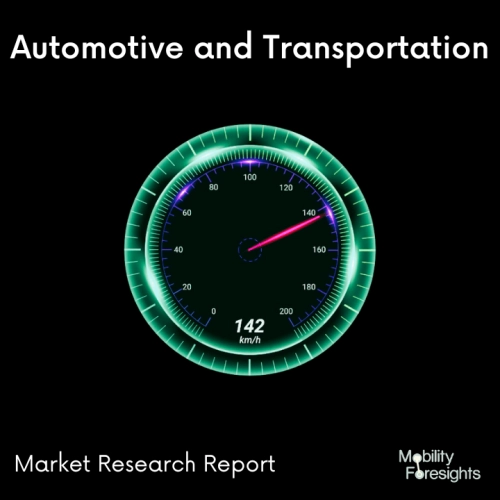
- Get in Touch with Us
Last Updated: Apr 25, 2025 | Study Period: 2024-2030
The major constituents of electric vehicle systems are the motor, power supply, controller, drive train and a charger.An EVM controller or electric vehicle motor controller is used to regulate the torque generated by the motors of electric vehicles by means of modifying the energy flow from the power sources to the motor.Motor controller is a device that improves the performance of an electric motor in a prearranged manner
As the hybrid electric vehicles/electric vehicles (HEV/EV) market begins to grow further, the need for efficient and smarter motor control becomes more critical.
Today more than ever, original equipment manufacturers (OEMs) are focused on how to enhance the capability of electric motors (for example, torque control), while maintaining a high-level of system visibility via diagnostics to always know the health of the system.
To reach these goals, highly integrated solutions in the motor-position control, especially dealing with motor efficiency and torque control, are essential.
One of the key factors that will drive the motor controller market will be due to the use of micro control modules in direct drives to incorporate dynamic safety features.
Currently, permanent magnet synchronous motors (PMSM) are most widely used because of their high efficiency, high-power density and high torque, even at low speeds.AC Induction motor is seeing increased usage among vehicles mainly in the premium electric vehicles.
Tesla uses Permanent Magnet Synchronous Reluctance Motors (PMSRM) in their vehicles and is the only OEM to use this motor type.In 2020, even after Covid the global sales of plugged in vehicles saw a rise with Europe being the market leader followed by China and USA. The market shows no signs of slowing down.
One of the key factors that will drive the electric vehicle motor controller market will be due to the use of micro control modules in direct drives to incorporate dynamic safety features.
Nevertheless, the high price of controllers and the complexity of functions and architecture remains a challenge for manufacturers.
According to Delphi, the 48-volt, mild hybrid market is predicted to grow 10-times from 2019 to 2025, which is nearly 20 million vehicles, with China and Europe dominating the landscape, respectively.
The 48-volt system is expected to represent 50 percent of the overall hybrid market by 2025, or some 12 million units, which is one out of every 10 vehicles sold.
For the market for electric vehicle motor control, Microchip Technology Inc. (Microchip) has introduced the LX34070 IC, a novel inductive position sensor.
The recently released LX34070 IC is designed for motor control applications in electric vehicles (EVs). The sensor has properties that enable functional safety for ISO 26262 compliance under the Automotive Safety Integrity Level-C (ASIL-C) classification, such as differential outputs and quick sample rates.
The LX34070 inductive position sensor makes it possible to create motor control systems that are lighter, more compact, more dependable, meet strict safety regulations, cost less overall to build, and function precisely and noiselessly with the DC motors, high currents, and solenoids found in automobiles.
Combining the LX34070 with other functional-safety-ready Microchip components, such as the 8-bit AVR and PIC microcontrollers, the 32-bit microcontrollers, and dsPIC digital signal controllers, allows designers to further optimise EV motor control designs.
The company wants to hasten the global transition away from magnet-based EV motor position monitoring systems with the LX44070 IC.
According to Microchip's official release, manufacturers of motor control systems are quickly switching away from Hall Effect position sensors and outdated magnetic resolver technologies in favour of inductive replacements that do not require costly magnets or other bulky transformer-based structures and can be integrated onto straightforward, small printed circuit boards (PCBs).
The latest LX34070 IC sensor, according to the company, brings the same tried-and-true PCB materials, approaches, and simplified, low-cost packaging to EV motor control and other applications that need its high-speed and low-latency benefits. Microchip released its first volume of inductive sensors for automotive and industrial applications.
1 | Market Segmentation | 3 |
2 | Executive Summary | 5-6 |
3 | Introduction | 7-10 |
4 | Insights from Industry stakeholders | 11 |
5 | Key criteria for EV Transmission adoption by OEMs | 12-13 |
6 | EV Transmission manufacturing in US, Europe and China | 14-15 |
7 | Breakdown of new EV concept vehicles by powertrain | 16-17 |
8 | Upcoming EV platforms utilizing E-axle | 18-19 |
9 | Disruptive innovations in EV Transmission market | 20-21 |
10 | Cost breakup of EV transmission and average margin | 22-23 |
11 | Market Size ,Dynamics and Forecast By Input torque | 24-30 |
12 | Market Size ,Dynamics and Forecast By Application | 31-39 |
13 | Market Size ,Dynamics and Forecast By Geography | 41-55 |
14 | Market Size ,Dynamics and Forecast By Transmission type | 56-64 |
15 | Competitive Landscape | 65-69 |
16 | Market share of leading players | 70 |
17 | Company Profiles | 71-82 |
18 | Unmet needs and Market Opportunity for suppliers | 83-84 |
19 | Conclusion | 85 |
20 | Appendix | 86 |