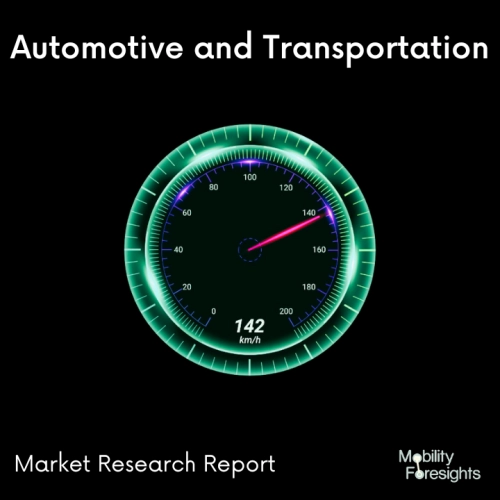
- Get in Touch with Us
Last Updated: Apr 26, 2025 | Study Period: 2023-2030
The conventional internal combustion engine (ICE) cooling system and indirect liquid cooling systems for electric vehicles both circulate coolant through a network of metal pipes to conduct heat away from the battery pack or engine, respectively.
The battery is cooled using a liquid coolant such ethylene glycol, water, or a refrigerant. The liquid passes via tubes, cold plates, or other parts that surround the cells and transfer heat to another area, such a radiator or a heat exchanger.
The Global EV multilayer cooling pipes market accounted for $XX Billion in 2022 and is anticipated to reach $XX Billion by 2030, registering a CAGR of XX% from 2023 to 2030.
Performance and Sustainability for EV Multilayer Cooling Lines was launched by DuPont eCool Technology. This solution addresses the issue of increased cooling line requirements in xEVs, a direct result of the critical requirement to manage heat and energy for maximum battery operation, safety, and range.
For EV batteries to continue performing at their best, automotive cooling lines are essential. Furthermore, they represent a significant target for sustainability improvement due to their size.
They provide the industry with a cost-effective, high-performance, flexible, and more sustainable solution with eCool solution. Up to three times as many cooling lines as those found in ICE systems may be needed for electric vehicles.
DuPontTM eCool technology, which is based on the firm's Zytel® LCPA Long Chain Polyamide grades co-extruded with thermoplastic olefin elastomer, offers a viable substitute for existing, heavier solutions including thick EPDM rubber hoses and other thermoplastic components.
While maintaining cost-competitiveness, the eCool solution not only reduces weight but also better withstand a variety of EV cooling fluids.
Additionally, DuPont determined that its eCool solution may drastically cut the Global Warming Potential (GWP) of these cooling tubes when compared to monolayer PA12 tubes, cutting it by more than half.
In addition to other application development facilities throughout the world, DuPont's Center of Excellence in Geneva offers production-level support for eCool technology.
Extrusion trials, assistance with post-processing, welding, burst pressure testing, mechanical evaluation of properties prior to and following air and chemical aging, salt stress cracking, cold impact resistance, and bend testing are some of the advanced CAE/FEA simulation techniques that are covered in this.
DuPont gives its clients the option to create cooling lines under nearly commercial circumstances, test them, and then fine-tune the process and postprocessing as needed.
Sl no | Topic |
1 | Market Segmentation |
2 | Scope of the report |
3 | Abbreviations |
4 | Research Methodology |
5 | Executive Summary |
6 | Introduction |
7 | Insights from Industry stakeholders |
8 | Cost breakdown of Product by sub-components and average profit margin |
9 | Disruptive innovation in the Industry |
10 | Technology trends in the Industry |
11 | Consumer trends in the industry |
12 | Recent Production Milestones |
13 | Component Manufacturing in US, EU and China |
14 | COVID-19 impact on overall market |
15 | COVID-19 impact on Production of components |
16 | COVID-19 impact on Point of sale |
17 | Market Segmentation, Dynamics and Forecast by Geography, 2023-2030 |
18 | Market Segmentation, Dynamics and Forecast by Product Type, 2023-2030 |
19 | Market Segmentation, Dynamics and Forecast by Application, 2023-2030 |
20 | Market Segmentation, Dynamics and Forecast by End use, 2023-2030 |
21 | Product installation rate by OEM, 2023 |
22 | Incline/Decline in Average B-2-B selling price in past 5 years |
23 | Competition from substitute products |
24 | Gross margin and average profitability of suppliers |
25 | New product development in past 12 months |
26 | M&A in past 12 months |
27 | Growth strategy of leading players |
28 | Market share of vendors, 2023 |
29 | Company Profiles |
30 | Unmet needs and opportunity for new suppliers |
31 | Conclusion |
32 | Appendix |