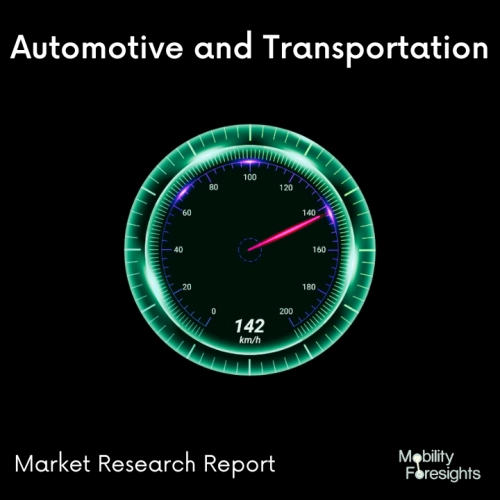
- Get in Touch with Us
Last Updated: Apr 25, 2025 | Study Period: 2024-2030
The main function of composite battery enclosures for EVs, often known as frames, boxes, or housings, is to store and safeguard battery cells. They come in a variety of sizes and forms. A battery cover with a composite design is up to 40% lighter while exhibiting comparable mechanical qualities.
The main function of composite battery enclosures for EVs, often known as frames, boxes, or housings, is to store and safeguard battery cells. They come in a variety of sizes and forms. A composite construction battery container exhibits similar mechanical qualities while being up to 40% lighter.
Multiple advantages are offered by composite battery casing. They reduce weight, free up design space, improve safety and fire safety, better control thermal energy, prevent corrosion, and offer high electromagnetic compatibility (EMC). Additional advantages include automated production, series production that meets the quality and quantity requirements for vehicle manufacture, and weight reduction.
Traditional possibilities for battery enclosure materials include steel and aluminum. Composites, though, are probably going to be a better option. The performance of EVs is expected to increase dramatically as a result.Based on type and end-use, the worldwide composite battery enclosure market may be divided.
TheGlobal EV Multi-Material Composite Battery Enclosure marketaccounted for $XX Billion in 2023 and is anticipated to reach $XX Billion by 2030, registering a CAGR of XX% from 2024 to 2030.
Teijin Automotive Technologies (formerly Continental Structural Plastics) declared today that the Society of Plastics Engineers (SPE) ACCE People's Choice Award has been given to its creator, an EV Multi-Material Composite Battery Enclosure. All attendees at the annual automotive composites exposition vote for the winner of this prize from among the SPE ACCE Innovation Awards submissions.
The full-sized, multi-material battery enclosure has a one-piece composite tray and lid with reinforcements made of steel and aluminum. Teijin Automotive has developed a solution that is simpler to seal and that can be approved before shipment by molding the lid and the tray separately into one piece. The business has two patent applications in process for its unique box assembly and fastening systems.
The business also created a mounting structure that absorbs energy using structural foam. This enhances crash performance while allowing for a thinner, lighter structure. The tray and cover may be molded into intricate designs while requiring less complicated and expensive tooling because they are composed of composite materials.
The multi-material battery enclosure from Teijin Automotive is 15% lighter than a steel battery box. Despite weighing the same as an aluminum enclosure, the enclosure is more temperature resistant, especially if the phenolic resin is utilized. There are no through holes in the tray's one-piece design, therefore sealing or sealant is not necessary. This lowers the total cost and complexity of production while also eliminating the possibility of leaks.
Sl no | Topic |
1 | Market Segmentation |
2 | Scope of the report |
3 | Abbreviations |
4 | Research Methodology |
5 | Executive Summary |
6 | Introduction |
7 | Insights from Industry stakeholders |
8 | Cost breakdown of Product by sub-components and average profit margin |
9 | Disruptive innovation in the Industry |
10 | Technology trends in the Industry |
11 | Consumer trends in the industry |
12 | Recent Production Milestones |
13 | Component Manufacturing in US, EU and China |
14 | COVID-19 impact on overall market |
15 | COVID-19 impact on Production of components |
16 | COVID-19 impact on Point of sale |
17 | Market Segmentation, Dynamics and Forecast by Geography, 2024-2030 |
18 | Market Segmentation, Dynamics and Forecast by Product Type, 2024-2030 |
19 | Market Segmentation, Dynamics and Forecast by Application, 2024-2030 |
20 | Market Segmentation, Dynamics and Forecast by End use, 2024-2030 |
21 | Product installation rate by OEM, 2023 |
22 | Incline/Decline in Average B-2-B selling price in past 5 years |
23 | Competition from substitute products |
24 | Gross margin and average profitability of suppliers |
25 | New product development in past 12 months |
26 | M&A in past 12 months |
27 | Growth strategy of leading players |
28 | Market share of vendors, 2023 |
29 | Company Profiles |
30 | Unmet needs and opportunity for new suppliers |
31 | Conclusion |
32 | Appendix |