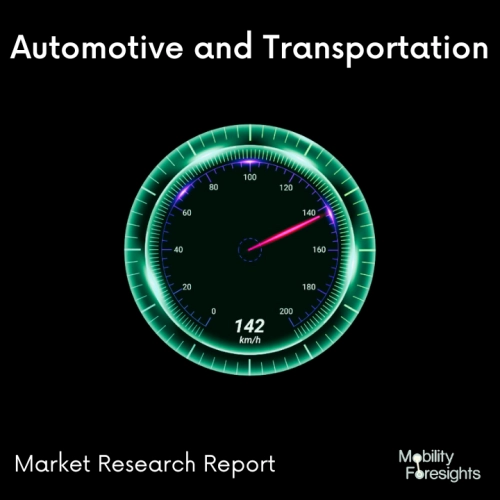
- Get in Touch with Us
Last Updated: Apr 25, 2025 | Study Period: 2023-2030
Coating. Overview- A class of high-performance polymers called polyimides (PI) are renowned for their remarkable chemical, thermal, and mechanical performance characteristics. Generally speaking, polyimides exhibit great thermal stability in both high and low temperatures.
AM-5352 Tape made of polyimide has a single coating and acrylic adhesive. Due to its superior heat resistance and electrical insulation, it is employed in many manufacturing processes for electrical and electronic products.
Through the process of creating film and imine treatment at high temperature, PMDA and ODA are polymerized in strong polar solvents to create polyimide film, the generic name of DuPont's tradename Kapton.
Since polyimides have strong mechanical qualities, they are used in applications that call for tough organic materials, such as As polymers, films, laminating resins, insulating coatings, and high temperature structural adhesives, they can be used. Thermosetting and thermoplastic polyimides are both available.
A polymer having imide groups and falling under the category of high-performance plastics is known as polyimide (often shortened as PI). Polyimides are highly heat resistant and have a variety of uses in industries that need tough organic materials, such as displays, high temperature fuel cells, and different military functions.
Polyurethane resins have a relatively short pot life, phenolic resins breakdown when exposed to UV light repeatedly, and polyimide resins are pricy and display a notable water absorption.
The Global EV Polyimide Silicone Coating market accounted for $XX Billion in 2022 and is anticipated to reach $XX Billion by 2030, registering a CAGR of XX% from 2023 to 2030.
Snab Graphix India Private LimitedManufacturers of exterior parts may be able to replace glass or metal substrates with lighter, stronger, and more workable polymer materials with the use of SilFORT hardcoats.
SilFORT hardcoats can assist extend a polymeric component's durability and performance, retain physical qualities, increase weatherability, and improve resistance to abrasives, chemicals, and solvents by shielding against abrasion and UV exposure.
The employment of SilFORT hardcoat and priming technologies can help polymers maintain their colour, gloss, light transmission, and other physical characteristics over a lengthy period of time.
Our consumers are developing polymeric goods for applications that would otherwise be too demanding for these materials since SilFORT hardcoats can assist in enabling polymers to resist prolonged exposure to outdoor conditions, including severe weather like wind and ice. As a result, glass or metal parts can be replaced with lighter and more durable plastic components.
For the protection of plastics in automotive lighting, glazing, and trim applications, SilFORT hardcoats have been used, and they are encouraging innovation for more fuel-efficient cars in the future.
Additionally, SilFORT solutions can improve security and energy effectiveness in architectural applications. SilFORT hardcoats can provide non-yellowing, top-tier defence against heat and ultraviolet rays thanks to sophisticated UV absorbers.
Sl no | Topic |
1 | Market Segmentation |
2 | Scope of the report |
3 | Abbreviations |
4 | Research Methodology |
5 | Executive Summary |
6 | Introduction |
7 | Insights from Industry stakeholders |
8 | Cost breakdown of Product by sub-components and average profit margin |
9 | Disruptive innovation in the Industry |
10 | Technology trends in the Industry |
11 | Consumer trends in the industry |
12 | Recent Production Milestones |
13 | Component Manufacturing in US, EU and China |
14 | COVID-19 impact on overall market |
15 | COVID-19 impact on Production of components |
16 | COVID-19 impact on Point of sale |
17 | Market Segmentation, Dynamics and Forecast by Geography, 2023-2030 |
18 | Market Segmentation, Dynamics and Forecast by Product Type, 2023-2030 |
19 | Market Segmentation, Dynamics and Forecast by Application, 2023-2030 |
20 | Market Segmentation, Dynamics and Forecast by End use, 2023-2030 |
21 | Product installation rate by OEM, 2023 |
22 | Incline/Decline in Average B-2-B selling price in past 5 years |
23 | Competition from substitute products |
24 | Gross margin and average profitability of suppliers |
25 | New product development in past 12 months |
26 | M&A in past 12 months |
27 | Growth strategy of leading players |
28 | Market share of vendors, 2023 |
29 | Company Profiles |
30 | Unmet needs and opportunity for new suppliers |
31 | Conclusion |
32 | Appendix |