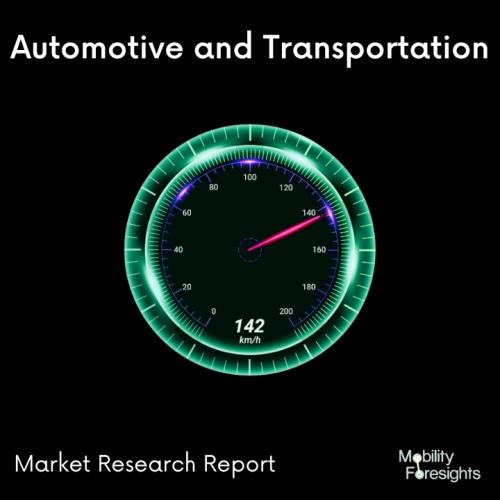
- Get in Touch with Us
Last Updated: Apr 25, 2025 | Study Period: 2023-2030
EV Coatings using drying oils are known as oil-based coatings. Following the application of this coating, it reacts with oxygen and the fundamental process of film formation takes place, turning the wet film into a solid film.
Fatty vegetable oil, a key component of oil-based coatings, works as the drying oil by chemically reacting with the oxygen in the air. The oil eventually dries and hardens.Fluid resistance has an exception known as oil resistance.
Oil resistance is, broadly speaking, the capacity of a rubber product to carry out its intended function when coming into contact with oil.
He acknowledges that the oil may inadvertently weaken or swell the elastomer to some extent. When immersed in oil, tyre rubbers progressively absorb the liquid until either all of the oil is gone or the rubber has broken down. They never find balance.
Only a little amount of oil is absorbed by the so-called oil-resistant elastomers, especially at high temperatures. It might not matter to certain people.
The majority of end uses for elastomers that are oil-resistant can tolerate noticeable swelling or volume increase. In light of this, volume gain is not a particularly reliable indicator of how well a rubber object would work in oil.
The Global EV Oil-resistant coating market accounted for $XX Billion in 2022 and is anticipated to reach $XX Billion by 2030, registering a CAGR of XX% from 2023 to 2030.
Oil and grease resistance may be easily added to a number of packaging applications with Ulterion brand launched oil resistant coatings, which also offer the greatest levels of repulpability, recyclability, and compostability.
A modified polymer called Ulterion 5125 OGB is created to be utilised as a film forming at the size press and calendar stack or as a binder in coating applications. In all applications, Ulterion 5125 OGB demonstrates exceptional viscosity stability.
Due to the physical strain of high-pressure sizing, it is unaffected. For sizing under conventional or high-pressure systems, rheological characteristics are excellent. In size press and coating applications, Ulterion 5125 OGB is entirely compatible with all frequently used additives.
It is simple to disseminate Ulterion 5125 OGB using batch or jet heating. It can be jet,cooked at solids levels of 15% or more, at temperatures ranging from 132°C to 154°C. Moreover, it may be cooked in batches at temperatures higher than 95°C for at least 15 minutes with solids levels as high as 35%.
Depending on the size press configuration, a lower solids sizing solution may be used when applied to low porosity papers. Higher solids sizing solutions may be needed for rod coaters and metered size press applications to produce better films with greater levels of oil and grease barrier properties.
Sl no | Topic |
1 | Market Segmentation |
2 | Scope of the report |
3 | Abbreviations |
4 | Research Methodology |
5 | Executive Summary |
6 | Introduction |
7 | Insights from Industry stakeholders |
8 | Cost breakdown of Product by sub-components and average profit margin |
9 | Disruptive innovation in the Industry |
10 | Technology trends in the Industry |
11 | Consumer trends in the industry |
12 | Recent Production Milestones |
13 | Component Manufacturing in US, EU and China |
14 | COVID-19 impact on overall market |
15 | COVID-19 impact on Production of components |
16 | COVID-19 impact on Point of sale |
17 | Market Segmentation, Dynamics and Forecast by Geography, 2023-2030 |
18 | Market Segmentation, Dynamics and Forecast by Product Type, 2023-2030 |
19 | Market Segmentation, Dynamics and Forecast by Application, 2023-2030 |
20 | Market Segmentation, Dynamics and Forecast by End use, 2023-2030 |
21 | Product installation rate by OEM, 2023 |
22 | Incline/Decline in Average B-2-B selling price in past 5 years |
23 | Competition from substitute products |
24 | Gross margin and average profitability of suppliers |
25 | New product development in past 12 months |
26 | M&A in past 12 months |
27 | Growth strategy of leading players |
28 | Market share of vendors, 2023 |
29 | Company Profiles |
30 | Unmet needs and opportunity for new suppliers |
31 | Conclusion |
32 | Appendix |