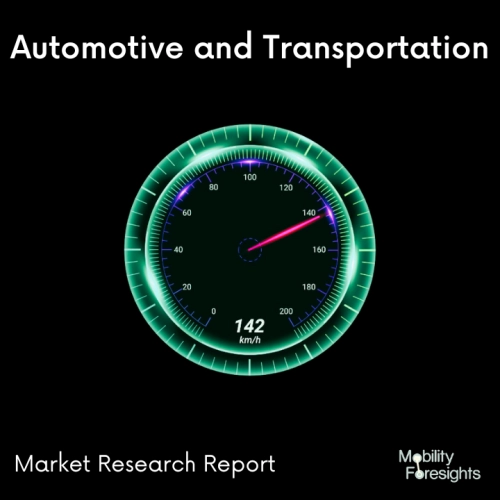
- Get in Touch with Us
Last Updated: Apr 25, 2025 | Study Period: 2023-2030
A polyol ester is blended with sufficient concentrations of an antioxidant, a yellow metal pacifier, and rust inhibitors to create a synthetic lubricant composition.
The polyol ester blend consists primarily of a mixture of poly(neopentyl polyol) ester produced by reacting partial poly(pentaerythritol) esters with at least one carboxylic acid and an ester produced by reacting a polyol with at least two hydroxyl groups and at least one carboxylic acid.
Prefer linear acids over ones that might release smells when used. Secondary arylamine antioxidants, a triazole derivative yellow metal pacifier, an amino acid derivative, and substituted primary, secondary, and/or diamine amine rust inhibitors are examples of useful additions.
This invention pertains to compositions including synthetic esters, more specifically compositions based on a mixture of poly(neopentyl) polyol ester and an ester of a polyol containing at least two hydroxyl groups, which is inhibited with a special mix of additives.
The compositions are particularly well suited for use as a coolant/lubricant in a rotary screw air compressor. The coolant/lubricant compositions use the least amount of esters produced from strongly odoriferous acids while still offering a longer lifespan, higher temperature operation, excellent demulsibility, biodegradability, rust protection, and hydrolytic stability a combination of qualities not present in currently available synthetic compressor coolant/lubricant compositions.
The Global EV Polyol esters coolantMarket accountedfor $XX Billion in 2022 and is anticipated to reach $XX Billion by 2030, registering a CAGR of XX% from 2023 to 2030.
The primary ingredient in many refrigeration lubricants is polyol ester (POE). In this study, the density and viscosity of pentaerythritol tetra hexanoate, a typical, pure polyol ester, were measured and predicted using molecular dynamics simulations. A method for performing a NEMD-Eyring fit was suggested for a low-error, repeatable, and reliable Newtonian viscosity calculation.
Rotary screw compressors are known to use hydrocarbon lubricating lubricants. Rotor seals, bearing lubrication, compressed gas cooling, and condensed water removal are all accomplished by oil. The hydrocarbon oils quickly degrade and turn into sludge due to the high temperature, pressure, and presence of water.
Synthetic esters are being used as base stocks in air compressor coolants as a result of efforts to increase their useful life. Physical characteristics including effective cooling, low temperature start-up, sealing of the rotors, and bearing lubrication are also necessary in addition to these performance characteristics.
Water condensed from compressed air will come into touch with all coolants and lubricants used in screw compressors. Therefore, any lubricant must have strong hydrolytic stability and offer effective protection against rust and corrosion.
The availability of a lubricant with good demulsibility is a bonus. This will make it possible to separate the water from the used lubricant and make it easier to dispose of and recycle the used lubricant.
Increased biodegradability is also highly desirable. It is also preferable from an environmental standpoint to get rid of the heavy metals that are present in some commercial coolants.
Sl no | Topic |
1 | Market Segmentation |
2 | Scope of the report |
3 | Abbreviations |
4 | Research Methodology |
5 | Executive Summary |
6 | Introduction |
7 | Insights from Industry stakeholders |
8 | Cost breakdown of Product by sub-components and average profit margin |
9 | Disruptive innovation in the Industry |
10 | Technology trends in the Industry |
11 | Consumer trends in the industry |
12 | Recent Production Milestones |
13 | Component Manufacturing in US, EU and China |
14 | COVID-19 impact on overall market |
15 | COVID-19 impact on Production of components |
16 | COVID-19 impact on Point of sale |
17 | Market Segmentation, Dynamics and Forecast by Geography, 2023-2030 |
18 | Market Segmentation, Dynamics and Forecast by Product Type, 2023-2030 |
19 | Market Segmentation, Dynamics and Forecast by Application, 2023-2030 |
20 | Market Segmentation, Dynamics and Forecast by End use, 2023-2030 |
21 | Product installation rate by OEM, 2023 |
22 | Incline/Decline in Average B-2-B selling price in past 5 years |
23 | Competition from substitute products |
24 | Gross margin and average profitability of suppliers |
25 | New product development in past 12 months |
26 | M&A in past 12 months |
27 | Growth strategy of leading players |
28 | Market share of vendors, 2023 |
29 | Company Profiles |
30 | Unmet needs and opportunity for new suppliers |
31 | Conclusion |
32 | Appendix |