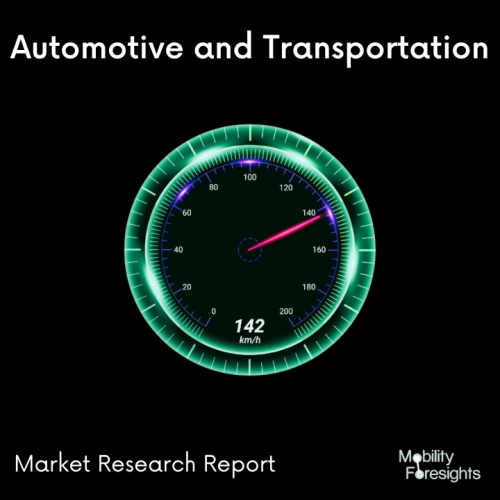
- Get in Touch with Us
Last Updated: Apr 25, 2025 | Study Period: 2024-2030
The global EV powder coating market is touted to grow at a tremendously high rate backed by the rapidly growing electric vehicles around the world, as powder coatings are very crucial for improving durability, aesthetics, and durability of the EV component parts such as the battery, chassis, exterior finishes, and more.
It features technological advances in heat management and improvement of corrosion resistance, with customized paint to meet the requirements of the EV manufacturers. These benefits to energy and efficiency result in in-time management and treatment regimens.
Powder coating finds its way into the manufacturing processes of major automotive OEMs for reasons of efficiency and aesthetics, while adherence to very stringent safety and regulatory standards is maintained. Geographically, North America, Europe, Asia Pacific, and others are promoting market growth through government incentives for electric vehicles and investment in charging infrastructure.
Some of the challenges facing the EV powder coating markets include substrate compatibility and paint compatibility, but innovations in resin chemistry, application technologies, and sustainable practices will surely satiate this market as the world shifts towards electromobility. As it happens, the EV powder market is projected to have much broader coverage, hence giving manufacturers a chance to innovate and cater to evolving demands within the automotive industries.
Powder coating is a dry finishing process whereby finely ground particles of pigments and resin are electrostatically charged and then sprayed onto electrically grounded surfaces. The particles, on impact, cling to the surface and, with heat, cure to a smooth, hard finish.
Advantages of Powder Coating for EVs
Durability: This is a hard finish resistant to chips, scratches, and corrosion, an important feature in-vehicle components.
Environmental Benefits: No solvents are used in it, and the quantum of VOCs emitted is very low, making it environment-friendly.This procedure is capable of producing high transfer efficiency; most of the overspray can be recovered and reused.
High-Temperature Resistance: The component is used for high-temperature-resistant parts such as motor parts and battery housings.
EV powder coating is one of the critical technologies for EV manufacturers in terms of excellent durability, environment, and outstanding aesthetic quality. Coupled with the rise in EV demand, innovations in powder coating technologies will still be among the most vital factors to help drive improved performance and sustainability in electric vehicles.
EV POWDER COATINGSMARKET SIZE AND FORECAST
The Global EV Powder Coatings Market was valued at $XX billion in 2023 and is projected to reach $XX billion by 2030, with a compound annual growth rate (CAGR) of XX% from 2024 to 2030.
Advanced thermal coatings
The EVs require effective thermal management to optimize the performance of their batteries and increase their lifespan; as a result, there is an increased demand for powder-coating solutions that ensure high thermal efficiency. These coatings help to maintain appropriate temperatures in both batteries and electronics.
Coatings for high voltage insulation
Since EV battery systems operate with high voltage, they require power coatings with good electrical insulation properties to avoid electrical accidents. Notable innovations include coatings capable of withstanding and resisting high-energy pressure electrical arcs, assuring safety and reliability in the operation of an EV.
Mechanical durability and storage improvement
Resilience in the face of highly aggressive environmental conditions or mechanical loads is what EVs have to be ready for. With regard to this, powder coatings can play a vital role in ensuring perfect durability, scratch resistance, and corrosion protection of the outer parts of the vehicle, such as brake calipers, chassis, and other components.
Interpon A1243
AkzoNobel Powder Coatings has developed Interpon A1243, a new addition designed for the global electric vehicle powder coatings market, in particular, to enhance and protect brake calipers. This new type of powder coating answers increasing demands from automotive OEMs focused on EVs and high-performance vehicles. It provides vibrant colors and finishes in bright yellow, red, blue, and green with metallic effects that keep pace with the trends in automotive design. These coatingsânot only pleasing to the eyeâare formulated to provide robust mechanical performance and strength against the severe requirements of modern EV braking systems.
AquaEC Flex
Axalta has developed a new electrocoat designed for the global electric vehicle powder coating market. It is a material of sustainability, featuring a wide thermal curing window, emission reduction, removal of hazardous materials, and water re-use. AquaEC Flex provides excellent Elektro system appearance and protection from edge scratch, offering advanced flexibility. This developing technology will help automotive OEMs to make operations more efficient by putting traditional electric vehicles and combustion engines on the same workflow. AQIC Flex ensures that critical componentsâeven the part that holds and protects the batteryâattaches well to the car body for durability and performance.
Rilsan T Orange 7706 and Rilsan ESY Orange
Arkema has announced the launch of innovative polymer solutions it developed for the global electric vehicle EV powder coatings market targeting high-energy insulation. These new products received UL Yellow Card certification for use in specific busbar insulation, underlining their suitability for EV battery systems and associated applications. New introductions include two polyamide 11 powder coating grades under the Rilson brand. Rilsan T Orange 7706 is designed for primer-free liquid bed insertion and enables coating with a large thicknessâ500 µm in a single dip. Rilsan ESY Orange 7705 is a primerless electrostatic coating grade for applications requiring thin insulation layers. Both grades achieved impressive ratings in excess of 600 volts in CTI and were classified as UL 94 V-0 for fire resistance. Arkema Polyamide 11 products are especially known for their flexibility, ease of processing, and bio-based origin, derived entirely from castor oil.
The Effects Collection, a new powder coating line from Polychem Powder Coatings, was introduced. 11 powder special effects from the Polychem Effects Collection are offered in many more colors than those depicted on the collection ring.
Speckles, translucents, metallics, sparkle translucents, veins, patina effects, river textures, fine textures, and dramatic illusion colors are just a few of the special effects.
Our customers wanted to see a good selection of the effect alternatives that would be accessible to them, said Lauren Bayer, manager of Polychem, who specializes in powder special effects. This collection highlights some of our most well-liked effects and allows for debate of the available colors and whether bespoke color versions are conceivable.
Sr.N | Topic |
1 | Market Segmentation |
2 | Scope of the report |
3 | Research Methodology |
4 | Executive Summary |
5 | Average B2B by price |
6 | Introduction |
7 | Insights from Industry stakeholders |
8 | Key Drivers for Global EV(Electric vehicle) Powder Coatings market |
9 | Disruptive Innovation in the Industry |
10 | Overview of Global EV(Electric vehicle) Powder Coatings market |
11 | Major impact on Technological advancements |
12 | Consumer trends in the industry |
13 | Recent technological trends in Global EV(Electric vehicle) Powder Coatings market |
14 | SWOT Analysis of Key Market Players |
15 | New product development in the past 12 months |
16 | Market Size, Dynamics, and Forecast by Geography , 2024-2030 |
17 | Market Size, Dynamics, and Forecast by Resin Type, 2024-2030 |
18 | Market Size, Dynamics, and Forecast by Functionality, 2024-2030 |
19 | Market Size, Dynamics, and Forecast by Application, 2024-2030 |
20 | Competitive landscape |
21 | Gross margin and average profitability of suppliers |
22 | Merger and Acquisition in the past 12 months |
23 | Growth strategy of leading players |
24 | Market share of vendors, 2023 |
25 | Market Company Profiles |
26 | Unmet needs and opportunities for new suppliers |
27 | Conclusion |