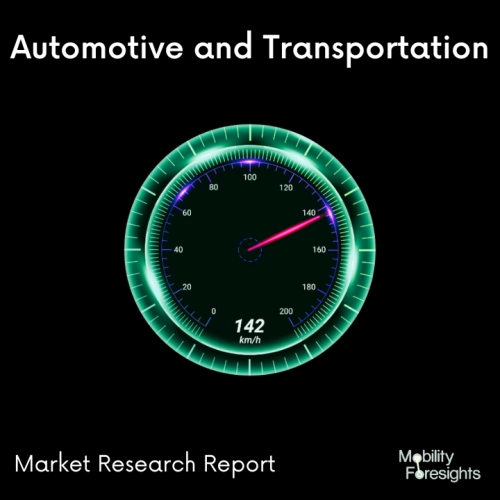
- Get in Touch with Us
Last Updated: Apr 25, 2025 | Study Period: 2023-2030
The high-performance resin polyphthalamide, also known as PPA, belongs to the nylon family and has remarkable thermal, mechanical, and physical qualities. It is semicrystalline, opaque, hygroscopic, and suitable for injection moulding.
In order to increase stiffness for high-temperature applications where Nylon 66 would not work, the majority of PPA grades are filled (with glass and/or mineral).
PPA is employed in areas where a metal or more expensive thermoplastic would typically be used instead. It is frequently used in industrial applications that call for low moisture sensitivity, good chemical resistance, high heat resistance, and automotive, electronics, and electrics.
Terephthalic acid, isophthalic acid, or a mixture of the two, and at least one aliphatic diamine, such as hexamethylene diamine, are the building blocks of polyphthalamide.
These resins are only partially aromatic since the aromatic acid portion only makes up at least 55 molar percent of the repeat units in the polymer chain. The polymer's aromatic backbone increases rigidity, rigidity at high temperatures, chemical resistance, and heat stability while decreasing moisture absorption.
The improved qualities cost money, though. Phthalimides have a higher melting point than conventional aliphatic amides, which makes them more expensive and more challenging to manufacture.
Improved chemical resistance, warpage, better strength & stiffness at high temperatures, creep & fatigue resistance, sensitivity to moisture absorption, and dimensional stability are some of the traits of polyphthalamide.
As the amount of terephthalic increases, the glass transition temperature of PPA rises. A copolymer is considered to be amorphous if isophthalic makes up more than 55% of the acidic portion of a PPA.
Above the glass transition temperature but below the melting point, crystallinity aids in mechanical characteristics and chemical resistance. Warpage and transparency are ideal for amorphous PPA polymers.
The Global EV Polyphthalamide (PPA) market accountedfor $XX Billion in 2021 and is anticipated to reach $XX Billion by 2030, registering a CAGR of XX% from 2022 to 2030.
A new series of high-performance polyphthalamide (PPA) compounds called Amodel Supreme PPA is offered by Solvay. It is intended for demanding e-mobility and metal replacement applications.
Solvay's Amodel Supreme PPA, the first PPA product and the industry leader in PPA chemistry, provides systems that demand superior thermal, mechanical, and electrical qualities with a higher level of performance.
Applications include housings for high-temperature electrical connectors, power electronics, e-motors and other high-temperature automotive components used in electric drive units, electric and electronic devices, and telecommunication equipment components that require outstanding heat resistance.
The sustained investment by Solvay in Amodel PPA shows a strong dedication to PPA and the automobile industry's transition to e-mobility. Amodel PPA Supreme and Amodel PPA BIOS, two new product lines that the business just unveiled, are made to fulfil the increasingly demanding needs of e-motors, power electronics, and batteries.
Sl no | Topic |
1 | Market Segmentation |
2 | Scope of the report |
3 | Abbreviations |
4 | Research Methodology |
5 | Executive Summary |
6 | Introduction |
7 | Insights from Industry stakeholders |
8 | Cost breakdown of Product by sub-components and average profit margin |
9 | Disruptive innovation in the Industry |
10 | Technology trends in the Industry |
11 | Consumer trends in the industry |
12 | Recent Production Milestones |
13 | Component Manufacturing in US, EU and China |
14 | COVID-19 impact on overall market |
15 | COVID-19 impact on Production of components |
16 | COVID-19 impact on Point of sale |
17 | Market Segmentation, Dynamics and Forecast by Geography, 2023-2030 |
18 | Market Segmentation, Dynamics and Forecast by Product Type, 2023-2030 |
19 | Market Segmentation, Dynamics and Forecast by Application, 2023-2030 |
20 | Market Segmentation, Dynamics and Forecast by End use, 2023-2030 |
21 | Product installation rate by OEM, 2023 |
22 | Incline/Decline in Average B-2-B selling price in past 5 years |
23 | Competition from substitute products |
24 | Gross margin and average profitability of suppliers |
25 | New product development in past 12 months |
26 | M&A in past 12 months |
27 | Growth strategy of leading players |
28 | Market share of vendors, 2023 |
29 | Company Profiles |
30 | Unmet needs and opportunity for new suppliers |
31 | Conclusion |
32 | Appendix |