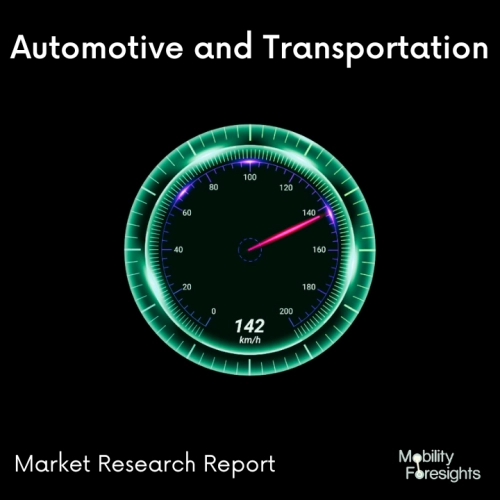
- Get in Touch with Us
Last Updated: Apr 25, 2025 | Study Period: 2023-2030
A collective term for a group of artificial long-chain polyamide resins. The term "nylon" is followed by a number that represents the number of carbon atoms in the monomer, such as "Nylon 6," to classify nylons.
When two numbers are given, as in the case of nylon 6,6, the polymer was created using a diamine and a dibasic acid. The initial production of nylon 6,6 began in the early 1930s by W. H. Carothers has a textile fiber known as fiber 66; the word nylon was first used by DuPont in 1938.
Nylons are thermoplastic polymers with exceptional tensile strength, toughness, elasticity, and resistance to abrasion. They can build up static electricity yet have strong electrical resistance.
The semi-crystalline engineering thermoplastics NY66 and NY6 (Nylon 6,6 and Nylon 6) are easily pigmented and can be produced in both injection moulding and extrusion applications. Nylons offer an outstanding level of chemical resistance. Two of the most popular engineering thermoplastics are nylon 66 and nylon 6.
They provide strong resistance to fungal assaults and excellent abrasion resistance in addition to chemical protection. Both nylon 66 and nylon 6 are strong, heat-resistant fabrics. By adding additives, these materials' physical qualities can be improved.
Flexural modulus values may be raised by the addition of glass fibres and/or mineral fillers. Molybdenum disulfide can be added to boost surface lubricity, and heat stabilisers can be added to increase long-term thermal stability.
Tough Nylon compositions can be created by adding impact modifiers. Due to Nylons' propensity to absorb water due to their hygroscopic qualities, humidity affects the majority of Nylon products.
Nylon is "plasticized" by absorbed water. The water that is absorbed will make the material more ductile and less rigid. The size of items made of Nylons will also increase due to water absorption. Even though water absorption is reversible, it must be considered when designing items that will be moulded from Nylons.
The Global EV Nylon Resin market accountedfor $XX Billion in 2021 and is anticipated to reach $XX Billion by 2030, registering a CAGR of XX% from 2022 to 2030.
A high-strength resin material called PA100 Nylon-Like Resin was created by eSUN for engineering and manufacturing. It has excellent precision, low shrinkage, good durability, good toughness, and is broadly compatible with both color and mono-screen printers.
It can be used to create models or components such as fixtures, stencils, aviation models, industrial parts, samples, joints, snaps, gears, etc. as an engineering-grade resin material.
A form of engineering thermoplastic known as nylon resin, often referred to as polyamide resin, is created from ethylenediamine with the aim of generating a variety of goods for industrial application, including films, hot-melt adhesives, binders, insulation, fibreglass, and filaments.
These resins are typically categorised as a class of polyamides, which are renowned for stability and adaptability in applications for mechanical engineering.
The crystallisation of polymer molecules, which determines a polymer's qualities and the sort of end product it will be used in, affects each type of nylon resin's specialised use. Nylon 66, which is frequently used to build extruded and moulded parts, makes up the bulk of resin produced in the United States.
While most nylon resins have great durability due to polymer crystallisation, some nylon resins can have their strength chemically increased by encouraging the production of new crystal nuclei, a process known as nucleation.
However, the application of nylon resin compounds is constrained by inherent differences between them, and a growing global trend toward the recycling of raw materials has changed the accessibility, efficacy, and affordability of products.
For example, nylon 6 can be processed more than many other types of nylon resins due to its moderate resistance to modified crystallisation. Due to its extended lifespan and the range of end products it may be utilised to create, this attribute makes this specific resin more appealing in terms of cost reduction.
Sl no | Topic |
1 | Market Segmentation |
2 | Scope of the report |
3 | Abbreviations |
4 | Research Methodology |
5 | Executive Summary |
6 | Introduction |
7 | Insights from Industry stakeholders |
8 | Cost breakdown of Product by sub-components and average profit margin |
9 | Disruptive innovation in the Industry |
10 | Technology trends in the Industry |
11 | Consumer trends in the industry |
12 | Recent Production Milestones |
13 | Component Manufacturing in US, EU and China |
14 | COVID-19 impact on overall market |
15 | COVID-19 impact on Production of components |
16 | COVID-19 impact on Point of sale |
17 | Market Segmentation, Dynamics and Forecast by Geography, 2023-2030 |
18 | Market Segmentation, Dynamics and Forecast by Product Type, 2023-2030 |
19 | Market Segmentation, Dynamics and Forecast by Application, 2023-2030 |
20 | Market Segmentation, Dynamics and Forecast by End use, 2023-2030 |
21 | Product installation rate by OEM, 2023 |
22 | Incline/Decline in Average B-2-B selling price in past 5 years |
23 | Competition from substitute products |
24 | Gross margin and average profitability of suppliers |
25 | New product development in past 12 months |
26 | M&A in past 12 months |
27 | Growth strategy of leading players |
28 | Market share of vendors, 2023 |
29 | Company Profiles |
30 | Unmet needs and opportunity for new suppliers |
31 | Conclusion |
32 | Appendix |