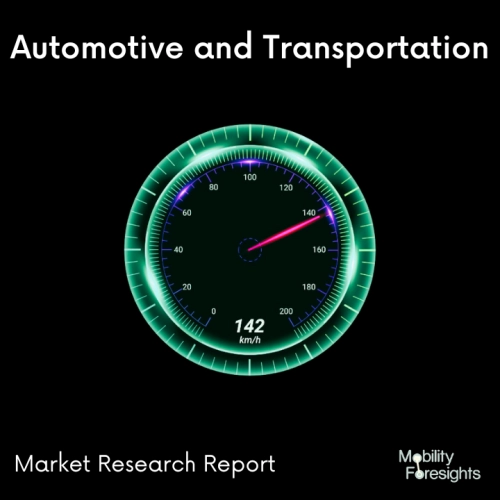
- Get in Touch with Us
Last Updated: Apr 25, 2025 | Study Period: 2023-2030
One of the essential components of passenger comfort is air conditioning in the cabin. The car sector needs to adopt an innovative strategy with better performance materials and technical know-how to comply with changing environmental standards.
Range of air conditioning system solutions goes beyond simply providing products. In any part of the world, our team of professionals is prepared to offer technical and regulatory support.
In an indirect charge air cooling system, the heat from the charge air cooler is vented to the ambient air by a downstream low-temperature radiator after first passing through a separate, low-temperature coolant circuit (LT cooling circuit) (LT radiator).
The engine cooling module holds the LT radiator of the indirect charge air cooling system, which allows for a more compact construction than the direct charge air cooler without compromising performance.
This occurs as a result of heat conduction from the air to the coolant. A temperature-sensitive lithium-ion battery, its power electronics, and soon the condenser of the refrigerant circuit may all be optimally thermally managed with the LT radiator.
Global EV polyamide air conditioning circuit market accounted for $XX Billion in 2022 and is anticipated to reach $XX Billion by 2030, registering a CAGR of XX% from 2023 to 2030.
Vehicles that use BEVs and HEVs have sophisticated, integrated cooling systems.Their high performance polymers' great mechanical strength, high flexibility, and ease of processing make them perfect for cooling circuits.
The materials of choice for cooling circuits are high performance long chain polyamides like Rilsan PA11 and Rilsamid PA12 because of their resilience to cooling media and corrosion from road salt.
The automobile sector can use Rilsan PA11, a bio-based, lightweight material manufactured from sustainable castor plants, in applications that must withstand harsh conditions.
The material performance requirements for air conditioning circuit lines are quite strict in terms of permeability, chemical resistance, and high-pressure resistance.
Market-leading Orgalloy polyamide alloys are used to replace metal-rubber hoses with high performance plastic compositions. The key characteristics of Orgalloy polyamide alloys, which include high processability, great chemical resistance, outstanding rubber adhesion, and low permeability, result in exceptional performance.
In Orgalloy polyamide alloys, key short-chain polyamide physical and chemical characteristics are combined with the practical and process benefits of polyolefins. In comparison to PA 6 and PA 6.6 resins, they are intended to give superior dimensional stability, a lower density, and better mechanical qualities.
Sl no | Topic |
1 | Market Segmentation |
2 | Scope of the report |
3 | Abbreviations |
4 | Research Methodology |
5 | Executive Summary |
6 | Introduction |
7 | Insights from Industry stakeholders |
8 | Cost breakdown of Product by sub-components and average profit margin |
9 | Disruptive innovation in the Industry |
10 | Technology trends in the Industry |
11 | Consumer trends in the industry |
12 | Recent Production Milestones |
13 | Component Manufacturing in US, EU and China |
14 | COVID-19 impact on overall market |
15 | COVID-19 impact on Production of components |
16 | COVID-19 impact on Point of sale |
17 | Market Segmentation, Dynamics and Forecast by Geography, 2023-2030 |
18 | Market Segmentation, Dynamics and Forecast by Product Type, 2023-2030 |
19 | Market Segmentation, Dynamics and Forecast by Application, 2023-2030 |
20 | Market Segmentation, Dynamics and Forecast by End use, 2023-2030 |
21 | Product installation rate by OEM, 2023 |
22 | Incline/Decline in Average B-2-B selling price in past 5 years |
23 | Competition from substitute products |
24 | Gross margin and average profitability of suppliers |
25 | New product development in past 12 months |
26 | M&A in past 12 months |
27 | Growth strategy of leading players |
28 | Market share of vendors, 2023 |
29 | Company Profiles |
30 | Unmet needs and opportunity for new suppliers |
31 | Conclusion |
32 | Appendix |