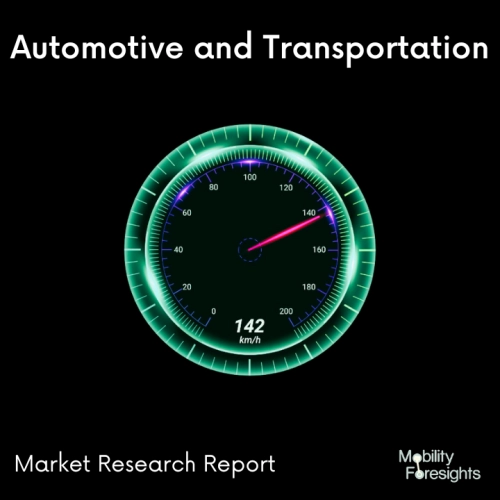
- Get in Touch with Us
Last Updated: Apr 25, 2025 | Study Period: 2023-2030
The multiplexed Rear-fed Fuse and Relay Module (mRFRM), which features a Controller Area Network (CAN) interface and rear fed sealed connectors, is an improved version of the Rear-fed Fuse and Relay Module (RFRM).
The Multiplexed Rear Fed Fuse and Relay (mRFRM) module can be a part of a multiplexing system that reduces the need for individual connections between switches and loads.
It connects with other components on the vehicle's CAN bus via the SAE J1939 protocol. The mRFRM operates by receiving messages to "on '' and "off"-cycle its relays and by sending messages to report the status of the components it is monitoring.
The Global EV Multiplexed Rear-fed Fuse and Relay market accounted for $XX Billion in 2022 and is anticipated to reach $XX Billion by 2030, registering a CAGR of XX% from 2023 to 2030.
A primary power distribution module that can function in challenging environmental conditions is available from the Series 15400 RFRM. The Eaton RFRM takes plug-in fuses, relays, circuit breakers, resistors, and diodes to satisfy a variety of power management requirements.
Its footprint is based on the industry standard 2.8mm (mini). To meet the needs of diverse OEMs, the RFRM is offered with a variety of internal busing choices.
As it contains a Controller Area Network (CAN) interface and rear fed sealed connectors, the multiplexed Rear-fed Fuse and Relay Module (mRFRM) is an improved version of the standard Rear-fed Fuse and Relay Module (RFRM).
In addition to twenty-eight (28) two-bladed sockets for fuses or circuit breakers (CB), the mRFRM has sockets for fourteen (14) relays (10 Form-A and 4 Form-C) and ten (14) relay sockets. A related fuse or CB protects every relay.
The outputs are independent with fourteen (14) fuses, or CB. A CAN control board, which keeps track of the condition of the components and manages relays plugged into the module, is electronically interfaced with all the output components.
A CAN control board, which keeps track of the condition of the components and manages relays plugged into the module, is electronically interfaced with all the output components.
Sl no | Topic |
1 | Market Segmentation |
2 | Scope of the report |
3 | Abbreviations |
4 | Research Methodology |
5 | Executive Summary |
6 | Introduction |
7 | Insights from Industry stakeholders |
8 | Cost breakdown of Product by sub-components and average profit margin |
9 | Disruptive innovation in the Industry |
10 | Technology trends in the Industry |
11 | Consumer trends in the industry |
12 | Recent Production Milestones |
13 | Component Manufacturing in US, EU and China |
14 | COVID-19 impact on overall market |
15 | COVID-19 impact on Production of components |
16 | COVID-19 impact on Point of sale |
17 | Market Segmentation, Dynamics and Forecast by Geography, 2023-2030 |
18 | Market Segmentation, Dynamics and Forecast by Product Type, 2023-2030 |
19 | Market Segmentation, Dynamics and Forecast by Application, 2023-2030 |
20 | Market Segmentation, Dynamics and Forecast by End use, 2023-2030 |
21 | Product installation rate by OEM, 2023 |
22 | Incline/Decline in Average B-2-B selling price in past 5 years |
23 | Competition from substitute products |
24 | Gross margin and average profitability of suppliers |
25 | New product development in past 12 months |
26 | M&A in past 12 months |
27 | Growth strategy of leading players |
28 | Market share of vendors, 2023 |
29 | Company Profiles |
30 | Unmet needs and opportunity for new suppliers |
31 | Conclusion |
32 | Appendix |