, and Methylhydrogensiloxane, a cross-linker and an alcohol inhibitor, is present in Component B.Typically, they are thermoplastic and elastomeric copolymers, or a combination of plastic and rubber.
Rubbers made of thermoset and thermoplastic materials can frequently be used interchangeably.
The Global EV liquid silicone injection molding system market accounted for $XX Billion in 2022 and is anticipated to reach $XX Billion by 2030, registering a CAGR of XX% from 2023 to 2030.
Dynamics CorporationPvt Ltd Easy-to-mold (and demold) low or high viscosity rubber silicones are needed by manufacturers in a variety of industries, including automotive, healthcare, general industry, infant care, consumer products, and electronics, to make parts quickly and affordably.
The material of choice for injection moulding applications is liquid silicone rubber (LSR). The repeating Si-O chains that make up the silicone backbone are very flexible and provide this chemical structure special qualities such a wide operating temperature range, weatherability, hydrophobicity, bio-inertness, electrical insulation, and a long lifespan.
Rapid production of high-quality parts is crucial in the LSR moulding industry. The most effective and financially viable process is liquid injection moulding, which uses liquid silicone rubber (LSR). Elkem Silicones provides a broad assortment of general-purpose LSR materials with durometers ranging from 01 to 70 Shore A. These materials were created with outstanding physical and mechanical qualities, a quick cure, and great mould release.
Sl no | Topic |
1 | Market Segmentation |
2 | Scope of the report |
3 | Abbreviations |
4 | Research Methodology |
5 | Executive Summary |
6 | Introduction |
7 | Insights from Industry stakeholders |
8 | Cost breakdown of Product by sub-components and average profit margin |
9 | Disruptive innovation in the Industry |
10 | Technology trends in the Industry |
11 | Consumer trends in the industry |
12 | Recent Production Milestones |
13 | Component Manufacturing in US, EU and China |
14 | COVID-19 impact on overall market |
15 | COVID-19 impact on Production of components |
16 | COVID-19 impact on Point of sale |
17 | Market Segmentation, Dynamics and Forecast by Geography, 2023-2030 |
18 | Market Segmentation, Dynamics and Forecast by Product Type, 2023-2030 |
19 | Market Segmentation, Dynamics and Forecast by Application, 2023-2030 |
20 | Market Segmentation, Dynamics and Forecast by End use, 2023-2030 |
21 | Product installation rate by OEM, 2023 |
22 | Incline/Decline in Average B-2-B selling price in past 5 years |
23 | Competition from substitute products |
24 | Gross margin and average profitability of suppliers |
25 | New product development in past 12 months |
26 | M&A in past 12 months |
27 | Growth strategy of leading players |
28 | Market share of vendors, 2023 |
29 | Company Profiles |
30 | Unmet needs and opportunity for new suppliers |
31 | Conclusion |
32 | Appendix |